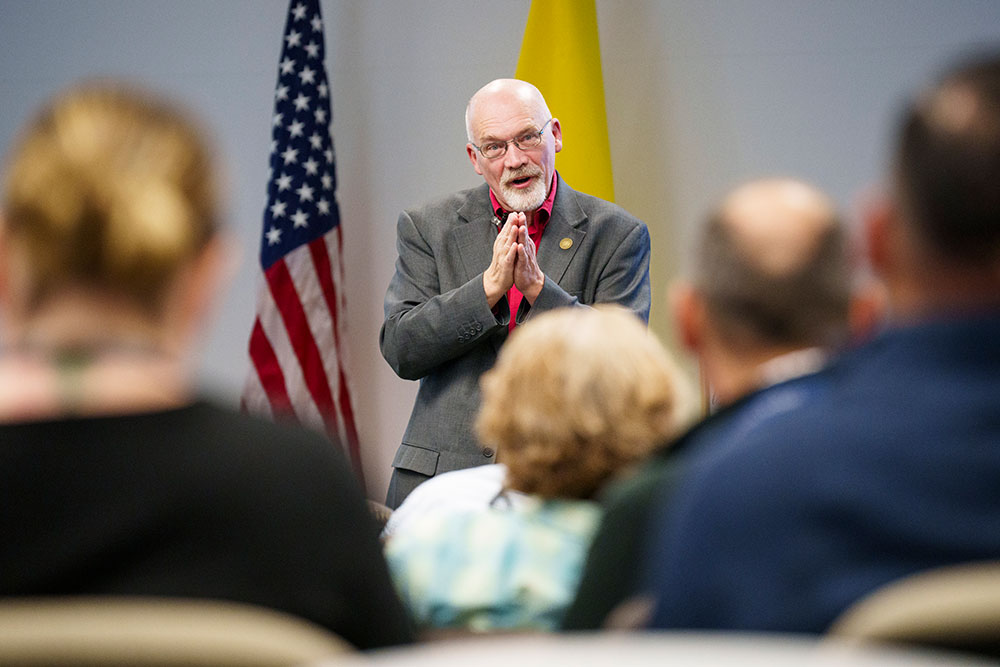
Perfection in continuous improvement and innovation doesn’t mean shaming people when something doesn’t go as planned.
Lorenzo Gutierrez, director of Enterprise Excellence, kicked off Sandia’s recent Lean Summit: Unleash Excellence, held on Nov. 13-15, by inviting in-person and virtual attendees to learn how to more easily and efficiently accomplish Sandia’s shared national mission.
“Unleashing Excellence, the title of this year’s summit, represents a body of work aimed at challenging the status quo at Sandia,” Lorenzo said. “It is challenging our ways of working with increased intention and critical thought as we seek to deliver exceptional service without exception, in all we do. Unleash Excellence serves as a social contract with our employees and our external partners in making Sandia a great place to work and a great partner to work with.”
Unleash Excellence is Sandia’s version of NNSA’s efforts to lead meaningful change in a positive way through its Enhanced Mission Delivery Initiative. Two Lean method experts were invited to speak to staff during the three-day summit at the Computer Science Research Institute at Sandia. The Lean method aims to increase efficiency through continuous improvement, and the presentations focused on how a “Lean” culture can make a difference in innovation success.
According to Ken Snyder, executive director of the Shingo Institute, “A key concept as we begin to look at ways to improve by innovating, is that failure is okay. The failure is not the people. It’s the process.”
Snyder expanded on this idea by saying that when people focus instead on the process as they aim for perfection, they can make progress toward increased excellence. Also, failure is OK because every time someone fails at something, they learn something.
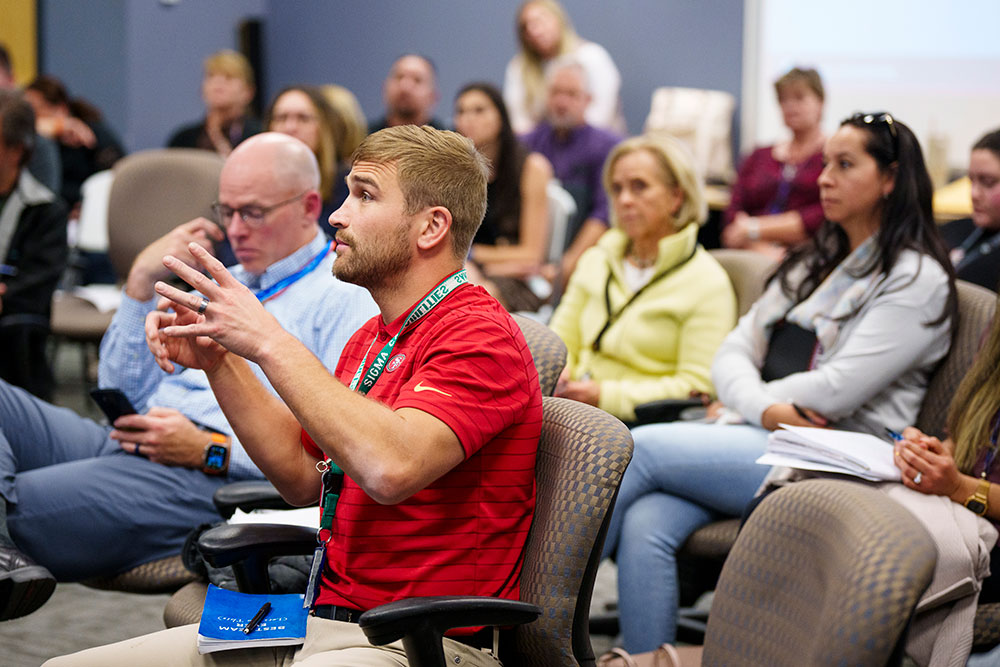
The Shingo Institute’s purpose is based on the timeless principle of shaping cultures that drive organizational and operational excellence.
During his presentation, “Don’t Let Perfect be the Enemy of Better,” Snyder shared necessary elements for a culture of continuous improvement, including that overall culture is the sum of all the behaviors in an organization.
He emphasized that when starting down a path of continuous improvement, an organization should first ensure the purpose for improvements is aligned with the organization’s overall goals.
“Make sure the improvements are going where you want them to go,” he said.
Industry shows the way
Norbert Majerus, retired Lean champion of the Goodyear & Rubber Co., Global Innovation Centers, Lean innovation author and consultant, and Shingo Institute faculty fellow, shared how Goodyear moved to a culture of innovation in 1990.
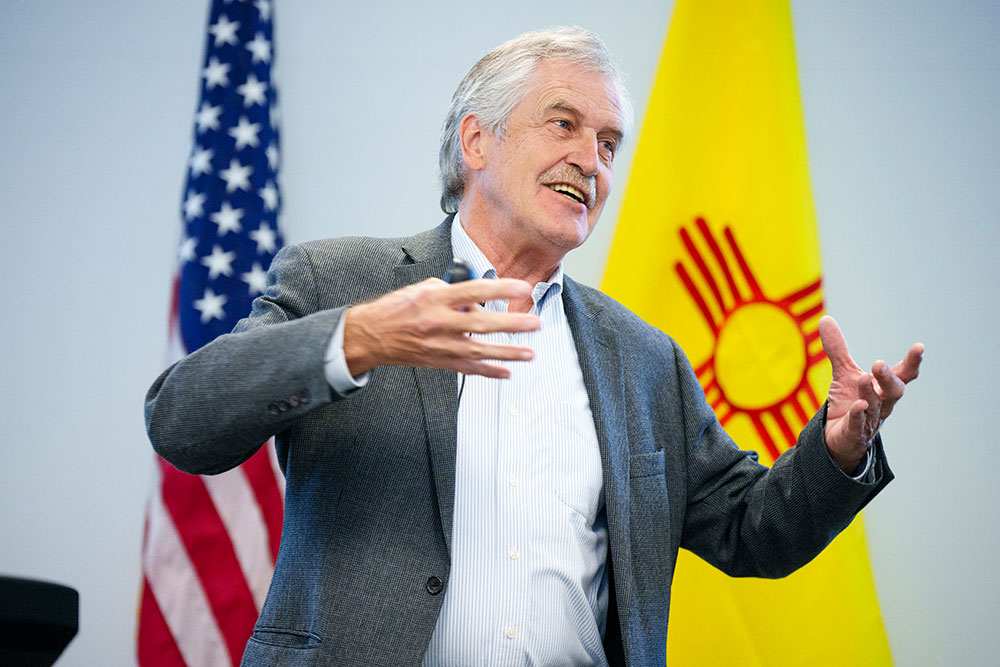
During his presentation, “Creating a Culture of Innovation,“ Majerus shared that many successful approaches to innovation use a Lean culture model.
“Whether a company succeeds or fails at innovation always comes down to their culture. The culture is the process and values that the people use and have,” Majerus said.
Key components of a Lean culture promote respect, engagement and trust, which together, reduce fear of a culture change that promotes team progress over individual or department goals.
“Their move to concentrate on innovation saved the company,” he said. In fact, it helped them launch a tire so different that it had never been seen before. The Aquatred Tire was designed with a center channel designed to dissipate water. This change drove great interest in Goodyear and resulted in increased sales of 21% and a new income increase of 533%.”
Majerus said one obstacle to innovation is an employee’s fear of losing their job status or even continued employment. He suggested overcoming this by aligning organization and individual professional goals, and then the expected behaviors and rewards that support those goals. Other key characteristics of the culture are humble leadership, empowerment and sustainability. Education about innovation and a system that incorporates agility and cycle speed were included as additional culture elements critical to innovation.
Snyder said that an organization must create a system that enables behaviors that support the culture. “When an organization’s leadership makes it easy for workers to do the right thing, such as improve, then the workers will do it,” he said. “Ideal results require ideal behaviors, so align behaviors with performance goals.”
All about the people
Majerus said that for Lean to work properly, there must be motivation for improvements, meaning there must be buy-in from staff. “Employees must be motivated to be innovative,” he said. “They must find joy in their work. They do this by having autonomy, being able to use their expertise and having a purpose.”
“People love to be in charge, use their expertise and if allowed, will come up with ways to make things better. Let them innovate,” Majerus said.
Of course, people work on teams with colleagues who often have disparate goals. Concentrating on organization goals over department goals is key, Majerus said, and focusing on mutual respect can make this easier.
Collaboration that values company over ego is essential for successful innovation and helps departments win at the intersection of their specific interests. Ideally, project managers create a project environment that supports this and ensures that team success is recognized.
In talking about a holistic approach to continuous improvement, Snyder said that a Shingo Institute principle considers continuous improvement as the responsibility of everybody, everywhere in the organization and all the time.
“It’s not something you get released from doing, and it’s not the responsibility of a lead department,” he said.