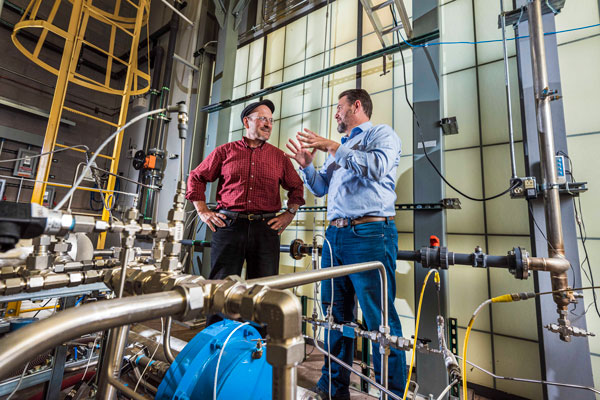
Electricity production is one of the industries that uses the most water in the country each day. Researchers at Sandia are helping the largest power plant in the United States identify the most efficient and cost-effective strategies to reduce water use. They have developed a first-of-its-kind comprehensive system dynamics analysis that can show power plants which wet cooling systems can save them money.
The analysis could eventually be used at other plants as federal regulators begin to reduce the power industry’s allowed water supply. The researchers have also redesigned and patented an air-cooling system to make waterless cooling more energy efficient and possible over a wider range of operating conditions.
The Palo Verde Nuclear Generating Station near Phoenix, Arizona, converts heat from nuclear reactions into electricity. The heat boils water, creating steam that drives turbine generators. Steam leaving a turbine must be cooled and condensed before it is reused.
More than 40% of the country’s water is used for wet cooling at power plants. Typically, large thermoelectric power plants are located near lakes or rivers so that operators can draw a regulated amount of water, run it through a condenser to cool steam leaving the turbines, and discharge roughly the same amount they withdrew.
The Palo Verde plant has limited access to water because it is in the middle of a desert. Its cooling water is treated wastewater, which is becoming increasingly expensive as other customers — who are willing to pay higher prices for water — emerge. To curb rising costs, operators want to reduce the plant’s water use by about 9 million gallons a day. Annually, that savings is roughly equivalent to a 16-square-mile pool of water one foot deep, said Sandia nuclear engineer Bobby Middleton.
Other thermoelectric power plants will be looking for water-saving approaches in the future as rising populations, increased per capita energy usage and potential federal regulations reduce supplies of cooling water. The Sandia analysis could be used to save water at these power plants, too, whether they run on coal, natural gas or nuclear energy.
“We jumped at the opportunity to tackle this problem for Palo Verde because solutions that work for Palo Verde could also work for other plants, too,” Bobby said.
Emerging cooling technologies
To reduce the plant’s water use, operators at Palo Verde first looked at commercially available solutions. When they realized that nothing available could meet their needs, they turned to Sandia to help identify which cooling systems under development might eventually offer the greatest water savings.
To evaluate different emerging technologies, Bobby developed software that combines the physics of the cooling process — such as fluid flow, heat transfer, atmospheric evaporation and water treatment — with the financial impact of different solutions. Sometimes, a certain technology saves a plant money through increased efficiency; other times, reductions in water use deliver overall cost savings.
“No one has created a system dynamics analysis that simultaneously considers all these factors before,” Bobby said. “It helps us predict the benefits we might see from a particular technology so that we spend time only testing the most promising approaches.”
The wastewater that arrives at Palo Verde contains silica, calcium, magnesium and phosphate ions. These salts concentrate as the cooling water evaporates in the cooling system, possibly forming new minerals that might clog the cooling towers. Currently, operators add lime, soda ash and acid to the wastewater before it enters the cooling tower to reduce the possibility of mineral formation.
Bobby and Sandia chemist Patrick Brady are using the model to identify less expensive ways to remove ions at different points in the cooling cycle. For example, the Sandia researchers are examining the feasibility of desalinating discharged cooling water so that it can be reused. Otherwise, the water is too salty for reuse and must be evaporated from large ponds.
The researchers have finished the first phase of the project, developing the analysis software. The next phase involves using the software to identify the most promising water saving technologies, including alternative water treatment approaches, as well as dry and hybrid coolers that use supercritical carbon dioxide instead of the standard refrigerants used in commercial technology. The final phase of the project involves testing the most promising technology in a laboratory setting in the hope that a cost-effective solution can be installed at Palo Verde in 2026.
Efficient cooling without water
While evaluating effective cooling technologies, Sandia researchers also are working to improve existing solutions. Earlier this year, Bobby and his colleagues were awarded a patent for redesigning an air cooler to use supercritical carbon dioxide to transfer heat from steam to air. This change makes indirect dry cooling feasible over a wider range of conditions while increasing the system’s efficiency.
Wet cooling systems such as those at Palo Verde have water-filled condensers to cool steam leaving the turbines. Direct dry cooling systems transfer heat from the steam directly to air; indirect dry cooling systems transfer heat from the steam to water then from the water to air. Current commercially available systems designed to retrofit a power plant typically use a recirculating refrigerant instead of water to help transfer heat to air.
In these commercially available systems, the liquid refrigerant boils as it absorbs heat from the steam and condenses into a liquid as it loses that heat to air. This change from liquid to gas releases energy that causes the refrigerant to circulate naturally through a heat exchanger.
The new indirect cooler design uses supercritical carbon dioxide instead of a refrigerant. Here’s how it works: Above a certain pressure and temperature, carbon dioxide becomes a supercritical fluid. This means the CO2 acts as a liquid below the critical temperature and as a gas above the critical temperature. However, at no point is the fluid a two-phase fluid; it does not boil. Because one fluid can change from a liquid to a gas without boiling, a supercritical fluid can transfer heat over a wider temperature range than a sub-critical fluid (such as the R134a used in current technologies).
The performance benefits with this design come from the amount of air needed to refresh the supercritical carbon dioxide for another round of cooling. A heat exchanger with supercritical carbon dioxide uses less air to cool water to the same temperature as a traditional dry cooler with a sub-critical refrigerant; it can also make water cooler using the same amount of air. Both impacts improve the overall energy efficiency for the cooling process.
“The expanded operating conditions also mean that there are more times of the year plants can use dry cooling,” Bobby said.
The researchers plan to test Sandia’s design against state-of-the-art, commercially available technology, and they are currently analyzing it as a potential solution for the Palo Verde plant.
Due to the decreasing availability of water, what was once the cheapest resource for thermoelectric power plants is quickly becoming one of the most expensive aspects of electricity production.
“Water saving technologies for energy production are critical for scientists and engineers to consider today,” Patrick said.