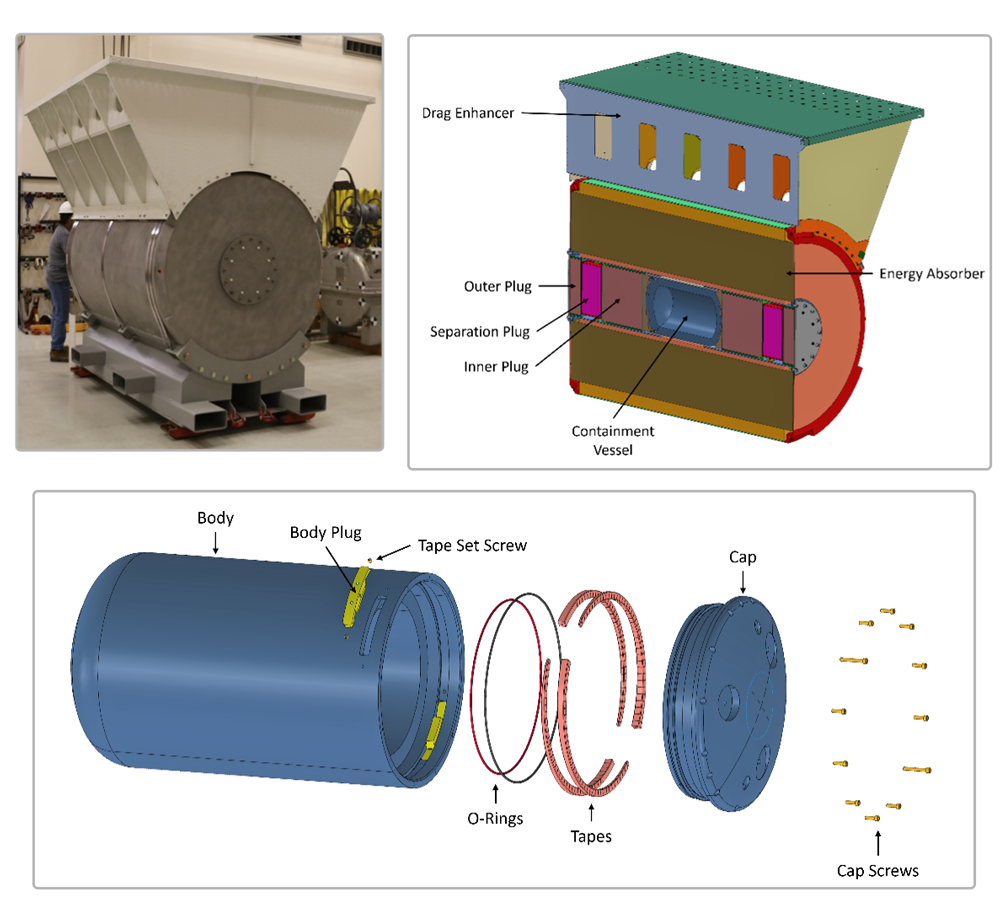
Sandia researchers have developed a large plutonium air transportation (LPAT) package that utilizes HPC resources and test facilities. This package is capable of transporting hazardous plutonium materials over-the-road or by air and was designed to satisfy the plutonium air transport safety criteria specified by U.S. regulations. These regulations stipulate that a hazardous materials transportation package must maintain containment of its hazardous contents, provide sufficient shielding against radiation leakage from the package and prevent the package contents from going critical during an accident. The regulations define a series of hypothetical accident condition (HAC) tests for which the package must be designed. These tests are intended to bound realistic accident scenarios.
Of the eight defined tests, the impact and fire tests are by far the most challenging to withstand. Six tests are to be applied sequentially:
- Impact: the impact of the package at a velocity of at least 129 m/s into a flat, essentially unyielding surface
- Static Load: the application of a 312 kN static compressive load on the package
- Puncture: the drop of the package from a height of 3 m onto a steel puncture probe
- Slash: two sequential impacts of a steel angle dropped from a height of 46 m onto the package
- Fire: the exposure of the package to a fully engulfing jet-fuel pool-fire for 60 minutes
- Immersion: the immersion of the package in water to a depth of at least 0.9 m
Two are stand-alone tests:
- An individual terminal velocity impact test, which is only required if the package’s terminal velocity is greater than 129 m/s
- A deep submersion test where an undamaged package is submerged in water and subjected to an external water pressure of 4 MPa
The LPAT package (Figure 1) is cylindrical in shape with a diameter of 1.5 m and a length of 2.0 m. It has a mass of about 4400 kg. The package consists of three primary safety critical components: a Containment Vessel (CV), an Energy Absorber (EA) assembly and a Drag Enhance (DE). The high strength stainless steel CV prevents the release of radioactive material contents and provides shielding to limit radiation exposure to those around the package. The CV, which is about 380 mm in diameter and 700 mm long, is enclosed within the EA assembly. The EA assembly, which includes a body and six plugs, protects the CV from mechanical and thermal loads generated during the specified regulatory tests. The EA assembly components are comprised mostly of a unique composite material developed at Sandia that is made from successive layers of perforated aluminum sheets and Kevlar® fabric. This composite material provides excellent energy absorption, as well as exceptional structural and thermal protection. The DE is a lightweight aluminum structure that limits the free-fall terminal velocity of the package to less than 129 m/s. The DE was designed using Sandia’s HPC resources and fluid dynamics analysis code (Figure 2).
Figure 2. Drag enhancer fluid dynamics simulation.
An initial design for the LPAT package was developed from an earlier and smaller preliminary PAT package developed at Sandia. An engineering unit of the initial design was built and subjected to testing that intended to prove-out the feasibility of such a large PAT package. In 2013, the engineering unit was impacted at 133.8 m/s into a large concrete target at Sandia’s 600 m rocket sled track facility. It was subsequently burned for 60 minutes in a jet-fuel pool fire at Sandia’s Lurance Canyon Burn Site. Results of the tests demonstrated that a plutonium air transport package of the size of the LPAT package was feasible.
Figure 3. Comparison of the FEM response with the outcome of the engineering unit impact test.
Data from the tests were used to construct a detailed finite element model (FEM) of the package (Figure 3) for use with Sandia’s SIERRA Solid Mechanics (SIERRA/SM) finite element analysis code. The half-symmetry model, consisting of 2.5 million elements, was used to refine the initial package design. Hundreds of simulations were completed using Sandia’s HPC resources for each new design iteration to assess its response to the accident condition scenarios, culminating in a final package design in 2016. The half-symmetry final design model comprises approximately 4.2 million elements and has been used extensively in certification evaluations of the LPAT package.
Figure 4. Corner certification impact test (real time).
Figure 5. Comparison of the FEM response with the outcome of the corner certification impact test.
A Safety Analysis Report for Packaging (SARP) is a document that describes the design and safety-critical features of a package and provides the technical evidence demonstrating that the package meets the regulatory requirements applicable to the package. In December 2019, a 1600+ page LPAT package SARP was submitted to regulators. Thousands of normal and accident condition simulations, completed over several years on Sandia’s HPC machines, provided most of the data used to establish the performance of the package against regulatory requirements. Results from a series of plutonium air transport certification tests are also described in the SARP. Data derived from the extensive set of simulations completed for the LPAT package provided a wealth of information to the design team, allowing them to identify the critical test scenarios that eventually comprised the certification test series. In 2018, three packages, in three impact orientations, were tested at Holloman Air Force Base: corner (see Figures 4 and Figure 5), side and end. The side orientation impact velocity was 131.2 m/s, corner orientation was 137.1 m/s and the end orientation was 139.2 m/s. Following the impact tests, the corner impact package was subjected to the remaining sequence of regulatory tests, including a fire test (Figure 6). Results from the tests demonstrated the exceptional performance of the LPAT package under the plutonium air transport HAC test scenarios.
Figure 6. Certification fire test.