Planning, building reconfigurable Agile Lab is unique achievement
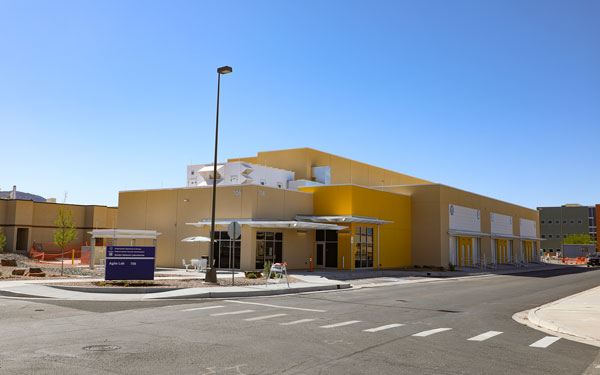
The recently completed Agile Lab in Tech Area I is unique at Sandia. No organization owns it, and researchers can reconfigure the flexible facility quickly when they need temporary lab space.
Completing the lab required a two-year effort by a broad planning and execution team from the facilities organizations.
It started with a trip strategic planner Malia Orell made in mid-2016 to the Aerospace Research Centre, part of the United Kingdom’s Manufacturing Technology Centre. Sandia’s Power Sources organization asked Malia to review the Centre’s concept for flexible space and determine whether the British model would translate well to Sandia.
Designed to be reconfigured quickly for short-term projects, the Aerospace Research Centre was built quickly and relatively cheaply. The Sandia team wanted to model the Agile Lab after it, at a smaller scale. And the Power Sources group needed better space, including a backup dry room, a humidity-controlled area to process lithium-ion batteries.
Ultimately, their efforts resulted in a 15,840-square-foot structure, with about 12,000 square feet of lab space. The overall cost was $12.7 million, which was $500,000 less than estimated.
The Agile Modular Lab Facility is on track to achieve LEED Gold rating, which is a major accomplishment for an industrial building.
More demand than supply
Typically, demands for lab space from Sandia’s multiprogram mission exceed availability. In addition, building age and construction type can limit or prevent repurposing space quickly, and renovations are costly. Facility modernization projects often require turnaround space during construction.
“There is nothing particularly extraordinary about the design of the building,” Malia said, “but the concept of managing it with temporary occupancies is new to Sandia.”
What’s unique about the Agile Lab is that it lets Sandia programs think differently about how to use space, she said. No one owns the building, a marked change in thinking.
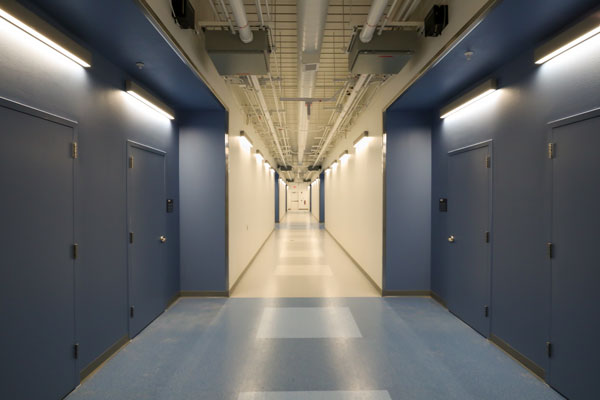
“Sandia can leverage this intentional flex space for short-term lab occupancy needs such as rapid changes in mission, recapitalization of aging facilities or a bridge to a longer-term investment strategy,” Malia said.
“This concept represents a paradigm shift,” said Alicia Brown, another strategic planner in facilities. “Rather than a custom-built, static lab building, the Agile Lab is intended to be an advanced high-bay shell that can flex and be reconfigured quickly as it houses temporary tenants.”
The Power Sources group plans to occupy about three-fourths of the building’s total lab space, which will reduce program risk for their battery production mission while they wait for a permanent home. They hope to identify funding and construct a permanent facility in five years so they can move from their current home, an aging and inadequate facility originally designed as a warehouse in 1949.
“Before the Agile Facility was conceived, there were no other viable options for them to temporarily stand up a reliable production dry room,” said Malia. “This now serves as a stopgap to the longer-term investment strategy.”
DOE funding
The Agile Lab can provide 12 high-bay lab spaces for occupants with various mission needs, including turnaround space for remodeling or renovations. It was built using Institutional General Plant Project funding from DOE and followed IGPP requirements.
The team hopes to use a similar IGPP process for future facilities built without a specific user in mind. To meet DOE/NNSA’s criteria for IGPP funding, a project must support multiple programs, cost less than $20 million and provide site-wide benefit while meeting other use requirements. Sandia planners emphasized providing benefits across multiple programs.
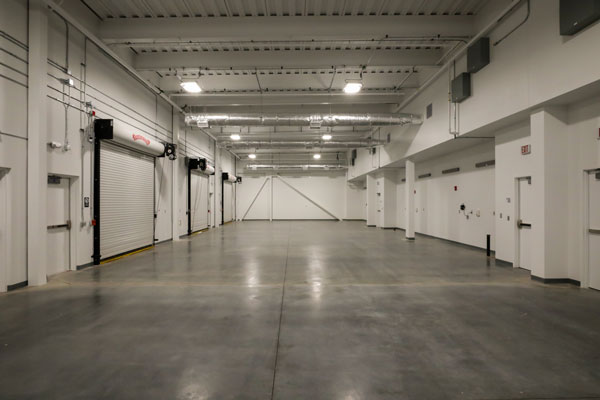
Construction was led by Thompson Construction Inc., a family-owned small business in its first project on the Sandia site.
Josh DeReu, Sandia construction manager for the project, pointed to TCI’s attention to detail. “Despite the full COVID-19 posture for the duration of this project, there were no safety incidents,” Josh said.
Staff from project and construction management and risk management worked with TCI on-site during the Labs’ COVID-19-related maximized telework while other support functions worked remotely.
The building will be a high-bay laboratory only, as it doesn’t meet design requirements for secure space. If needed, though, Sandia could build another facility for use by programs that require high security.
Next up: Geosciences Lab
Agile Lab is part of the NNSA’s Standard Acquisition and Recapitalization Initiative program and can be replicated at other NNSA sites in the complex, including Sandia. The planned STAR Geosciences Lab will be a clone of the Agile Lab and will enable demolition of two of the oldest buildings on the site.
Each bay is 24 by 32 feet and 18 feet high. Each has independent roll-up door access and utilities, with independent power in case of planned or unplanned outages.
“The facility itself has been optimized to provide a blank canvas — a flexible environment — where a multitude of work can be performed,” said planner Jeff Fleming.
Among the design features are a robust mechanical system that permits a variety of activities, electrical systems sized for future expansion and an over-designed roof that can accept additional equipment anywhere it’s needed. The building also has a conference room, breakroom and restrooms.
Following the call for occupancy, the timeframe and square footage were evaluated and compared with each applicant. Each tenant will then fund and build out programmatic modifications for occupancy and then fulfill the required decommissioning at the end of tenancy.
Julie Kelly-Smith, a strategic capital planner, summarized the achievement. She said, “The planning process for this facility was a great opportunity for the planning group as well as the Labs. It allowed us to think about building allocation from a new perspective.”
Associate Labs Director for Infrastructure Operations Harold Yeldell echoed that. “This new model benefits and serves the entire Lab,” he said. “It’s an unprecedented example of flexibility and adaptability for Sandia and its mission.”
The building should be ready for occupancy by late summer 2023.