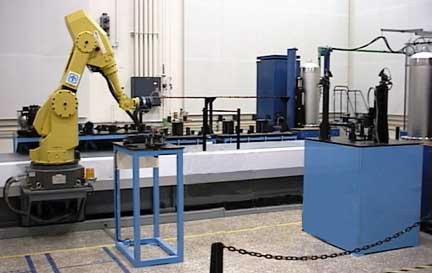
The Nuclear Weapons Complex stores radioactive nuclear materials known as “pits”. At the Pantex Plant in Amarillo, Texas, several stockpile inspection, evaluation, and maintenance programs require the handling and measurement of pits from a wide variety of weapons systems. These measurements are performed to ensure stockpile integrity. Historically, pit-handling operations were performed manually, resulting in accumulations of radiation doses for workers. With the Weigh and Leak Check System (WALS), that is no longer the case.
WALS was a joint effort by High Consequence, Automation, & Robotics (HCAR) who developed the robotic automation system and by Pantex who developed the weigh and leak check stations. Pantex is currently using WALS to perform remote weigh and leak check operations on its nuclear weapon pits. WALS is the first robot system ever to handle such stockpile pits.
Technical Challenges
The handling of stockpile pits is a high-consequence task as any system failure could result in significant and catastrophic consequences. Having a robot system that has the necessary capabilities to safely, precisely, and gently handle the pits is critical. In addition, having a robotic system that is not only designed to be robust to a wide variety of potential failure modes, but is also able to fail in a safe manner in the event of a failure is extremely critical. Finally the system has to be at least as efficient and effective as the current standard process to ensure there are no negative impacts to current and future operations.
Features
WALS uses a 6-axis robotic arm on a 25 ft. linear track. The robotic arm is programmed to move pits to custom tooling and automation stations, where the pits are unpacked from their containers, removed from their shipping fixtures, weighed, leak-checked, and repacked. WALS also has a suite of sensors and safety features necessary to operate the robot safely and reliably. Other features include:
- Computer vision to determine the position of objects in the workcell, eliminating the need for large numbers of precise fixtures.
- Force feedback control allows the robot system to sense forces on the payload, thereby protecting the payload and providing an automated means to precisely and gently place pits in the workcell.
- Mechanical locks and sensors that ensure a sequence of events occurs before a pit can be moved.
- A redundant computer to independently monitor forces on the pit during robot motion.
As an upgrade, Sandia has also modified the robot’s pit-handling tools so the system can accommodate new sealed insert (SI) containers, in addition to the several containers already used in the WALS system.
Benefits
The primary benefit was a significant reduction in operator exposure to radiation by eliminating manual handling of pits. Another important ergonomic benefit is the elimination of many of the manual lifting tasks that are required for unpacking and repacking the pits. Furthermore, the automation process enforces qualified, validated procedures, that will be executed the same each time ensuring a high quality operation. This sequence of performed operations automatically generates a log that can be retained and audited, thus improving overall quality.
Applications
The automation technologies developed for WALS can be employed in a wide variety of areas where pits are handled. This will dramatically extend the scope of these technologies well beyond their original use in the weigh and leak check facility.
Contact Us
Questions and comments about High Consequence, Automation, & Robotics? Contact us.
In the News
Never-Tiring Robots Help Dismantle Nuclear Weapons Faster, More Safely