Compendium of geothermal bit behavior to help drive down drilling time
DRILL DEMO — A Sandia team test drill bits at Sandia’s Hard Rock Drilling Facility. (Video by Ruth Frank)
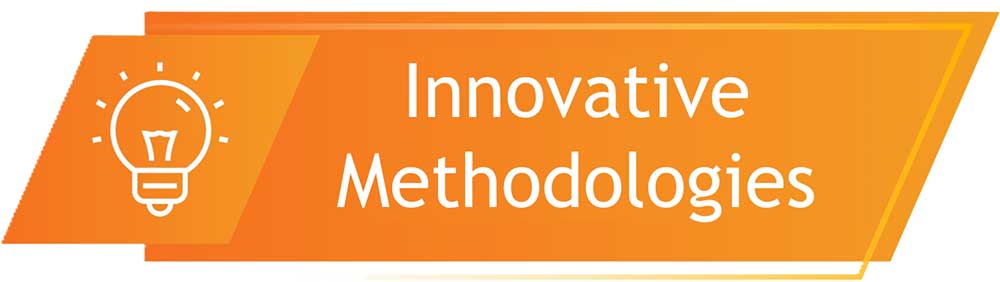
In golf, a great caddie helps tune a professional golfer’s performance, matching their skill, choice of club and type of swing to the course and weather conditions.
A recent analysis of drilling records from the Frontier Observatory for Research in Geothermal Energy by Sandia researchers aims to provide this level of guidance to the art of selecting the right drill bit for geothermal well drilling, based on location and depth, to reduce drilling costs. FORGE is a DOE-funded field laboratory in southwestern Utah, dedicated to testing geothermal technologies to reduce risks and accelerate commercial viability.
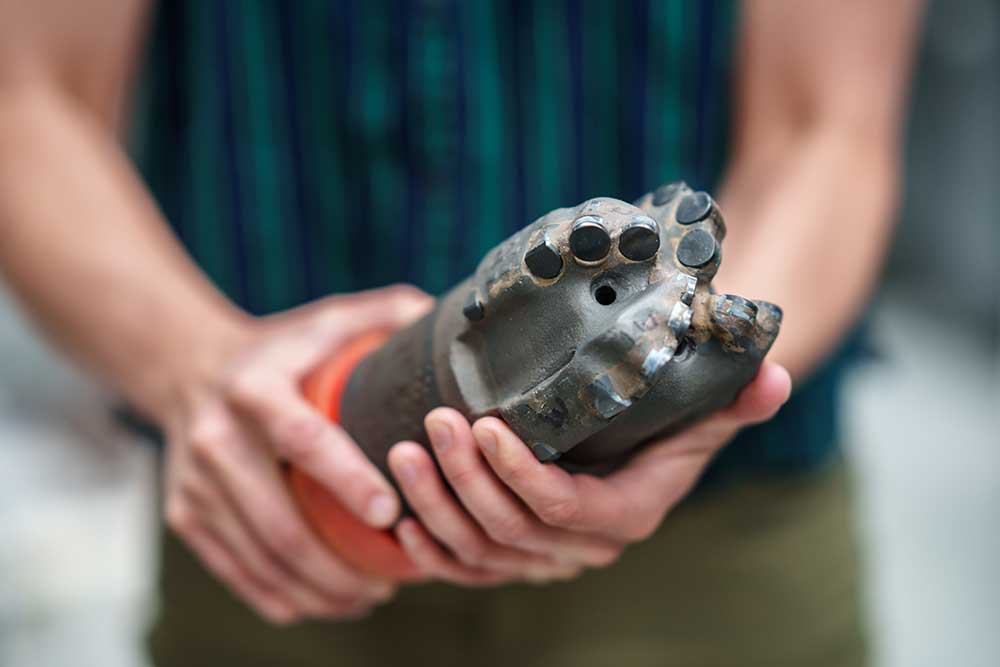
Geothermal power plants offer the advantage of providing clean electricity all day, every day, regardless of weather conditions, thus balancing intermittent renewable energy sources such as solar panels and wind farms. However, the high startup costs for finding suitable locations and drilling the necessary wells have hindered commercial development. The FORGE project, alongside the Sandia analysis, aims to improve drill bit performance in the challenging conditions of geothermal sites and reduce drilling costs.
“At the FORGE site, a number of wells were drilled to depths of approximately 10,000 feet, and they were largely drilled by polycrystalline diamond compact bits,” said David Raymond, a Sandia mechanical engineer and leader of the analysis. “This is one of the largest applications of diamond bits for geothermal drilling in their 40-year history. We produced a compendium of all the drill bits used and how they performed.”
The Sandia research team, led by David, analyzed drill rig data from the most recent wells drilled at the FORGE site, looking at the response data and post-operation photos of each polycrystalline diamond compact bit. The results of this analysis were recently shared with the geothermal community. Polycrystalline diamond compact bits have proven to be more cost effective than roller bits for oil and gas drilling, this compendium could help do the same for geothermal drilling.
Analysis for better bits
At the University of Utah-managed FORGE site, four wells were drilled for injection, production and monitoring, primarily using polycrystalline diamond compact bits. These bits use the strength of lab-made diamonds in the form of disc-shaped cutters. Many of these cutters are embedded into the bit in a specific arrangement designed to best cut the rock. The industrial diamonds in these bits are tiny, grown in a lab for strength rather than aesthetics.
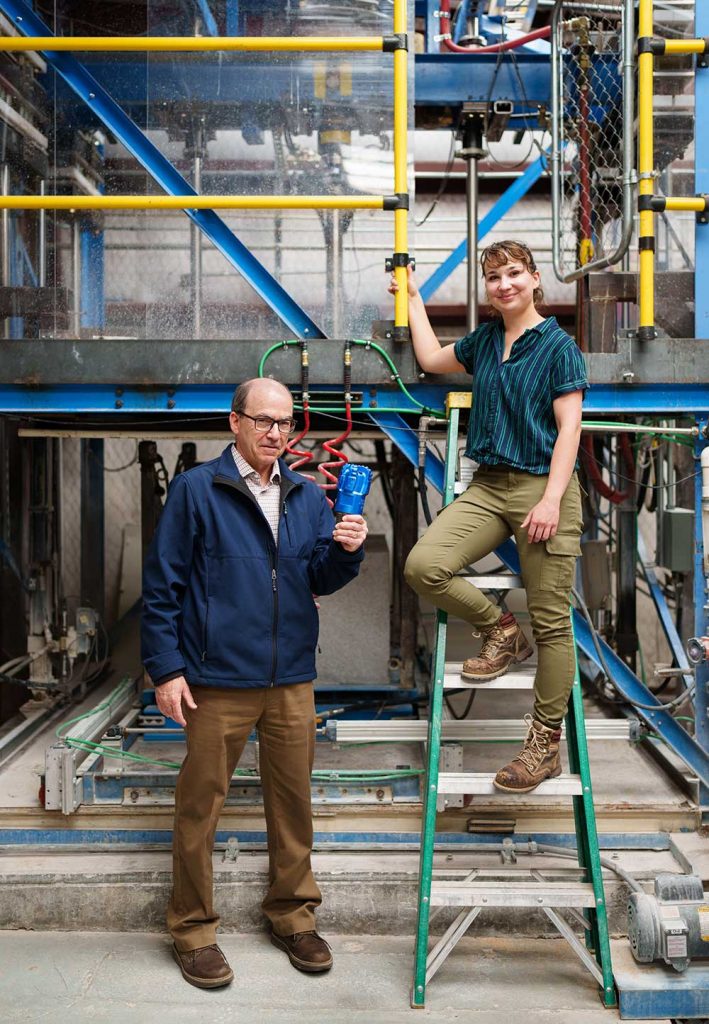
“Two things afforded FORGE the ability to drill with these advanced diamond bits,” said Doug Blankenship, a Sandia geothermal expert on detail with DOE’s Geothermal Technologies Office as a senior adviser. “One is the advanced technology that the bit companies have developed so that the bits are more capable of drilling in hot, hard rock. Two is the approach to running these bits that Fred Dupriest and Sam Noynaert from Texas A&M brought to the drilling program.”
David and his team, which includes mechanical engineer Melanie Schneider, looked at the daily reports from the FORGE site. They collected four key parameters — the force applied to the drill bit by the rig, the rotation speed set by operators, the drilling speed, and the power needed to achieve that speed — and inserted those numbers into a computer model. They used the algorithm to model the interaction between the drill bit and the rock, comparing that with the response of a single standardized diamond cutter.
The Sandia team also looked at the cost constraints, the balance between drilling speed and distance drilled and how that plays into the cost per foot drilled by each bit. One of the leading costs in geothermal well drilling is the daily expense of renting a drill rig, David said. But that doesn’t mean drilling faster is always the most cost-effective solution, Melanie said. Depending on the depth already drilled and the time taken to get a fresh bit to the bottom of the well, a slower, steadier approach may be more cost effective, David added.
“A big cost is truly how long it takes to get in and out of the hole when you’re at depth,” Melanie said. “A key takeaway from our reporting is it’s not necessarily about going fast or with more force; it’s about trying to extend the bit’s life and getting the most out of each one. We’re already seeing a huge improvement in drilling performance throughout the course of the four wells at FORGE.”
History of diamond bits
In the early 1980s, on the heels of two oil crises and the advent of synthetic diamond manufacturing, the DOE sponsored research at Sandia to develop diamond-based bits for drilling in the hot, hard rock of geothermal systems, David said.
Polycrystalline diamond compact bits are made of many diamond cutters embedded into the bit in a proprietary configuration. Each cutter is a disc of lab-made diamond, sometimes less than 1/16-inch thick, bonded to a tungsten-carbide stud.
More than 40 years ago, Sandia researchers, led by David Glowka, tested diamond cutters from various manufacturers in the lab, measuring the forces required to scratch rock depending on the cutting angle and other parameters, Doug said. Data from these experiments were fed into a computer model that allowed for the simulation of forces on any drill bit design, David said. This code was publicly released and provided to drill bit companies to inform the design of cutters on their bits, which was instrumental in catalyzing the industry, Doug said.
Since then, diamond bits have been used by the oil and gas industry due to their durability and faster drilling compared to roller bits, David said. However, early generations of diamond bits wore out too fast in the hard rock and high temperatures of geothermal sites, he added. Another challenge of drilling in geothermal sites is the rock often contains fractures, Doug said, likening hitting these fractures to striking an unexpected pothole on a bicycle: the best-case scenario is a jolt that doesn’t cause damage.
Sandia has continued refining diamond bits for geothermal drilling over the years, including computational modeling of specific vibrations that can occur in hard rocks that can cause the drill bit to bounce and break, David said. Sandia also participated in field tests of diagnostics to improve diamond bit usage in extremely hard rock.
David hopes this compendium of bit performance at the FORGE site will help bit manufacturers in designing even better performing bits and assist geothermal well drillers in selecting the best bits for their conditions. Both should help reduce startup costs for steady, clean electricity-producing geothermal power plants.
“It’s been a long road getting to this point where polycrystalline diamond compact bits are a viable solution for geothermal drilling,” David said. “It’s not intuitively obvious how you should place the cutters across the bit to balance speed and lifetime, but that is what our analysis has accomplished. There’s an incredible wealth of information here on what worked and what didn’t work on these synthetic diamond bits.”
This analysis and the FORGE project were funded by DOE’s Geothermal Technologies Office.