3D-printed torpedo anchor tested for impact data
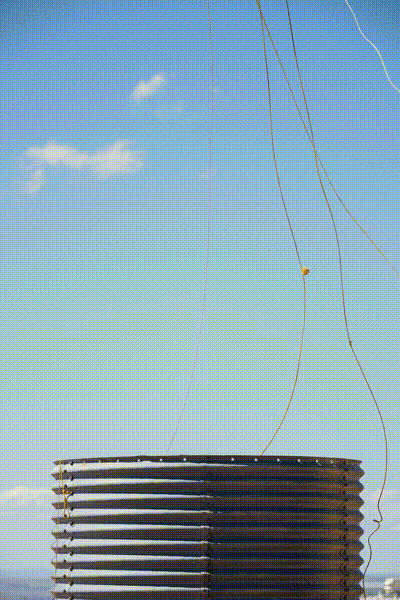
Beside a 50-foot-deep pool, a 300-foot metal tower rises into the air at Sandia New Mexico. Cables and a vertical guided trolley attached to the tower allow personnel to hoist objects to varying heights so they can watch them fall at Sandia’s Drop Tower and Water Impact test facility. Built in late ’50s and early ’60s, the site has been used for impact testing on containers that transport hazardous materials, weapons testing and underwater impact testing. Last month, the facility dropped anchor — torpedo anchors.
Torpedo anchors, heavy arrow-shaped weights, are completely embedded in the seafloor. Traditionally made of steel or other metals, the anchors are fiscally and environmentally expensive. Sperra, a clean-tech company specializing in automated construction for marine energy, is seeking to lower both of those costs by developing anchors that meet performance requirements but also minimize environmental impact. Sponsored by DOE testing program TEAMER, Sperra sought the assistance of Sandia’s Budi Gunawan, a mechanical engineer with water power technologies, to test 3D-printed concrete torpedo anchors. Budi and mechanical environments engineer Rich Jepsen and test operations engineer Luis Abeyta oversaw the testing.

Currently, steel torpedo anchors are used primarily to anchor offshore oil & gas platforms off the coast of Brazil. Sperra is developing a patented scalable concrete torpedo anchor which can be used to anchor marine energy devices like wave energy converters, floating photovoltaics and floating offshore wind. 3D-printed concrete is an ideal material for torpedo anchors due to its weight and durability, and unlike traditional metal anchors, they are more resistant to corrosion. Also, cement anchors have a smaller carbon footprint than metal anchors and are cheaper to produce. Cost is a barrier to wide-scale commercial deployment of offshore energy fields, especially wave-energy converters and floating photovoltaics. As part of the TEAMER network, Sandia personnel assist commercial developers, such as Sperra, with testing wave energy technology. With facilities like the Drop Tower and Water Impact facility already in place, Sandia has the capability to conduct the kind of tests most commercial developers lack the resources to carry out.
Last month’s tests involved a crane hoisting three, approximately 500-pound concrete torpedo anchor prototypes 10-30 feet into the air. A fourth steel anchor was also included in the drop tests for comparison purposes. The test required each anchor to be dropped from different heights into a 12-foot-tall metal culvert with a 10-foot diameter. The pipe was filled with sand and water to mimic the seabed off the coast of Oregon, home to the PacWave test facility for marine energy devices. The sand, which came from a local supplier, was passed through a sieve to verify that its grain distribution matches that at the PacWave. The drop test was designed to evaluate the structural integrity of the prototypes, verify how much force it will take to pull the anchors out of the seabed and provide numerical models for design improvement.
ANCHORS AWAY — A GoPro camera attached to the inside of the metal culver captures the drop and splash from another perspective. (Video by Craig Fritz)
Despite pausing work due to rain and lightning, the test team was able to complete all testing scenarios. Each of the three concrete prototypes are reinforced with steel and have a hollow center where a bullet-shaped metal weight, called a booster, is placed during deployment. The anchors are designed to be dropped from a ship with mooring lines that can be attached to a renewable energy device or floating platform. The booster adds additional mass to the anchors which helps them embed deeper into the seafloor. This makes them less likely to be dislodged by high waves or winds buffeting the surface devices to which they are attached. Once placed, the booster is removed and reused for additional anchor deployments, a cost savings.
The three prototypes had different fin shapes that impacted embedment depth. The anchors didn’t break when dropped, maintaining structural integrity, a concern with using concrete over metal. Preliminary conclusions found anchor capacity, the pull force needed to remove the anchor, was highly dependent on embedment depth, whereas the embedment depth itself is affected by torpedo fin width and angle, seabed composition, and speed and angle of the anchor on impact. Armed with new knowledge about their torpedo anchor designs, Sperra will refine their designs and continue next-stage testing.
The future of renewable energy is anchored in innovation, and with each test, it moves closer to realizing its full potential.