Most of us rarely look up when we trek into a Costco, Home Depot or other large retailer. Usually, there’s nothing of interest on the ceiling. But if one of Sandia’s newest patents becomes an industry standard, those huge lights illuminating huge spaces may light the way to cooling computers and other electronics.
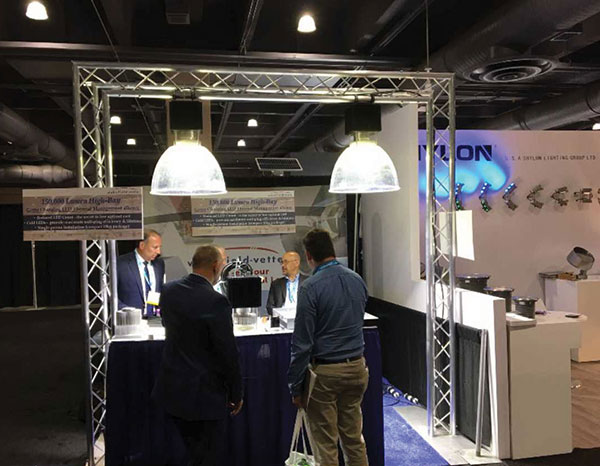
Engineer Jeff Koplow and his team have developed a way to use less energy to cool light fixtures. Their outside-the-box idea is to spin the LED emitters at 1,000 rpm to cool them. The 1,000 watts of electricity required to power the LEDs also powers the spinning emitters, Jeff said.
The rotating LED emitter array generates no perceptible flicker, and thus imposes no degradation of lighting quality. The cooling method also will extend the life of lighting fixtures, because keeping LED junction temperature low drastically improves LED service lifetime and requires less maintenance.
“We wanted to pursue an application with lighting first,” Jeff explained. “It’s a high-visibility application that demonstrates that the Sandia Cooler technology is now viable to businesses and consumers. That gets the conversation started that there is a new approach to cooling for electronics.”
Jeff believes the same technology can be adapted to cooling of computer central processing units and graphics processing units by transmitting the internal data stream across a narrow air gap.
Compact and easy to install
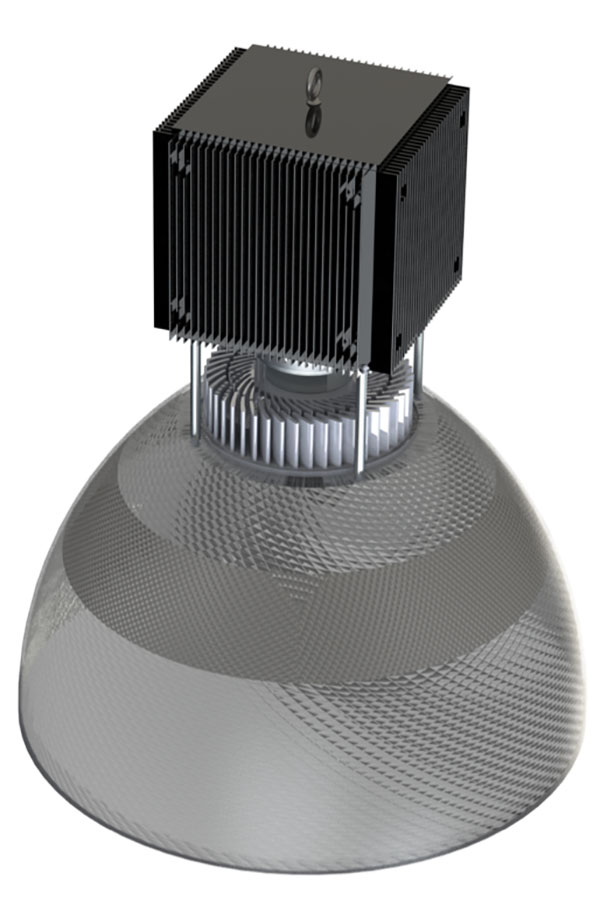
The cooler is extremely compact for such a large lighting fixture, essentially fitting inside the lamp. Traditional heat sink units for such lights are many, many times the size of the fixture and far more challenging to install.
“The idea here was you could get the best of all worlds,” Jeff said. “Use the minimum number of LEDs, keep them really cool so they would last the whole life of the light fixture and do that in a really lightweight and compact form factor without making any sacrifices to efficiency.”
Most of the prototype was built by Sandians.
“Construction of the three product demo units was intensely collaborative,” Jeff recalled. “There isn’t a supplier making the Sandia Cooler. The parts would come in and we would put them together and test successive prototypes. There was also a learning curve from the standpoint of design for manufacturability, but we got there.”
Jeff also complimented Sandia’s involvement with DOE’s Technology Commercialization Fund.
“I thought to myself throughout the process, ‘This is exactly what the TCF was designed to do,’” he said. “Bring together a really productive collaboration with people whose incentives are fully aligned, work toward a product and overcome all the hurdles together. The whole process was really satisfying.”