Researchers help improve next-gen reactors
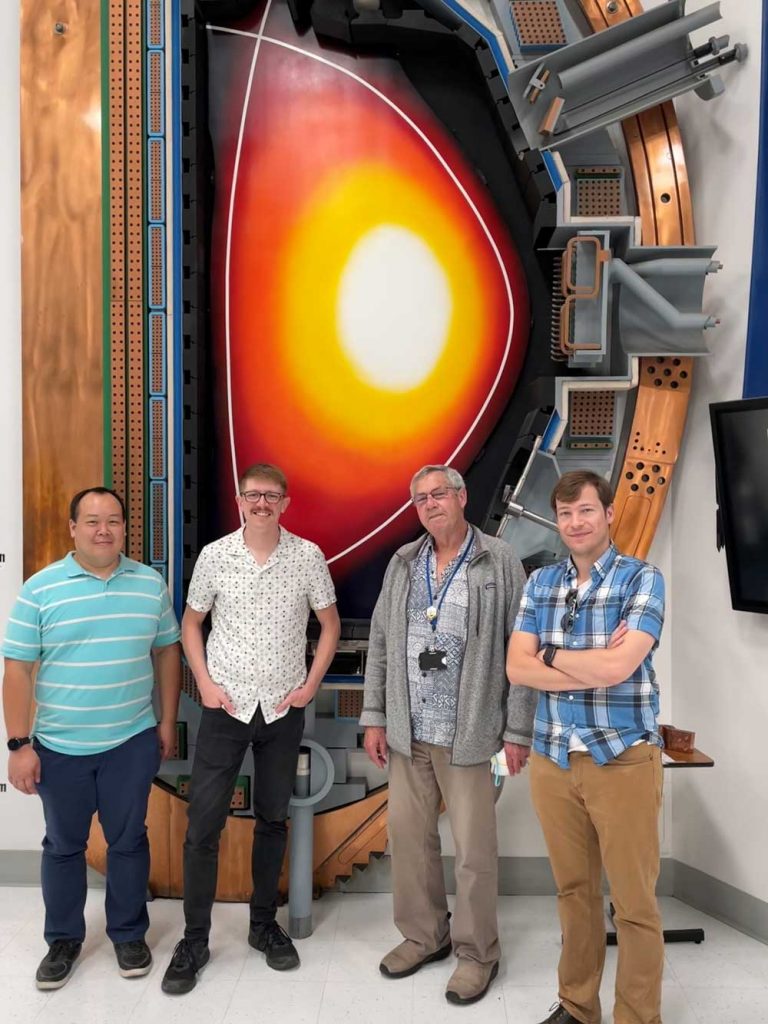
A team of Sandians working on the reactor at the DIII-D National Fusion Facility is testing materials to make the next generation of fusion reactors, in the quest to develop more carbon-free energy sources.
These magnetic confinement fusion reactors, called tokamaks, use magnetic fields to shape plasma into a donut shape that generates power from nuclear fusion. DIII-D is the largest such facility currently operating in the DOE complex. Tokamaks create high heat and particle fluxes which can cause significant erosion of the reactor wall materials. If these materials contaminate the core plasma, it could make it impossible to bring the reactor to a temperature high enough to start stable, safe fusion.
The physics program at DIII-D provides plasma edge diagnostics and measurements in the high heat flux fusion plasma environment as part of a collaboration with a multi-institutional team of more than 200 physicists. The facility, located in San Diego, attracts scientists interested in the science and innovative techniques that will enable the development of nuclear fusion as a next-generation energy source. Sandia collaborates in fusion materials research to test and develop specialized fusion materials for the hot fusion plasma environment.
“Plasma-material interactions deal with what effects the ions and electrons from the plasma have on a material and vice versa,” said Jonathan Coburn, who is part of a Sandia team that collaborates with DIII-D. “Magnetic confinement fusion devices use very strong magnetic fields to generate and then confine the plasma, and so all of these ions and electrons are interacting and producing fusion energy. Inevitably, you have exhaust from the plasma that ends up impacting the walls of your vessel.”
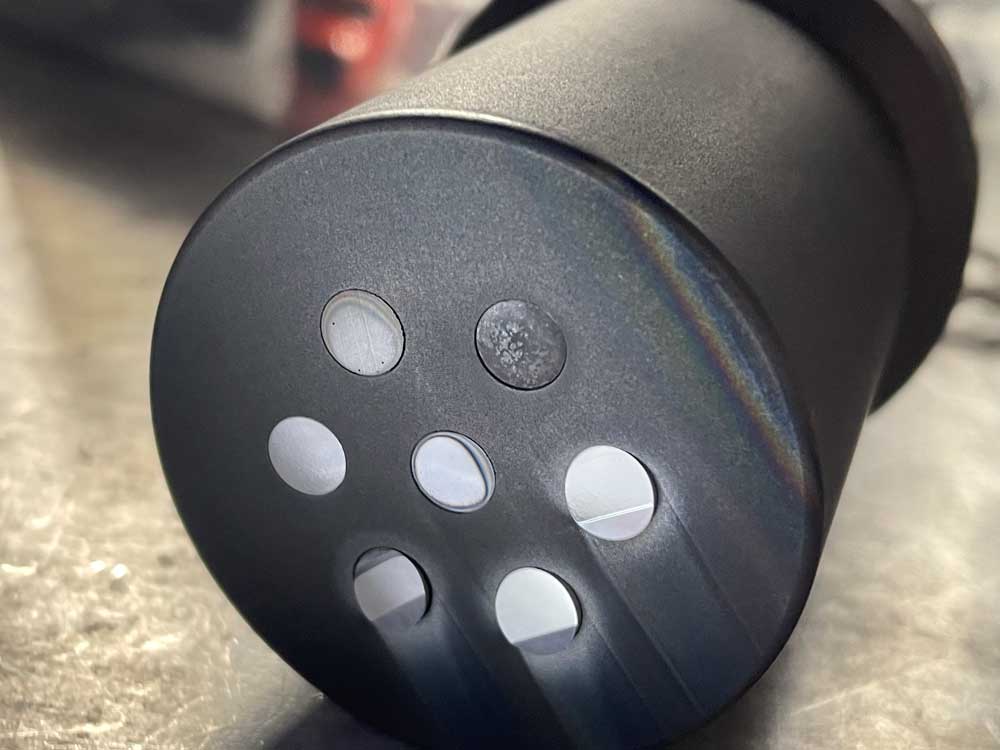
The different plasma-facing components of such a reactor are made of materials like tungsten, carbon and beryllium, which interact differently when irradiated by ions and electrons.
“One of the engineering challenges for building a fusion device is to select the right materials to build all of these components out of,” Jonathan said. “There are plasma physics-based problems that you’re trying to optimize for, and then there are engineering challenges that you’re trying to optimize for. Those challenges are different depending on which type of component you’re building.”
Jonathan and the team perform physical and computational experiments to test material erosion, macroscopic damage, gas retention and recrystallization for tungsten samples after those high-energy interactions.
“The majority of the components in DIII-D are made of carbon, and so in order to perform experiments using different materials, you have to actually have a specific test stand to insert your materials of interest, stick it into the vacuum vessel so it can get close to the plasma and then get your exposures,” he said.
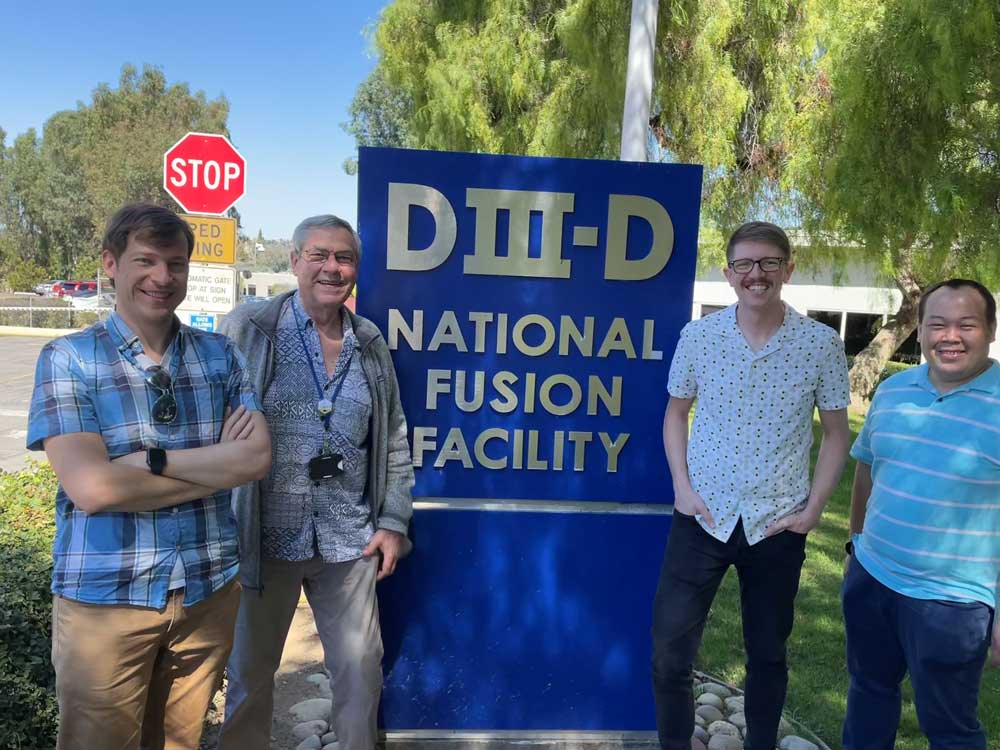
Not only must the team figure out how the materials are damaged by the fusion environment, it must also understand how the energetic byproducts of these plasma interactions are retained in the exposed material.
“When those hot ions impact the material surface they are implanted in the material and neutralize. The length scale for that implantation can vary depending on several factors, and you end up having to figure out what the long-term effects are for what’s implanted,” Jonathan said. “Does it diffuse into the bulk material? Is it eventually released from the surface? What are the consequences of the long-term build-up of implanted species in the material?”
DIII-D creates plasmas with hydrogen, deuterium and helium. In a power-producing reactor, the main fusion interaction will be between deuterium and another hydrogen isotope, tritium.
“What you get out is what’s referred to as an alpha particle and a high energy neutron. The neutron comes out with 14 mega electron-volts of energy that provides the power that you’re then trying to harness to boil water and create steam, turn a turbine and produce electricity,” Jonathan said. “There’s also tritium that is not used up in the core plasma but ends up in the exhaust. Tritium is naturally radioactive and is the main concern from a nuclear regulatory standpoint. How much tritium builds up in the machine over time? I’m seeing if certain alloys of tungsten retain less tritium than others. I am also looking at whether specific materials can prevent the diffusion of tritium through the bulk material, serving as a barrier so that the tritium stays in one place and doesn’t go off into the cooling water, for example.”
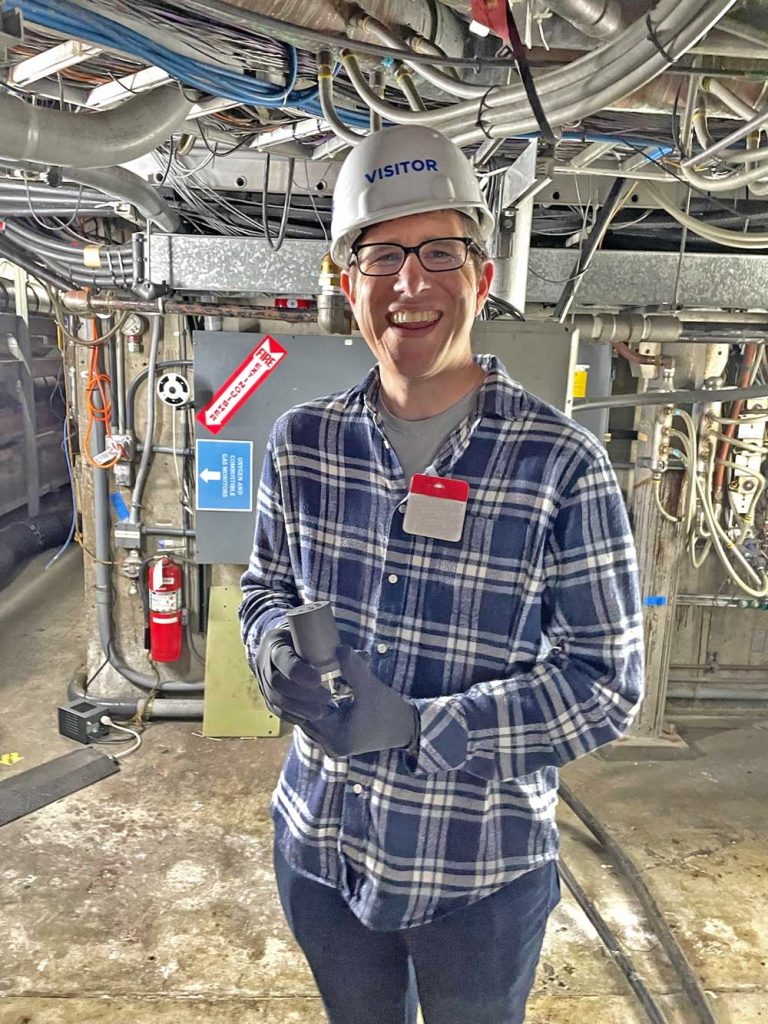
The work to make fusion power generation safer and more reliable is being incorporated into the next generation of tokamak reactors. The best example is the ITER tokamak being constructed in France. ITER, meaning ‘the way’ in Latin, is the largest such reactor. For 50 megawatts of input heating power, ITER will be able to generate 500 megawatts of output power. The team’s work is going to impact that project and help ensure ITER’s success in producing safe, reliable net fusion energy.
“A lot of the earlier work that was done on DIII-D contributed greatly to the overall design of the ITER tokamak,” Jonathan said. “It’s pretty exciting to be able to have the opportunity to do these high-level, high-stakes experiments for the DOE and to advance fusion energy sciences. It’s just a really satisfying feeling for sure.”
Jonathan credited the commitment of his team — Jon Watkins, Dinh Truong, Ryan Hood, Robert Kolasinski, Richard Nygren and Bill Wampler — with advancing the understanding of fusion energy and enhancing Sandia’s reputation for engineering solutions to national and international issues.