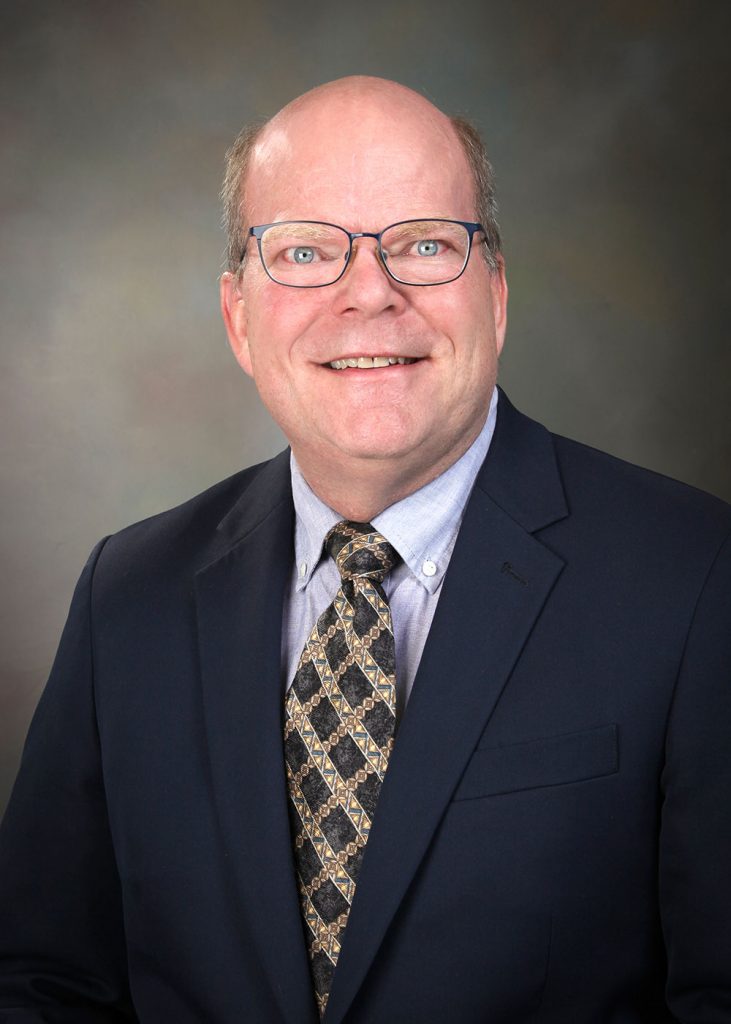
Lonnie Love, the driving force behind the creation of an exploratory manufacturing facility at Oak Ridge National Laboratory, the nation’s largest science laboratory, has come 10 years later to develop a similar facility at Sandia, the nation’s largest security and engineering lab.
As the newest Sandia Fellow, Lonnie believes this increased focus will change the future of manufacturing and positively impact U.S. security.
“I believe this so much that I left my friends and career in east Tennessee to come to Albuquerque and devote myself to helping enable this vision,” he said. “It’s a lot of pressure, but I have to say I’m having a lot of fun.”
In six months at Oak Ridge in 2013 at the nascent Manufacturing Demonstration Facility, he transformed the additive manufacturing process. He developed it from a tool that slowly printed expensive material, in shapes a cubic foot in size, to a tool that rapidly printed large functional systems weighing thousands of pounds using inexpensive feedstocks costing less than $5 per pound.
The additive manufacturing technique prints raw material directly into computer-guided shapes, reducing waste unavoidable in conventional manufacturing, which must cut blocks of material down to size.
In 2014, Lonnie’s team printed an automobile in real time in front of 120,000 people at a trade show in Chicago.
“From that one demonstration, seven companies started commercializing the technology and a new industry was born,” Lonnie said.
That first vehicle, the Strati, was a 1,400-pound monolithic structure printed in 44 hours. “Most cars are manufactured by assembling close to 20,000 different parts. The Strati had less than 100,” Lonnie said. “However, the true objective wasn’t to print cars. It was to show we could make large structures in days with commodity-grade materials.
“We had eight months to prepare. It was a high-pressure schedule, but I’ve continued to push for these moonshots,” he said. “They force us to accelerate the development of new technologies and fail early, so we understand the real issues that need to be solved.
“I believe strongly that Sandia needs this type of culture. Sandians should be the world experts at how to digitally design and manufacture complex structures using advanced manufacturing technologies. It will help us in our mission, be impactful for our country, be a hell of a lot of fun and is the reason I’m here.”
Some weeks later, Lonnie’s team designed, printed and assembled a replica 1964 Shelby Cobra, which is now at DOE headquarters.
“Printing a full vehicle is still a niche market but does have the potential to change the whole business model of the automotive industry,” Lonnie said.
In 2016, Lonnie shifted from printing large composite structures to metal structures. “Our goal was to show additive manufacturing could be used to transform the tool and die industry as well as diversify the castings and forgings industry. This is a multibillion-dollar industry that our country gave up on, and we can get it back through advancements in manufacturing.”
Later, he used additive manufacturing to transform the complex structure of an artificial hand’s hydraulic actuation tubes and mechanical linkages. By doing this, he internalized the hand’s actuating mechanisms, improved its hydraulics, decreased its size, protected its delicate mechanisms against damage, benefited stroke victims relearning to move their extremities with the hand’s immediate feedback, and, by adding a waterproof “skin,” improved the underwater exploration and repair capabilities of the U.S. Navy.
Lonnie demonstrated his management skills by coordinating the manufacturing response to COVID-19 across 16 national laboratories under the National Biotechnology Virtual Laboratory program funded by the Coronavirus Aid, Relief, and Economic Security Act. His efforts led to partnerships with Coca-Cola Consolidated Inc. and Thermo Fisher Scientific Inc., enabling a supply chain of 10 million test tubes per week and the establishment of a new factory focused on test kits in Lenexa, Kansas. Partnering with Cummins Filtration Inc. and DemeTECH Corp., the team also created a U.S.-sourced supply of N95 respirators, resulting in the production of more than 1 million masks per day and resulting in a new factory with more than 1,000 employees in Tampa Bay, Florida.
As one supporter wrote, “Individually, these contributions evoke reactions of wonder and awe and would stand as the work of a lifetime for most of us. For Dr. Love, they are simply part of enjoying every day.”
As a boy, Lonnie admired his father, who joined the Air Force as a teenager and fell in love with cartography. He recalls his father showing him maps he had made for the Apollo missions and the first pictures from Mars.
“His last project was to lead the digitization of all mapping information,” Lonnie said. “He taught me love of family, loyalty to our country, passion for people and the confidence to take big risks to change the world.”
Lonnie started his career at Oak Ridge as a postdoctoral researcher from the Georgia Institute of Technology in 1995. “I quickly became a survivalist, living project to project. This exposed me to a variety of technologies and skills and instilled in me a passion for pivoting to new research areas.”
The success of these pivots has not escaped Lonnie’s reviewers, who note that his contributions to general knowledge “rapidly penetrate into industrial practice” and who consider him a kind of “embodiment of the Renaissance man.”
One reviewer wrote, “I consider Dr. Love to be the visionary in the deployment of interdisciplinary research to our national needs. … Lonnie is indeed the chief manufacturing officer of the USA.”
Another reviewer notes that Lonnie’s ability to span the gaps between basic and applied research, and technology development, demonstration and commercialization “makes him unique and often difficult to find in our scientific and technology ecosystem,” for which reason Lonnie’s colleagues “refer to him as a unicorn of manufacturing.”