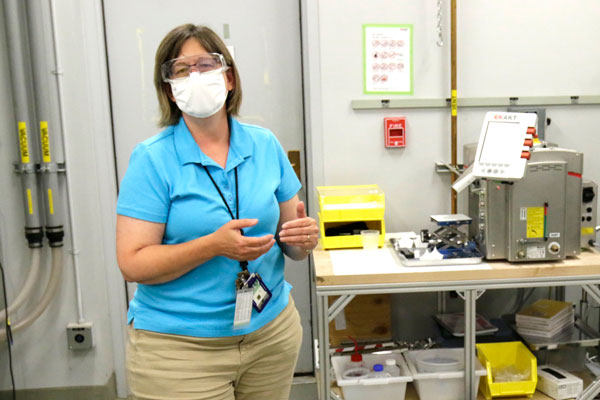
The novel approach of Integrated Service Delivery being practiced in several centers within Sandia’s Integrated Security Solutions Division was tested to its utmost this year, as departments had to suddenly figure out how to accommodate a remote workforce and then just as suddenly overcome dozens of challenges to bring people back to work safely on-site.
The outbreak of COVID-19 brought broad changes of life, and no one was left untouched. All of the Labs’ sites were affected by stay-at-home orders to some extent. In California, where a large part of the division is located, the governor mandated a statewide quarantine on March 19. That order was in force for more than eight weeks before it was eased. Sandia at first sent most workforce members home but quickly needed to figure out a new normal for on-site operations once NNSA issued a return-to-work order a few weeks later.
National security in the balance
The division is home to key centers focused on nuclear deterrence, energy, cybersecurity and biothreats. COVID-19 threatened the nation, including those at Sandia working to keep our country safe.
“We have some responsibilities that are 24/7 operations, where we have to be present at all times. These are really critical to national security,” Associate Labs Director Andy McIlroy said of the division he leads. “We monitor and maintain systems that are out in the field. Those systems must be on regardless of whether there’s a pandemic or not. And so we have responsibilities that are very key to the nation’s security — not in a theoretical way but in a truly operational way, ultimately. I think that was a big driver for us to try to get our critical functions back to work as soon as we could.”
This was especially important, he said, for those who had to be on campus and could not work from the safety of home: security personnel, custodial staff and other mission-critical workers.
Thus, new issues of safety — making sure no one contracts COVID-19 while at work — had to be thought through, a complex process that no one person had all the answers for in an unprecedented outbreak that was emerging quickly.
First things first
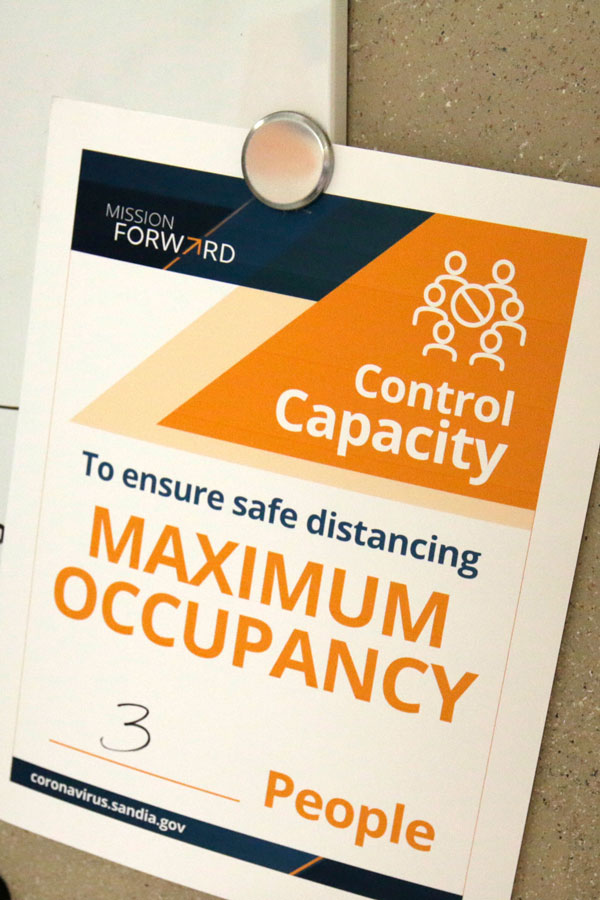
The Chemistry, Combustion and Materials Science Center is one of eight centers within the division, performing critical experiments and supporting classified nuclear deterrence research.
“We prioritized the activities that directly support the nuclear weapons program because we support them in a lot of materials analysis work,” said Sarah Allendorf, center director.
Sarah and her leadership team, including Chris Moen, head of the engineering and transportation sciences group, began to think about how to make sure their buildings and labs were as safe as possible.
“First thing we had to do was figure out what are the hazards and what are effective ways of controlling those hazards?” Chris said, adding that this was no easy task because there were so many unknowns about the novel coronavirus, such as how long it lived on surfaces and how close you needed to be to another person to contract it.
“We decided to use an engineered-safety approach,” he said. “Because our center has so many diverse types of equipment and spaces, we had to review each of our safety cases and write an addendum on how to mitigate for COVID-19.”
But chemical and materials scientists are not necessarily well-versed in biological threats. They needed help to understand the risks. So they leveraged Integrated Service Delivery, a system they helped pioneer, to draw in experts from across multiple centers and use their expertise and connections to help tackle challenges.
Turning to the experts
The Chemical, Biological, Radiological, and Nuclear Defense and Energy Technologies Center within the division is home to medical doctors, virologists and other biological scientists who were already hard at work trying to understand the novel coronavirus and what was making it spread so rapidly across the planet.
When Craig Tewell, the center’s acting director at that time, was asked by Sarah if he had anything that could help inform her team’s thinking, there was little to draw from.
“In the early days, there was not much guidance to lean on. There was one OSHA (Operational Safety and Health Administration) document,” Craig said. “For example, there was not a lot that was agreed on at that time about how the virus was transmitted.”
But the center Craig was leading had an advantage — it is home to a biosafety lab, classified as a BSL-2, where researchers can work with “moderate-risk” agents associated with human disease. Drawing on advice from BSL-2 manager Cathy Branda and biochemist Joe Schoeniger, Craig and his team developed guidelines for “treating the world like a BSL-2.”
“My center was at the forefront of this,” Craig said. “Sarah and I, in particular, were talking about an engineered-safety approach. Our goal is to prevent an on-site transmission, and we had to trust our level 1 managers and senior managers to develop a safety system.”
He shared some rough biological guidance with Sarah and her team. They also turned to another Sandia group with experience in pandemic response.
Engineering safety in every room
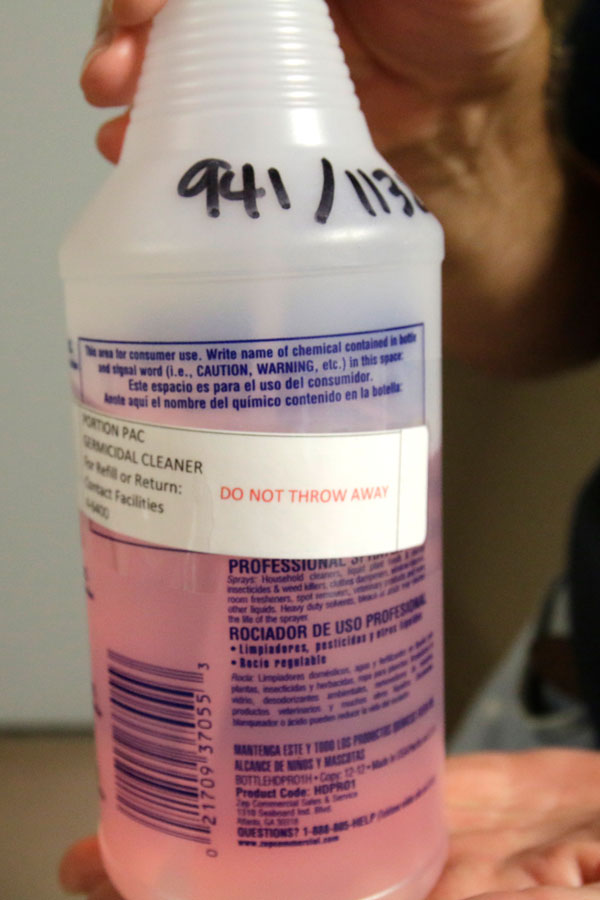
Mike Roth works as part of Sandia’s industrial hygiene team at the California campus. He is trained in pandemic response.
“The first thing we had to do was make sure everyone felt safe about being on campus,” Mike, who worked on each safety case as the site slowly reopened, said.
Mike’s 20-plus-year career as an industrial hygienist has taught him a very valuable lesson.
“Public health — it’s a battlefield. You’re fighting a crisis,” he said, adding that Sandia’s industrial hygiene team applied past lessons to mitigate the unknowns of COVID-19. “There’s a lot of guidance about communicable diseases. Even with this new novel coronavirus, it follows similar patterns.”
Mike worked directly with front-line managers, like Dawn Skala, in the Chemistry, Combustion and Materials Science Center. Dawn, who manages 10–12 labs, had to take the policies being developed by Sarah, Chris and the rest of the center’s management team and apply them.
“We had to look at the guidance and determine how it would work in a particular lab with specific hazards,” she said. “Sometimes we decided to limit the number of people in the lab. Other times the solution was to wear gloves or disinfect equipment. We conducted virtual walkthroughs of each lab with Mike and his team and developed five safety cases to cover those labs.”
Dawn said that the level of teamwork and collaboration was incredibly helpful.
“They (the industrial hygiene team) added to our safety steps and understanding,” she said. “They thought through the process with us from an end-to-end perspective.”
Chris agreed. “It was hugely impactful,” he said of the contributions from the environment, safety & health department and the industrial hygiene team.
“While we could come up with a safety approach for our labs, there were things we hadn’t even considered. For example, we have a lot of PPE (personal protective equipment) because we work with lasers, but the team would warn us not to use particular chemicals (on the PPE) so that our PPE wouldn’t be ruined. Or they’d say, ‘Okay, you wiped the surface clean, but how are you disposing of the wipe?’”
Supply-side issues
After Sarah, Chris and their center staff collaborated with Craig’s and Mike’s teams on an engineered-safety plan for resuming critical activities to support Sandia’s national safety missions, Sandia/California faced a new issue — one felt by almost every American citizen in March and April.
“The supply chain was always the most critical part of the pandemic,” Mike said. “Things like spray bottles — that you wouldn’t think would be in short supply — were gone. Cleaning supplies and PPE like eyewear and gloves. No one had any. Fortunately, we were able to get a supply of disinfectants from New Mexico very early on.”
Mike said the ES&H team became creative and innovative.
“Our team has been making disinfectant solutions, and we work with our partners in the logistics department to distribute disinfectant wherever it is needed,” he said.
He applauded the entire ES&H department for devising new solutions when faced with supply challenges, as well as having enough people on campus to safeguard the facilities. He also credits the collaborations with the various centers, which he said have been “adaptable and resilient” throughout this pandemic crisis.
Teaming for success
Chris said what happened on-site as people started coming back to work was as impressive as the effort to get back to work.
“It was a site effort, not just something in our center,” he said. “The Energy and Homeland Security Program Management Center handled all the logistics of how to bring everyone together safely and how to order supplies. They helped take that logistical load off our managers so they could focus on keeping our people safe and getting them back to work.”
That was exactly the kind of relationships and collaboration envisioned as the goal of Integrated Service Delivery — providing solutions for operational issues that are seamless and readily integrated. It was an approach mirrored throughout the division as people needed to continue to protect the national interest.
For Dawn, the impact was profound on the highest scale.
“I think the best part about going through that process is that it helped calm many people’s concerns about going back to work,” she said. “I was extremely impressed by the assistance we received from the biological researchers and the industrial hygiene team, because the potential consequence was someone falling sick and even dying. They really were available whenever we needed them and gave consistent advice. Through their efforts, our center staff heard the message that Sandia wants to keep us safe.”