Predicting plasticity and damage evolution in metal components during mechanical loading environments is critical to ensuring the nation’s nuclear stockpile remains safe, secure and reliable. However, doing so remains extremely challenging due to the myriad processes occurring at the microstructural level. As part of a Laboratory Directed Research and Development project focused on predicting material failure using deep learning, researchers evaluated damage evolution in the 2219 aluminum alloy using diffraction contrast tomography, or DCT, and in-situ X-ray computed tomography, or CT, in conjunction with high-fidelity modeling.
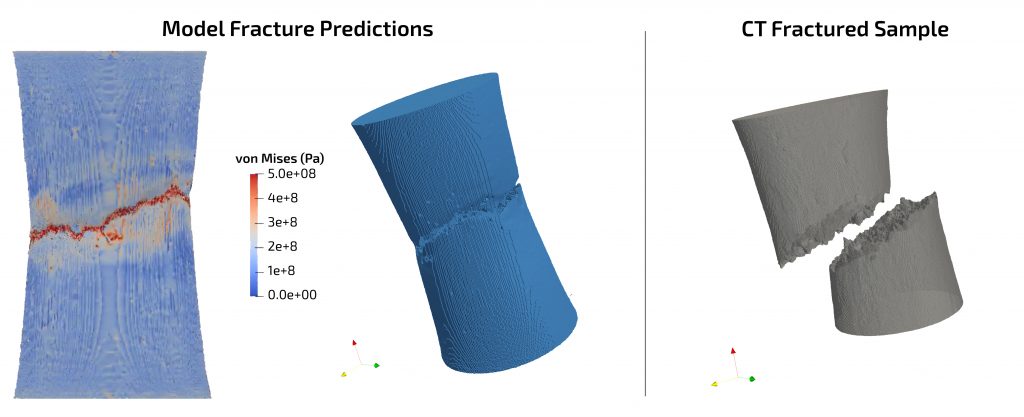
In the experimental effort, using a Zeiss Xradia Versa system, pre-test, nondestructive DCT scans delivered 3D reconstructions of crystallographic size, shape and orientation. During subsequent tensile testing, researchers used in situ CT scans to quantify initial Al2Cu second-phase particle and void distributions, as well as emerging void nucleation, growth and coalescence leading to fracture. After testing, the researchers performed serial sectioning within an electron microscope using the state-of-the-art TriBeam system, resulting in 3D reconstructions of deformed grain structure and orientation and providing insight into microstructural evolution and damage accumulation.
In the computational portion of the project at the continuum scale, the initial pre-test CT scan was segmented, reconstructed and converted to hexahedral finite elements using Cubit/Sculpt, resulting in a mesh containing over 8.1 M elements. Researchers calibrated continuum plasticity and damage models to macroscale stress-strain behavior for the aluminum matrix, while second-phase particles were treated as elastic based on nano-indentation results. Sierra/SolidMechanics was then employed to predict the plastic deformation, damage evolution and eventual failure. Crack initiation was modeled through element death based on a critical damage value. This simulation utilized 1,656 central processing units, or CPUs, on the Attaway cluster for 48 hours. When compared to post-test CT scans, the predictions for crack path and fracture surface appear qualitatively similar. At the mesoscale, DCT data was converted to a finite element mesh and directly used in a crystal plasticity simulation, allowing for the study of stresses and strains in individual metal grains. Combined with DCT and in situ CT, these simulation results allow modelers to study the effects of crystallographic orientation on void nucleation. Notably, in addition to the effects of initial grain orientation, the crystal plasticity results uncovered relationships between void nucleation and grain rotation during loading, which allowed for the discovery of correlations that were not present in initial orientations.
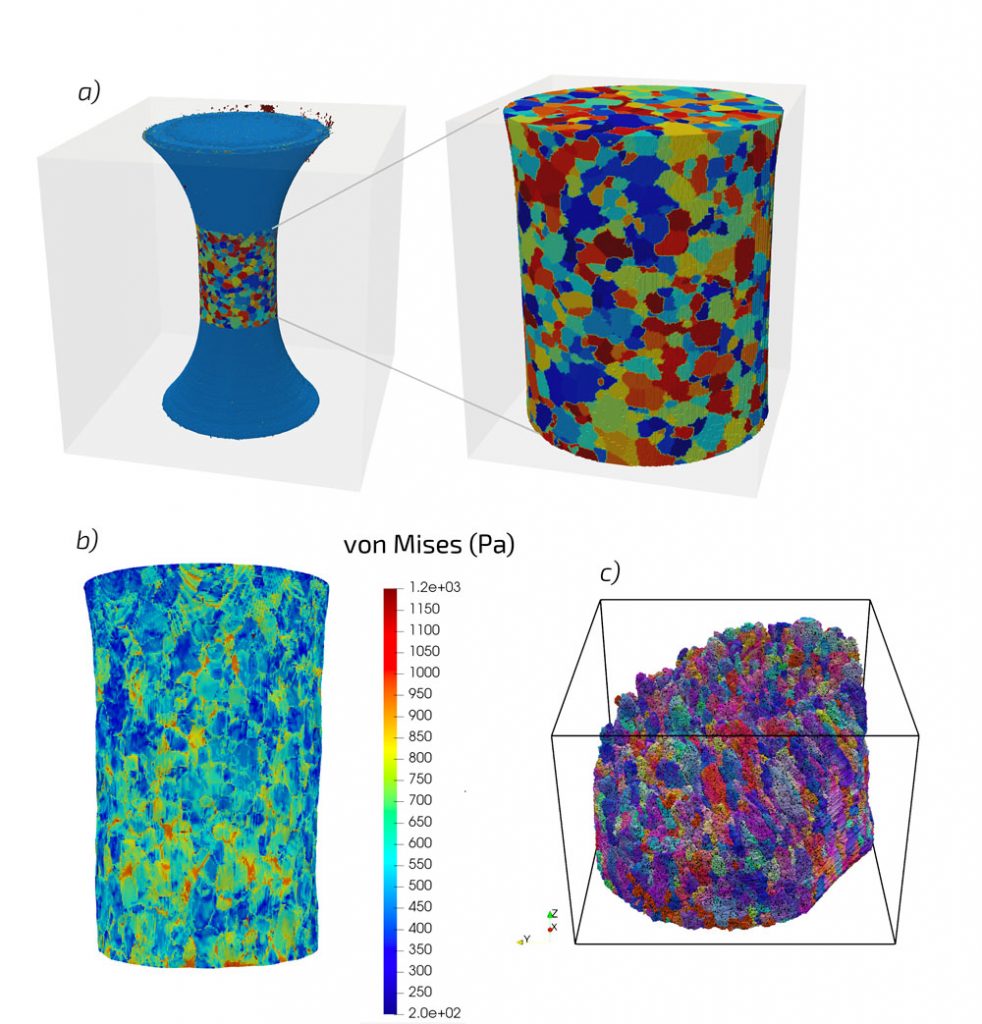
The results of this combined experimental and computational approach have provided great insight into microstructural deformation mechanisms as well as improved workflows. The researchers developed a streamlined approach to go directly from CT scan to finite element model while still considering different material phases present in the sample. Analyzed in situ, CT data has provided unparalleled detail into void formation and evolution, which will allow future researchers to calibrate damage models by using measured information on void evolution rather than stress-strain data alone. This improvement will enable better predictions of mechanical performance of structural components. Combined DCT, in situ CT and post-test TriBeam characterization has enabled for the first time at Sandia a direct comparison between mesoscale model predictions and experiments as well as insight into the local, grain-level stress states and their effect on damage evolution. Finally, these simulations are currently serving as training data for the development of Deep Learning algorithms in an effort to rapidly predict failure of components based on loading conditions and microstructural features.
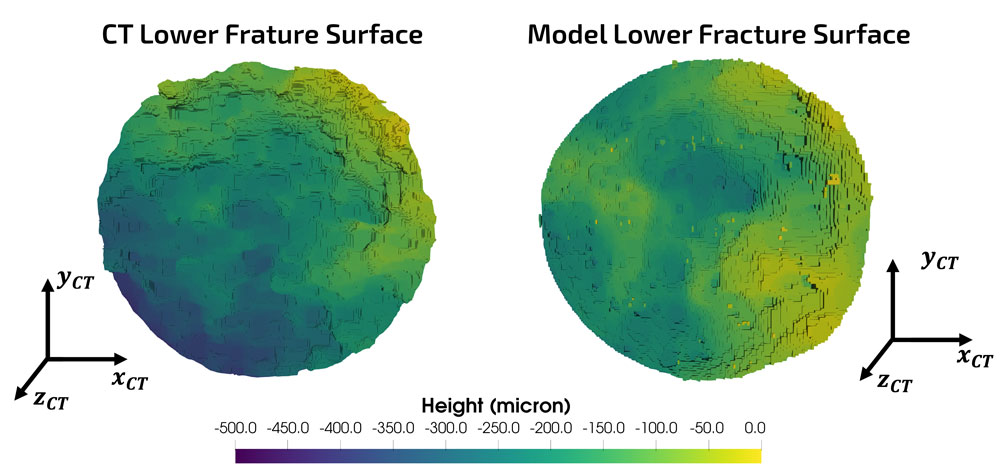