Even at 2,000 degrees, the sealed, stainless steel containers did not break open.
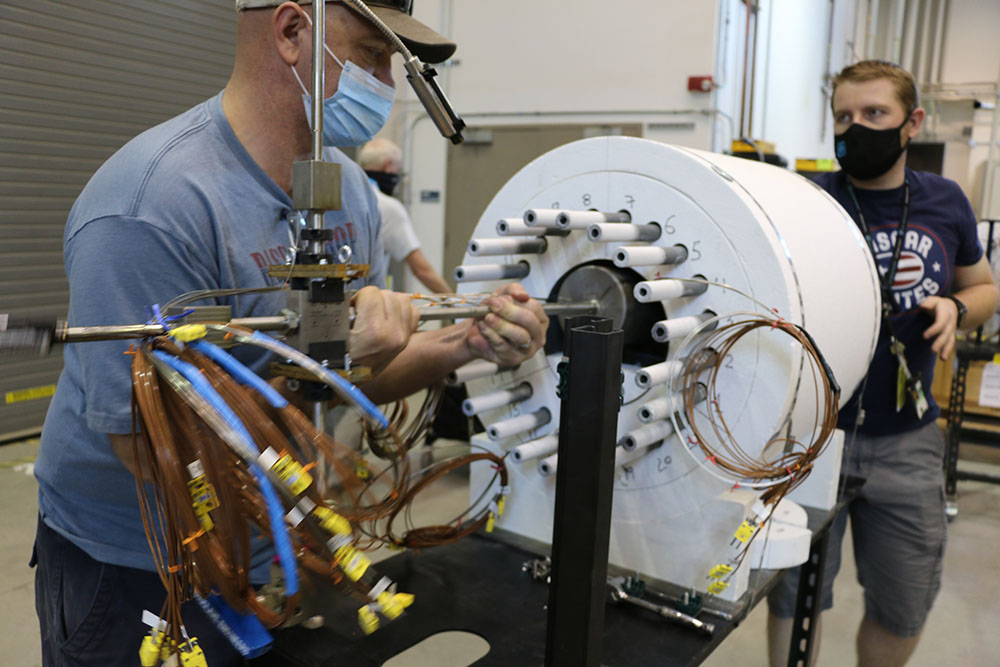
A team of Sandians recently completed a series of tests on specially designed stainless steel containers used by the DOE for storage and transportation of hazardous materials.
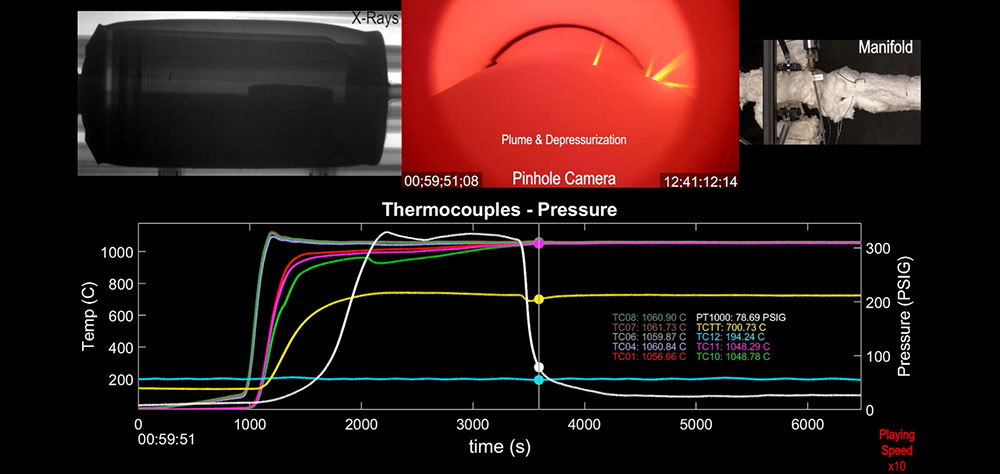
The engineers, technologists and project managers were surprised to find that the containers did not split open when heated to 2,000 degrees Fahrenheit, or 1,100 degrees Celsius. That is almost as hot as a cement kiln.
“These containers were welded shut and heated to 2,000 degrees, so we assumed that they were going to split open, but they developed small pinholes instead,” said Walt Gill, the test director and Sandia mechanical engineer. “We think the material inside reacted with the container itself and produced the pinholes in the container. These tiny holes let out all of the superheated gas without the containers pressurizing and pulling themselves apart.”
The series of 10 tests were designed to mimic a hypothetical raging-hot fire burning at a DOE facility and engulfing a container that had been knocked on its side and left outside of its insulated packaging, which protects it from heat. Since these containers are not designed to withstand such a fire, the goal of the test was to determine how much, if any, material stored within the container would be released into the air during such an accident, said Walt and Austin Baird, the test engineer.
Because the container is a complex, layered system of steel containers, hopefully any material that gets out through a pinhole would be contained or reduced by an outer layer. In 2018, the team conducted similar tests assessing the safety of similar containers.
This information will be used by policymakers to determine safety regulations to protect employees and the environment.
Nested containers for storage and handling
The stainless steel containers are nested in one another as part of a complex layered system, said Austin. There is an inner stainless steel container with a pop-on lid like a cookie tin called a convenience can. Then there are two stainless steel containers that are welded shut: an inner container and an outer container. These three containers are placed within another package for shipping. The containers are used throughout the DOE complex.
The test series started last fall and was conducted at Sandia’s Thermal Test Complex. The Thermal Test Complex performs fire safety tests for a variety of programs from weapon systems to shipping containers, Walt said. The complex also has the capability to design and build custom heating chambers for those tests, as well as integrating the results from field tests with advanced computational modeling.
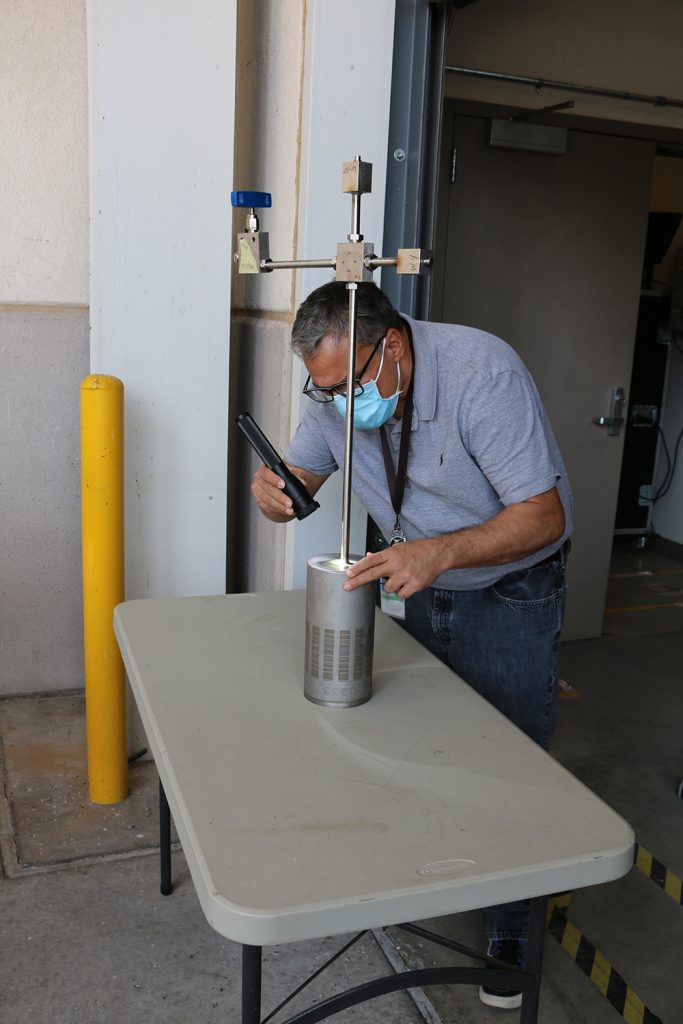
For the tests, the engineers heated the steel containers to 2,000 degrees Fahrenheit in five minutes, and then held the containers at that scorching temperature for four hours in a custom-built cylindrical heater. This set of times and temperatures is designed to mimic a fire inside a building. Many things from construction materials and fire-proof safes are put through similar tests, Walt said.
“One of Sandia’s capabilities is that we have quality assurance under which we can conduct tests,” said Victor Figueroa, the quality-assurance coordinator for the test series. “I think that’s the biggest reason a lot of consumers, like Savannah River, come to us. We have the highest-grade quality-assurance administrative framework necessary to qualify items involved in storing and transporting hazardous material.”
Los Alamos National Laboratory was also involved in the test series. They loaded the predetermined mixture into the containers, Austin said. This mixture contained aluminum oxide — which is used in sunscreen, paints and glass manufacturing — different salts and water in various proportions. The Savannah River Site constructed the pressure manifold for the test and Savannah River National Laboratory tested the containers for leaks.
Since the containers did not breach, like anticipated, the team and their scientific collaborators are analyzing what happened, said Austin. One theory is that the mixture inside the containers reacted with the stainless steel and formed pinholes that allowed the release of pressure without a catastrophic failure. Another theory is that the superheated steam seeped through the thin stainless steel container walls, reducing the pressure inside the containers.
Austin added, “Since the results were very different than what we thought would happen, we’re looking at the gas compositions before and after to determine what kind of chemical reactions took place inside the containers.”
Top-shelf test technology
The Sandia engineering team started planning for the tests about two years ago, which included spending time designing and building the custom test setups. The fire tests also required a lot of specialized recording equipment to collect all the data necessary to inform policymakers.
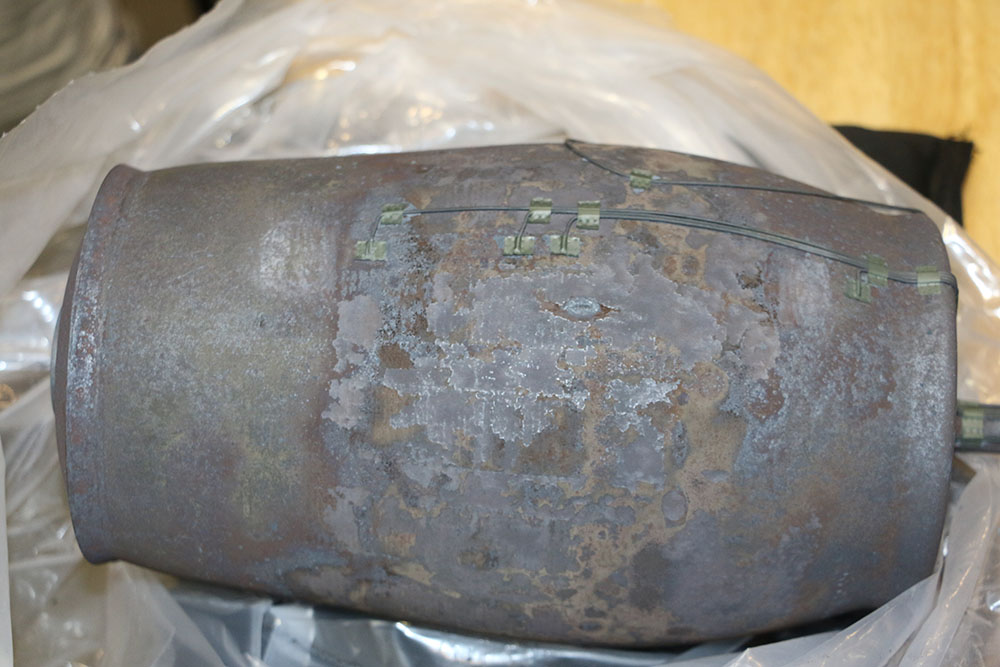
Each container was outfitted with 18 temperature-sensing thermocouples and two pressure sensors, said Austin. Additionally, the team used real-time, X-ray imaging and a pinhole video camera to monitor what was happening inside the heating chamber. They also had a video camera outside the heating chamber.
The team collected all this data with Sandia’s Mobile Instrumentation Data Acquisition System, in partnership with data-acquisition experts.
“The pinhole camera to look inside the test was a big deal,” Victor said. “We were actually able to see, in some cases, and get some idea of how big the pinholes were. We haven’t been able to do it in the past, due to the harsh test environments. As technology gets better, we’re able to make better assessments regarding safety.”
The fire tests are only one part of a suite of safety tests the nested containers, in their shipping configuration, must undergo to mimic the conditions of an accident, said Walt. The shipping packages are designed to withstand a hypothetical accident scenario without any release of material from the containers inside. After installing the container in the shipping package, the package is crashed into a hard surface, crushed by a heavy falling weight, punctured, dunked into 50 feet of water and, of course, burned in a fully engulfing fire.
To be certified by regulators, the whole package must complete all these tests with satisfactory results. He added, “These packages get really abused during the qualification test sequence to show that they’re safe.”
Victor added that the DOE has supported fire testing and qualification of a wide variety of packages for decades at Sandia.
“These packages go on the road and are used at sites across the U.S.,” Victor said. “We, as well as the industry, have to make sure that we design and rigorously test the packages such that they are safe. We have to make sure that we look out for the safety of DOE site workers and the general public.”