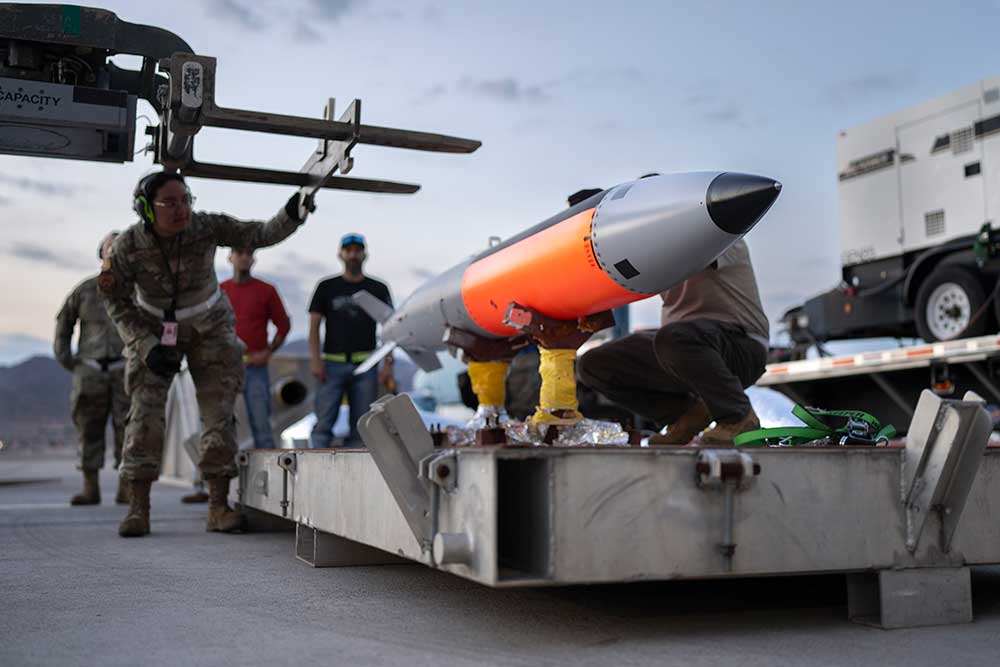
B61-12 program reaches 50% production milestone
Through significant collaboration with nuclear security enterprise partners, the B61-12 program met its 50% production milestone. The the team resolved numerous complex challenges, each of which brought a better understanding of design and production. This milestone was achieved through strong collaboration between the design and production agencies, who maintained steady-state production to deliver on this critical program. • 1000, 2000, 3000, 5000, 7000, 8000, 10000
Innovative spray technology improves efficiency and safety
Innovative spray technology equipment for production was designed, procured and installed to reestablish a production capability that improves efficiency and safety through use of an interlocking mechanism and a sealed inert chamber. The project encompassed rigorous site acceptance testing, major facility modifications and complex equipment installation, startup and characterization — all completed on a highly accelerated schedule. • 1000, 4000, 7000, 9000
Using AI to assist derivative classifiers
Developers from Sandia, Lawrence Livermore and Oak Ridge national laboratories and the Y-12 National Security Complex demonstrated how artificial intelligence can help identify classified information in documents from three datasets using two classification guides. The team plans to develop coverage for more classification guides, with the goal of enabling derivative classifiers across the DOE complex to use AI to identify potentially classified information in electronic documents. • 2000, 4000, 5000, 9000, 10000, LLNL, ORNL, Y-12
New design tools improve production
Sandia implemented Design for Manufacture and Assembly tools for electrical and mechanical design staff by teaming extensively with Kansas City National Security Campus to implement rules based on its manufacturing guides. Electrical and mechanical design teams will introduce manufacturing knowledge earlier into the design process to improve production and reduce feedback loops and late changes. • 2000, KCNSC
SWSIE aids impact analysis
The principle-based Strategic Work Scope Inquiry and Evaluation process significantly aided the Labs’ strategic direction by assuring existing commitments aren’t put at risk and that new work requiring resources beyond one’s direct control is not accepted without input from those affected. New work scope requests that meet thresholds are evaluated, judged and logged to show evidence of consideration and regarded as establishing precedent to ensure work aligns with strategy and enables future needs. • 2000, 7000
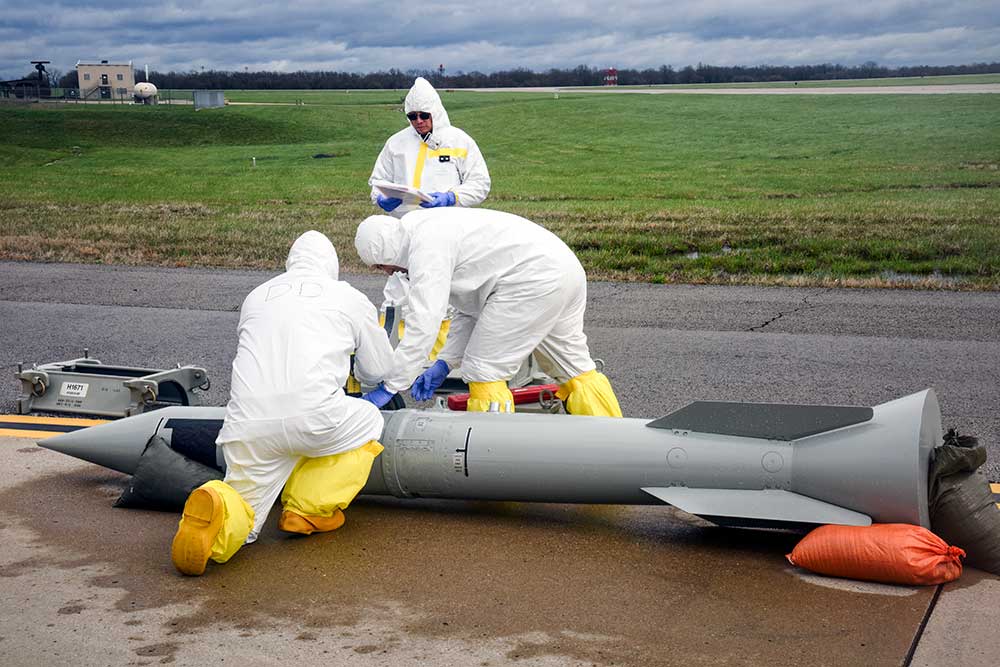
First national-level accident response exercise in four years
Sandia successfully completed the first national-level Nuclear Weapon Accident Incident Exercise in four years, after events were canceled due to COVID-19 restrictions. The Accident Response Group of responders from across Sandia New Mexico and California partnered with NNSA, DOD, and other nuclear security enterprise and federal agencies to exercise this critical capability. • 6000, 7000
First X-Flyer test conducted in over a decade
The Light Initiated High Explosive team conducted the first full-scale, explosively accelerated flyer plate test, called X-Flyer, in over a decade, then conducted a second full-scale test to demonstrate repeatability. Both tests were performed on the Joint Technology Demonstrator GT3B body, demonstrating a high-fidelity cold X-ray-induced mechanical response, an aboveground simulator capability that is unique to the nuclear weapons enterprise. • 7000
Review process saves time and money
The Stockpile Systems and Multi-Weapon Systems projects successfully reduced the frequency of Management Review 1 for approximately 17 projects that are stable and performing well. This has reduced hours spent in meetings for line participants, leadership, Sandia Field Office partners, technical leads, analysts and liaisons, saving about 600 hours annually. A streamlined approach to more concise and intentional presentations also meant more time could be focused on program integration. • 300
Model-based quality management system deployed
Sandia modernized its Weapon Quality Management System by creating and deploying a model-based tool that allows easy visualization of key quality procedures, making the system easier to learn and use. This new tool also will enable future systems engineering for other elements of the system to improve process efficiencies and reduce time and energy required to develop new products. • 2000, 9000
Electronic Parts Program completes high-impact projects
In its first year of executing projects, the Electronic Parts Program had several noteworthy achievements for stockpile and modernization programs. The W87-1 continues to follow Electronic Parts Program requirements. All systems have benefited from strategic sourcing efforts by the program to mitigate geopolitical supply chain threats. • 7000
Digital engineering improves thermal
battery production
The Power Sources Technology Group applied Set-based Concurrent Engineering, an agile digital engineering method, to improve thermal battery production. Modeling of thermal battery activation enabled a comprehensive analysis that led to understanding the impacts of material processing on overall performance to customer requirements and avoided
$1 million in costs. These tools can identify areas for research and development investments or for developing new proposals.
• 1000, 5000, 7000
W88 Alt 370 production halfway home
Half of the W88 Alt 370 program of record, which sustains and refreshes the deterrence mission of the W88/Mk5 system, was completed. In concert with this achievement, more than half of W88-0 systems have been modernized with the turnaround of the Alt 370 production. This success is underpinned by the production support of the design agency and strong partnership with production agencies such as the Kansas City National Security Campus, Pantex Plant, the Y-12 National Security Complex and the Savannah River Site. • 7000, KCNSC, Pantex, Y-12, SRS
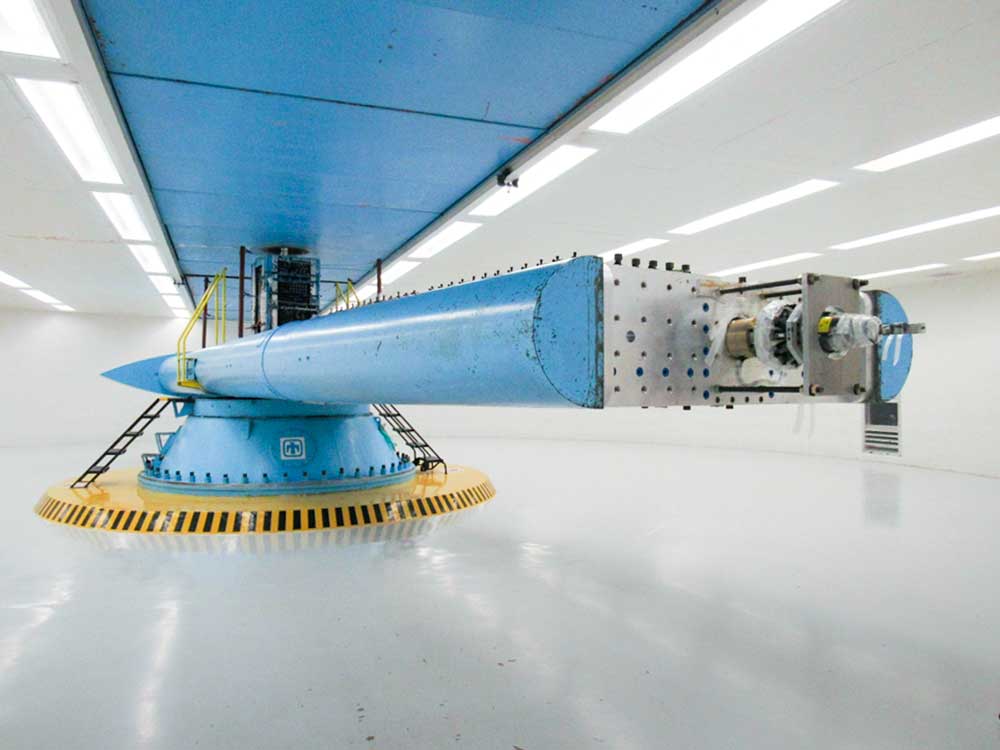
Mk21 Fuze program nears qualification and production milestones
All major components of the Mk21 Fuze have reached first-production unit status and are in production. The fuze successfully completed final qualification testing and analysis activities, including electrical, mechanical, radiation, materials, ground and flight tests and associated performance analyses. Final qualification results support the 2024 Qualification Engineering Release and first production unit for the fuze program. • 1000, 2000, 5000, 7000, 8000, 10000
Telescopic excellence
Since its launch, the Wide Area Space Situational Awareness Telescope onboard processing system has demonstrated excellent performance with confirmed detections of neighboring space objects. For the telescope, Sandia trained and deployed a convolutional neural network to replace a large traditional image processing chain, greatly simplifying onboard implementation and enabling rapid improvements to mission data processing on orbit. • 1000, 5000, 6000, 7000
First development W80-4 flight test
The W80-4 team completed its first flight test with a fully functional, instrumented W80-4 test unit aboard a development version of the Air Force Long-Range Stand Off cruise missile. The missile flew a representative flight profile and the W80-4 test unit successfully demonstrated compatibility with the missile throughout flight, including simulated warhead yield over target. • 2000, 8000, KCNSC, LLNL
W80-4 program replan approved
The W80-4 program completed and received NNSA approval for its cost and schedule replan. The major effort by the W80-4 Systems Program Management team began at the start of 2023 to align the program with delivery of the first production unit in 2027. The replan is designed to help the program assess risks, identify priorities and streamline processes. • 8000
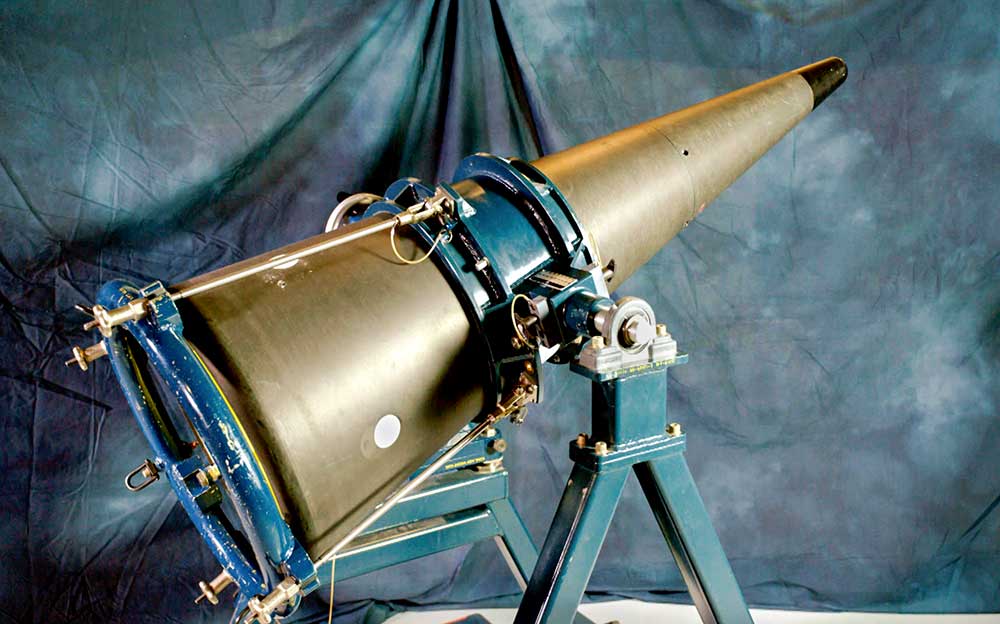
Evaluation efforts keep stockpile safe
Sandia’s Stockpile Evaluation Program completed a high workload of testing, tester development, data analysis and new program onboarding. On the modernization programs, the Weapon Evaluation Test Lab completed 17 system lab tests on the B61-12 and 16 on the W88 Alt 370. For core surveillance, 22 system flight tests and more than 50 system lab and 100 component tests were completed. • 2000, 7000, 8000
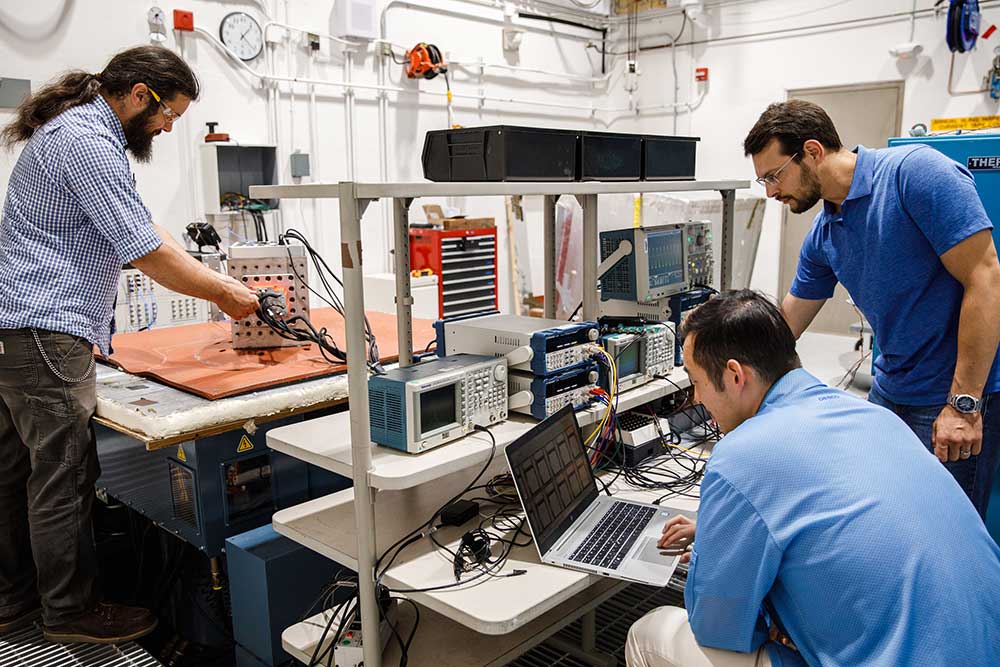
W80-4 JTA baseline design review completed
The W80-4 joint test assembly team completed its baseline design review, during which an independent panel of experts from Sandia and Lawrence Livermore National Laboratory evaluated the completeness and stability of the baseline design and assessed its readiness to proceed to a final design. The assembly team partnered with other Sandia organizations and across the nuclear security enterprise to test the design, building five ground and flight test units and culminating in flight tests with the Air Force Long-Range Stand Off cruise missile. • 2000, 8000, LLNL
B61-12 aerodome modeling, simulation accelerates issue resolution
The B61-12 program quickly developed technical basis for the structural strength of the B61-12 aerodome by using modeling and simulation to answer high-priority unsatisfactory reports. This activity investigated the effects that typical manufacturing imperfections have on the strength of the overall structure and resulted in increased technical basis for understanding the design. • 1000, 2000, 7000
Peer review improves W80-4 warhead case team processes
The W80-4 Warhead Case Product Realization Team asked the Neutron Generator Production Team to conduct a peer review of operations in the Sandia California Lightweight Structures Lab. While Sandia is not the production agency, the product realization team is responsible for producing about half of the development hardware crucial for qualification testing of the W80-4 warhead. The neutron generator team evaluated all aspects of the development build process. • 8000
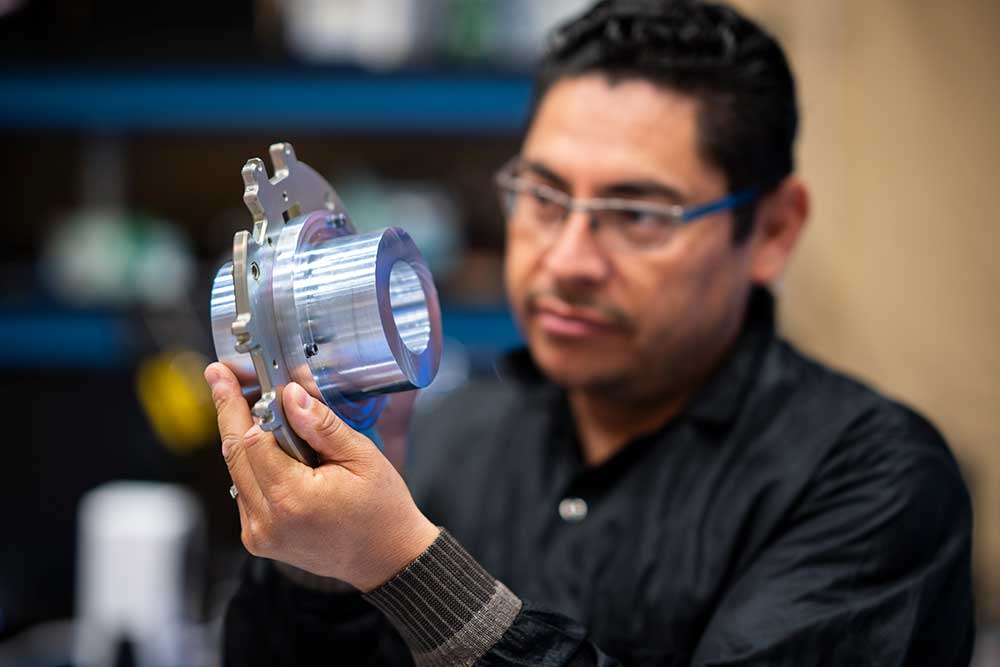
Flight demonstrator supports critical test
The Enzo demonstrator team developed and delivered an experimental reentry vehicle within a tight two-year deadline for a critical flight test to perform relevant technology demonstrations and experiments. The accelerated schedule required partnerships with Los Alamos National Laboratory, NNSA and others. More than 100 Sandians contributed to the success of project that produced streamlined design, integration and test methodologies and lessons learned for how to develop, test and deliver faster across the nuclear security enterprise. • 1000, 2000, 5000, LANL
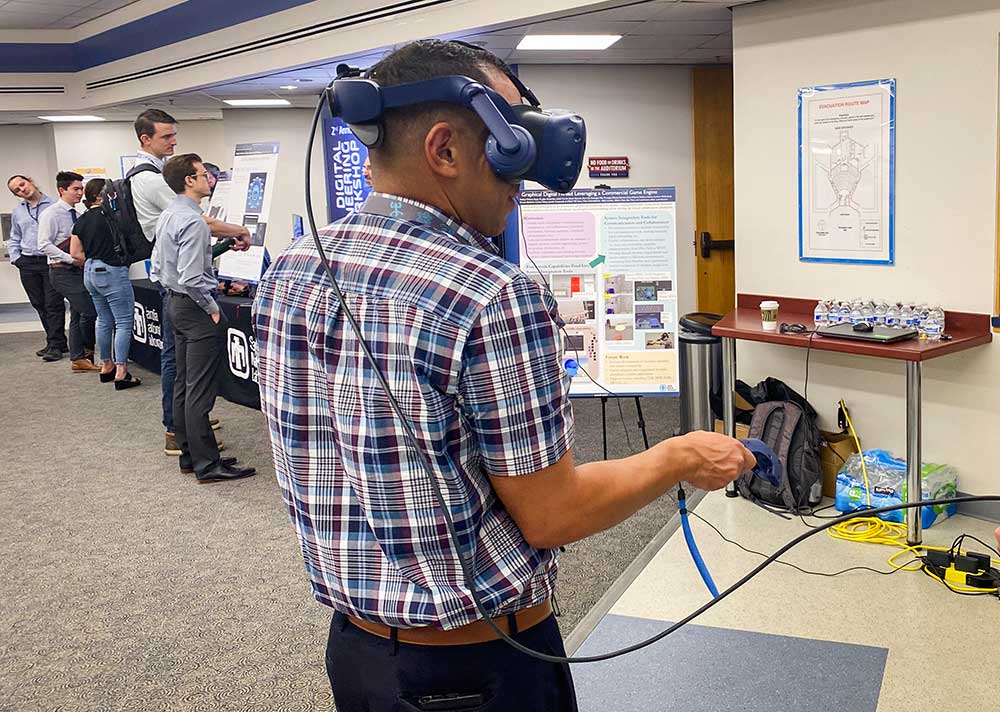
Digital engineering, virtual reality rooms aid collaboration
Sandia established three digital-engineering war rooms at the New Mexico and California sites. The rooms, with access to multiple classified and unclassified computer systems, allow interdisciplinary teams to use digital-engineering tools to collaborate and codevelop. The team also established more than a dozen virtual reality-capable rooms in New Mexico, California and Texas to help teams in different physical locations work together more effectively. The systems apply digital engineering tools for improved communication, knowledge preservation and accelerated product realization. • 2000, 5000, 7000, 8000, 9000
W87-1 program enters development engineering phase
The Nuclear Weapons Council approved the W87-1 program to enter Phase 6.3, development engineering, and the conceptual design review of the system was completed. The review was followed by 23 component reviews and the system conceptual design gate. Program requirements continued to mature, and the team successfully completed multiple system characterization activities. Close partnerships with Lawrence Livermore National Laboratory and the Pantex Plant, including an early conceptual Hazardous Analysis Task Team effort, will support future successes. • 3, 500, 2000, 3000, 5000, 7000, 8000, 10000, LNLL, Pantex
Superior capacitor technology selected
The W87-1 Firing Set Assembly and Capacitors Product Realization teams successfully identified a new main capacitor technology. These capacitors have not been used previously for nuclear deterrence but offer capacitance equivalent to traditional mica or Mylar technologies at one third of the volume with superior performance in strategic radiation environments, with a third less charge loss from ionizing radiation. Viability of this capacitor technology was demonstrated during successful radiation testing at the Annular Core Research Reactor. • 7000
Improved process for additive manufacturing
The Electro3D additive manufacturing process, which simultaneously analyzes and manufactures materials, was launched. Electro3D is more energy efficient than current metal 3D printers. The technology is scalable, deployable, can print multimaterials with rapid transition and seamlessly integrate with machine learning techniques to address the needs of many customers. The project is rooted in the recent Advanced Manufacturing Techniques of Thermoelectric Modules project sponsored by Laboratory Directed Research and Development and won an R&D 100 Award last year in the Process/Prototyping category. • 7000
New onboarding program makes big impact
Sandia’s Product Delivery Value Stream group brought on 45 staff members through a new program designed to enable their success and better integrate them with their new team. This dynamic program helps staff become familiar with nuclear deterrence programs while providing the tools and resources they need to execute their jobs effectively as the next generation of experts in purchased products and limited-life components manufacturing. • 7000
W80-4 team completes development engineering activities
The W80-4 team successfully completed all Phase 6.3, development engineering, activities and received NNSA approval to move into Phase 6.4, production engineering, following completion of its system preproduction engineering gate. Leading up to the production engineering phase, the team successfully completed a preliminary review with the Design Review and Acceptance Group, chaired by the Air Force Global Strike Command chief scientist, with members from the Air Force, Navy and Army. The group determined that the baseline W80-4 design meets the DOD military characteristics and stockpile-to-target-sequence requirements. • 2000, 8000, LLNL
Integrated Surety Architecture achieves first production for vital programs
The Integrated Surety Architecture program achieved first production for the W88 Alt 940 and B61-12 Multiapplication Transportation Attachment Device systems. Diamond-stamped Alt 940 hardware was delivered to the Pantex Plant and installed to complete first production of a new shipping configuration for the W88/Mk5 reentry body assembly. Integrated Surety Architecture provides an additional layer of security during NNSA transportation, and product realization has been a multicenter effort in partnership with Los Alamos National Laboratory, the Kansas City National Security Complex and the Pantex Plant. • 6000, 7000, 8000, LANL, KCNSC, Pantex
Hermetic connector produced using 3D-printed metal shell
Sandia produced a hermetic connector using a 3D-printed metal shell. This achievement supported the Rapid Development Connector project with the goal of maturing Labs technologies and workflows to produce electrical connectors for early development. It also has the potential of drastically reducing — in some cases, up to a year or more — the lead time to design, manufacture and test custom electrical hardware used in a variety of programs. • 1000, 7000
Warhead sectioned and remotely machined for analysis
The Explosives Technology Group explosives machine shop collaborated with the W80-4 program to section a high-explosive warhead for analysis, marking a first-of-its-kind effort for Sandia to remotely machine an assembly that contained high explosives. The application of technologies such as computed tomography, 3D laser scanning and robotics minimized personnel exposure to hazards throughout the process. The successful outcome demonstrated and highlighted the Labs’ broad engineering, teaming and explosive operations capabilities. • 7000, 8000
Network launches to support ND manufacturing production and development
The Unclassified Operational Technology Network — a mission-enabling innovation that establishes a secured network branching from Sandia’s enterprise network — was launched to support nuclear deterrence manufacturing production and development. The network accommodates unclassified production equipment and software that cannot connect to the enterprise network. As this network simplifies security accreditation for this class of equipment, it also lays the groundwork to enable smart manufacturing at the Labs. • 7000
Enhanced surety program meets urgent need
Sandia provided design and system integrator oversight to deliver an enhanced surety program for an urgent U.S. Air Force security need in an accelerated schedule of 30 months. The effort required close coordination with Department of Defense partners and teams across Sandia and Los Alamos National Laboratory. Sandia managed high-risk supply chain challenges and applied rapid prototyping to production cycles while meeting or exceeding weapon product requirements and the highest NNSA quality rigor. Global Security teams provided nuclear deterrence with substantial technical expertise during the installation. • 2000, 6000, 7000, LANL