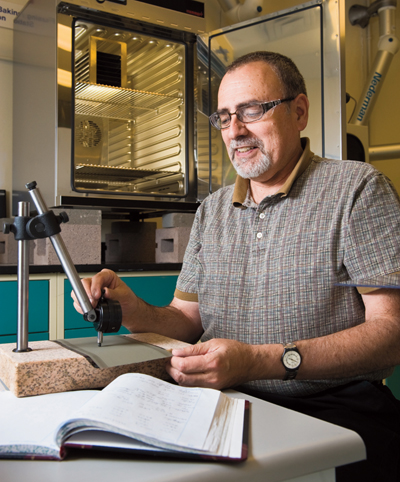
A new thin-film coating process for manufacturing thermal batteries used in nuclear weapons and other munitions that was invented at Sandia will be industrialized under a new corporate partnership with a Maryland company. The process could lead to lighter batteries in a variety of shapes for future applications.
A thermal battery is a nonrechargeable, single-use energy source that can remain inert for years at room temperature before becoming activated at temperatures as high as 1,100 degrees (600 degrees Celsius). The thin-film coating process changes the way some thermal batteries have been made since the 1950s.
Sandia researchers also are looking into whether a patented binder used in the new thin-film coating process has commercial applications, for example in lithium-ion batteries in electric and hybrid vehicles and in batteries used in the petroleum industry when drilling deep underground in hot geothermal environments.
Sandia and ATB Inc., a Cockeysville, Md.-based manufacturer of thermal batteries, recently signed a cooperative research and development agreement (CRADA) to test Sandia’s new thin-film coating process for large-scale industrial production.
“We can take the developments that we’ve had in the lab, scale up the quantities of materials that we use and instead of producing tens of batteries we can produce hundreds of batteries in ATB’s facility,” says Tom Wunsch, manager of Sandia’s Advanced Power Sources Research & Development Group 2546. “It’s beneficial to us to have an industrial partner to work with on these issues and for them to have this new technology.”
Guy Chagnon, CEO of ATB, says his company and Sandia had been working independently on changing the process for producing thermal batteries.
30 thermal battery designs since 1975
“The goal of the CRADA is to industrialize a new process, and to manufacture, build, and test the battery,” Chagnon says. “Sandia and ATB have the same vision with the thin-film coating. We’re putting our resources together to reduce the size and the cost of thermal batteries.”
Sandia’s expertise in thermal batteries stems from their use in nuclear weapons and other munitions. They are designed to be extremely reliable, remaining inert for 30 years at room temperature and then springing into action on a moment’s notice. Sandia has developed about 30 thermal battery designs since 1975.
Sandia researcher Frank Delnick (2546) led the effort to make the thermal battery components as thin-film coatings instead of pellets. Working with him were: Denise Bencoe (1815); Chris Apblett and Eric Branson (both 1815-2); Bill Averill and Linda Johnson (both 2546); Nick Streeter (2547); Martin Bachicha (2548); James Patrick Ball, Robert Knepper, and Alex Tappan (all 2554); and Judy Odinek, who is retired.
Traditional thermal batteries are made by pressing powdered materials into electrochemically active pellets used as the anode, cathode, and separator of the battery. The pellets must be a certain thickness to maintain mechanical integrity and prevent them from falling apart when handled. The amount of material needed to achieve mechanical stability can be up to 10 times greater than what is needed to make the battery work. Therefore, considerable reduction in size can be achieved by making the components thinner, Frank says.
Relatively inexpensive equipment used
Frank’s process uses relatively inexpensive equipment, common in the paint industry, that coats the battery components as thin films onto stainless steel foils. The coatings are held together and bonded to the foil using a patented binder. He says the process will work best for thermal batteries that last from a fraction of a second to a few minutes.
The binder must withstand temperatures of about 660-1,100 degrees (350-600 degrees Celsius), the operating temperature required to melt the salt electrolyte and activate the battery. Once activated, the binder must remain chemically and mechanically stable throughout the discharge of the battery without emitting gas or producing other side reactions that could adversely affect the performance of the battery, he says.
Frank overcame a lot of challenges in processing the binder needed for the thin-coating process.
In the early days, for example, the coatings would peel off after thermal processing or they would emit enough gas to extrude the molten salt electrolyte from the battery cells. Other formulations would cause the binder to deactivate the electrodes and the battery would fail, Frank says.
Coated materials much tougher
Tom says Frank had the technical savvy to overcome these complexities.
“There were many challenges along the way where the work could have stopped at any one of a number of points, but Frank kept going,” Tom says.
The goal of the agreement with ATB is to jointly develop thin-film coatings that will slash the time and materials needed to make thermal batteries.
On average, thermal batteries made with thin-film coatings would use one-fifth to one-half the materials needed for their conventionally manufactured counterparts, Frank says.
The coated materials in the batteries are much tougher than those in current models, Frank says. He expects that thin-film thermal batteries also will perform much better in high-shock environments and will be much more amenable to automated manufacturing.
“Since the parts are more robust, you don’t have to handle them as gingerly,” Frank says.
The new process also could allow manufacturers to produce different shapes of thermal batteries, Frank says. Currently, thermal batteries are cylindrical and range in size from a man’s thumb to a one-pound coffee can.
The first thermal battery made using the new process was slightly thicker than a postage stamp and about the size of a quarter, he says.
ATB employees have visited Sandia to learn more about the process and the company is busy readying its facility to begin developing the new manufacturing process. Chagnon says if the research and development are successful, large-scale manufacturing could begin by late 2012.
The thin-film coating process could be used for select thermal batteries that are being replaced in the B61 thermonuclear weapons as part of a Life Extension Program now under way at Sandia, Tom says. That project, the largest weapons refurbishment effort in the US nuclear weapons complex, currently involves hundreds of Sandia employees and is scheduled to begin production by 2017.