The use of High Performance Computing recently led to a remarkable breakthrough in the optimization of thermo-mechanical properties for an alloy of platinum and gold, an elemental combination that is ideal for a wide range of electrical applications due to the oxidation resistance of these constituents. Sandia researchers showed that the structure and composition of this noble metal alloy can be tailored in a way that produces extraordinary resistance to deformation, fatigue, and wear. This work triggered the development of high-throughput computational and experimental methods for material design that researchers are now using to optimize far more complex alloys for mechanical strength and resistance to extreme temperature.
HPC tools enable Sandia to test many alloy combinations in a short amount of time, spanning a divide that covers millions of combinations of alloys with diverse characteristics.
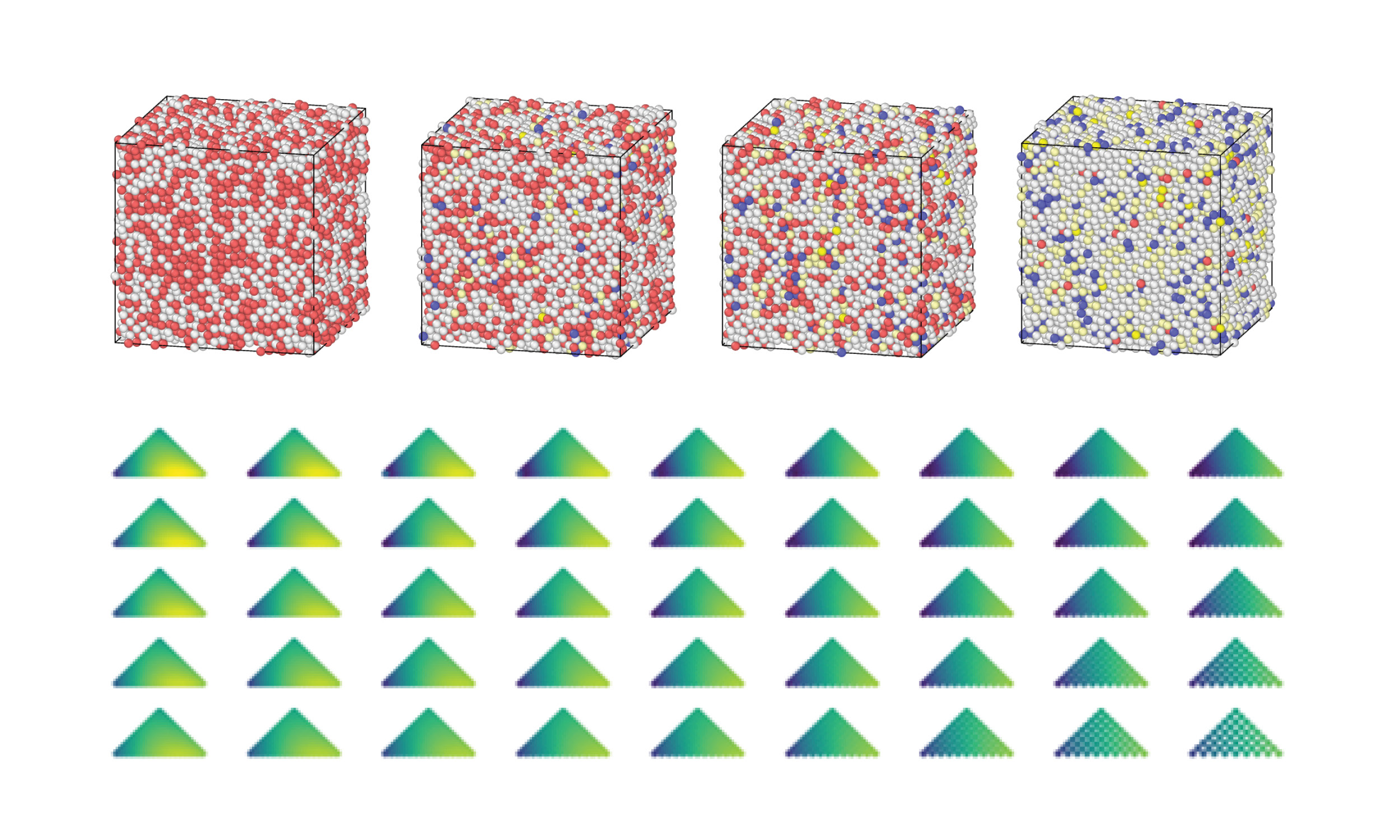
By coupling cutting-edge theory and testing, including high-throughput, machine learning-optimized molecular dynamics simulations, additive manufacturing synthesis methods, and mechanical property testing, it is possible to rapidly scan the vast compositional space of advanced alloys and find optimal configurations for high-strength, melting temperature, etc.
Researchers developed these novel techniques from a confluence of practical questions collected over decades from a wide range of customer needs. A common theme identified was metal electrical contacts, that depend on shearing metal junctions with minimal wear and without destroying the electrically conductive pathway. Many materials with properties ordinarily superior to metals, e.g., diamond-like carbon coatings, with typically far higher wear resistance, are obviated due to a lack of conductivity. The physics of metal interfaces is complicated not only because of the details of metals’ deformation, but also due to influences from the environment that can compound problems through oxidation or corrosion. Distilling the basics of the problem—structure-dependent deformation mechanisms, led to new fundamental insights about the aspects of alloys that could be tuned to better resist failure and wear, even in complicated environments.
Researchers initially worked on core concepts to more rigorously understand the fundamental physics (e.g., the mechanisms of deformation) and how practical considerations such as the environment can influence these in real-world applications. They then pursued cutting-edge applied R&D in parallel with systematic, targeted fundamental investigations to identify opportunities to tweak materials in a way that can ‘shut down’ or greatly mitigate failure modes. This combination of fundamental concepts and cutting-edge theory focused research on materials optimization and investigations of failure mechanisms in three ways.
The first research focus developed a theoretical model that predicts the peak strength of polycrystalline metals based on the activation energy (or stress) required to cause deformation. Building on extensive earlier work, this model is based purely on materials’ properties, requires no adjustable parameters, and is shown to accurately predict the strength of four exemplar metals. This framework reveals new routes for design of more complex high-strength materials’ systems, such as compositionally complex alloys, multiphase systems, nonmetals, and composite structures.
The success of this model in predicting the strength of metals leads to two major conclusions. The first is that in the absence or suppression of dislocation slip, the maximum strength of any metal is determined by the heat of fusion, and thus is a value that can be relatively easily determined. The second conclusion is that it is possible to directly design alloys for maximum strength by calculating and optimizing this property. This has strong implications in a variety of fields but seems particularly of value in the cases of high-entropy or compositionally complex alloys, where the design space is highly multidimensional.
HPC enables optimization of thermo-mechanical properties of a vast range of alloys, producing extraordinary resistance to deformation, fatigue and wear.
The second research focus, based off of recent work from the Massachusetts Institute of Technology, suggests that thermally stable nanocrystallinity in metals is achievable in several binary alloys by modifying grain boundary energies via solute segregation. Researchers at Sandia fabricated such an alloy out of platinum and gold and found that this alloy exhibited extraordinarily low wear. The potential practical impacts of ultralow wear noble (i.e., oxidation resistant) alloys are significant in many applications, though perhaps most notably in electrical contacts, where bare metal contacts remain an intrinsic requirement for maintaining electrical conductivity across sliding and rolling interfaces. A highly stable nanocrystalline noble metal alloy could address persistent roadblocks to widespread adoption of this technology. The demonstration of fatigue resistance and high strength of a stable nanocrystalline alloy also suggests promising opportunities for this class of alloys as structural materials.
The third research focus lies in the optimization of metal alloys, specifically complex concentrated alloys that are typically made of four or more elements in nearly equal concentrations. A high-throughput simulation approach allows researchers to rapidly scan potential alloys and identify what may be ideal or optimal properties. HPC allows a streamlined approach to this complicated problem. Implications of this work suggest that validating the properties of the compositions predicted by the simulations with high-throughput processing (via additive manufacturing) and characterization (via hardness/scratch testing) can enable rapid screening of complex concentrated alloys, and thus lead to novel materials with optimal properties for structural applications.
Sandia researchers may use this technology to produce unusual and practical results that industry partners can use to address emerging needs for DOE applications, including aerospace systems, power generation, and gas turbines for high efficiency.
The search for optimal alloys grows increasingly complicated as the number of their constituents grows. In the near future, researchers at Sandia hope to add additional properties, such as determination of heat of fusion, as a way to further accelerate the HPC-enabled iterative high-throughput optimization process. Additional capabilities, such as extreme temperature mechanical testing, will also concurrently accelerate this process and enable Sandia to achieve the ambitious goal of rapidly developing tailored alloys for any unique application.