The Waste Isolation Pilot Plant (WIPP) is an operating geologic repository in southeastern New Mexico for transuranic (TRU) waste from nuclear defense activities. Nuclear waste containers are placed underground in a disposal room at the WIPP, and then the surrounding rock salt creeps inward to compress the containers over several centuries, thereby isolating the waste from the biosphere.
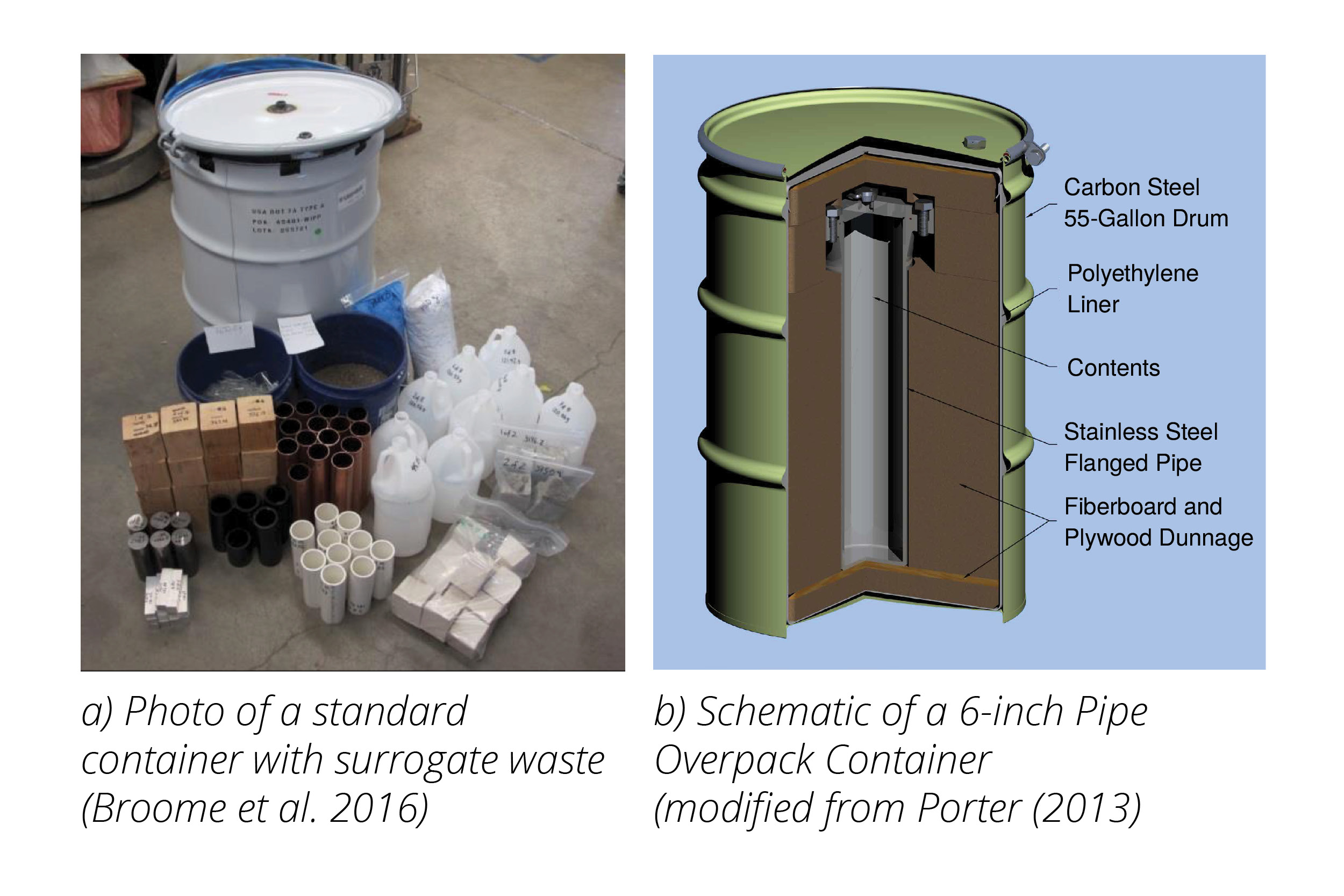
Past simulations of container compaction at the WIPP have homogenized the containers into a solid, spatially uniform material. As shown in Figure 1a, standard waste containers are 55-gallon drums filled with all types of contaminated debris: cellulosics, metals, sorbants, and polymers. These containers are typically bundled together in hexagon shaped seven-packs: six containers surround one container in the center. Upon emplacement in a WIPP disposal room, the seven-packs are stacked up to three-high and arranged in a hexagonal configuration (see Figure 2a). Geomechanical models developed in the 1980s and 1990s, however, replaced the complexity in Figure 2a with the idealized geometry in Figure 2b. Instead of including every individual container, the models represented all the containers by a single, isotropic material (see, for example, Stone (1997).
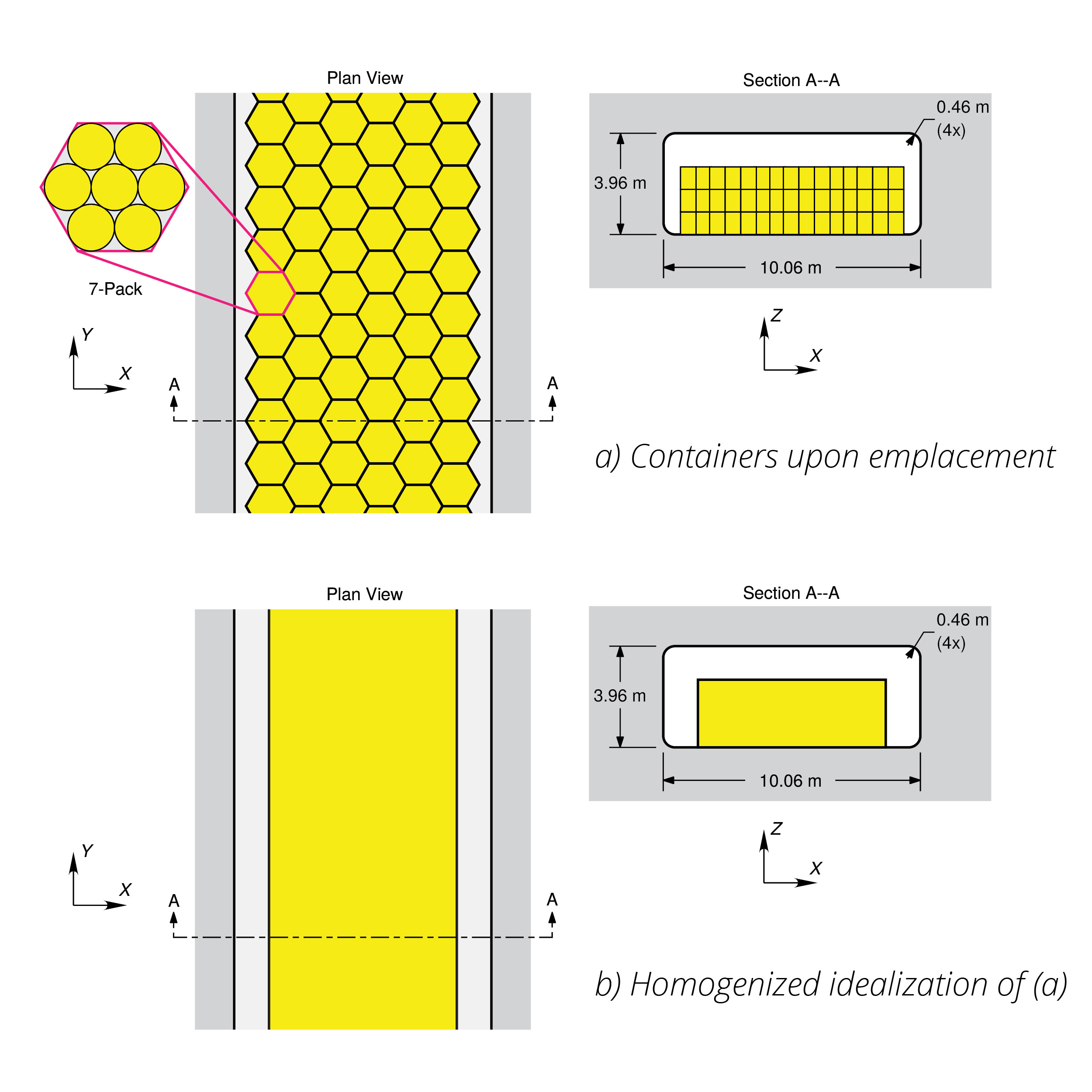
This modeling approach may be sufficient for standard waste containers, but WIPP disposes of other container types that may compact quite differently than standard waste containers, such as Pipe Overpack Containers (POCs). As shown in Figure 1b, a POC consists of a thin-walled stainless steel pipe filled with waste, surrounded by fiberboard and plywood, within a 55-gallon drum. These containers are structurally anisotropic, susceptible to buckling, and likely to interact with one another during compaction, which prompted Sandia researchers to discretely model the individual POCs, including the pipe and plywood within each drum. Discrete container modeling comes with a significant increase in computational cost, but processing power has also advanced significantly since studies performed in the 1990s. Even if a homogenized POC model is developed in the future, the higher fidelity model will still be useful as a reference for the homogenization error.
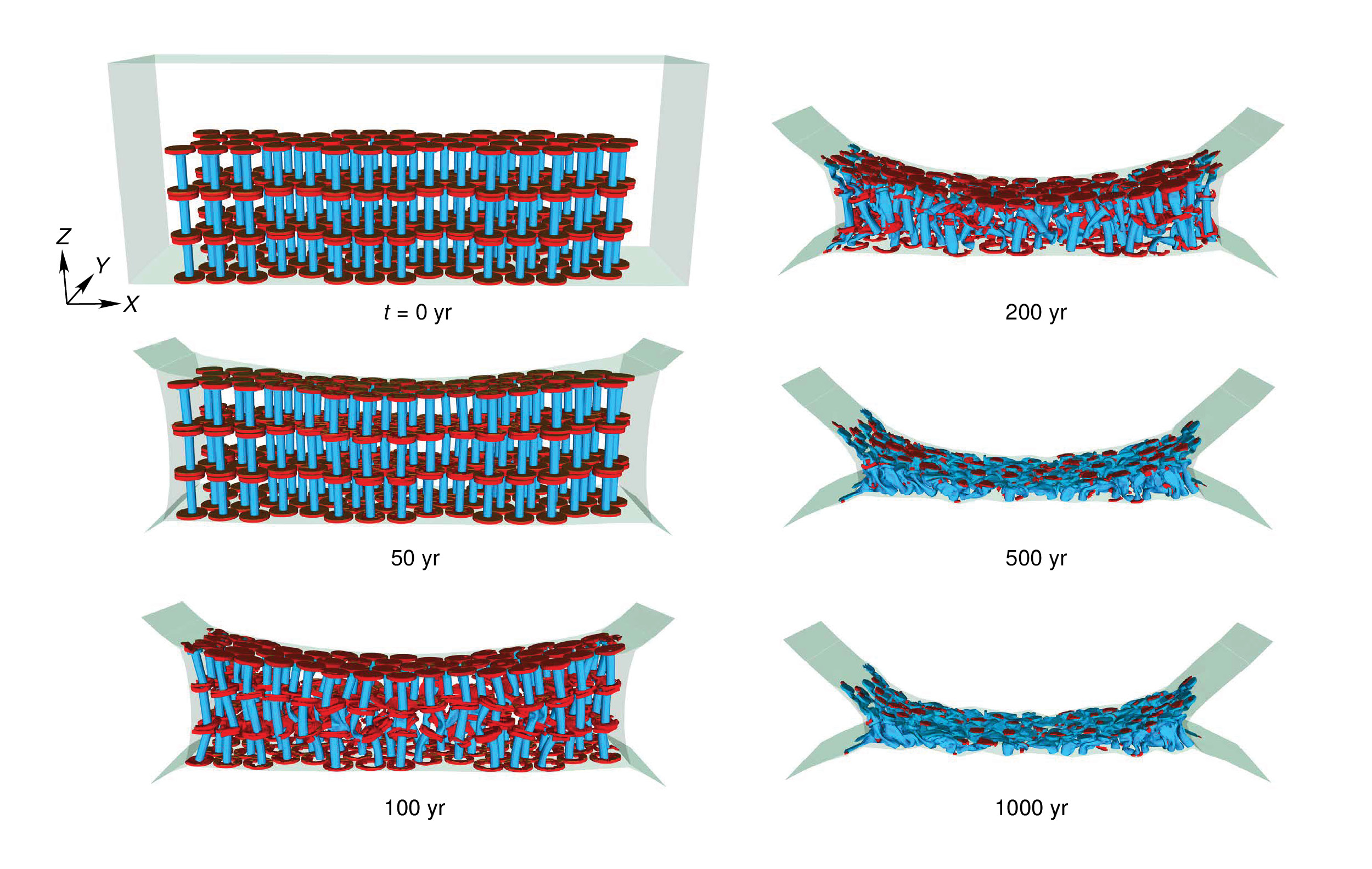
Images of 6-inch standard container gradual compaction predictions from Sandia’s Sierra/Solid Mechanics are shown in Figure 3 at selected time instances. The plywood, lateral fiberboard, and 55-gallon drums were included in the simulation, but they are hidden in Figure 3 to reveal the flanged pipes. The geology is also hidden, leaving only the semi-transparent surface of the room, and the perspective view is tilted in order to show the 3D nature of the compaction. While actual disposal rooms are 91 m long in the Y-direction, a representative Y length of 2.15 m was considered sufficient for modeling purposes.
The compaction sequence is as follows: The roof first contacts the containers at room mid-width at t = 41 yr and contacts the entire upper layer of containers by t = 70 yr. By t = 100 yr, many 6-inch flanged pipes have buckled under the axial load supplied by the roof and floor. By t = 200 yr, numerous pipes originally stacked in the upper and middle container layers have been pushed down into the bottom layer. Further room closure buckles the remaining flanged pipes and pushes the upper/middle container layers down into the bottom container layer. Nearly all of the fiberboard finite elements disappear as they were deleted upon inversion. At t = 1000 yr, the compacted shape of the container array is essentially stabilized to something resembling a tall and slender “I” turned on its side.
The containers clearly deform in a non-uniform and highly complex manner as they slide past one another in Figure 3. Interactions between containers are realistically captured by modeling each container discretely rather than homogenizing them into a single material. These high-fidelity simulations will help Sandia assess the nuclear waste isolation process and evaluate whether the risks of an adverse event are acceptably low.