From the March 28, 1969, Sandia Lab News:
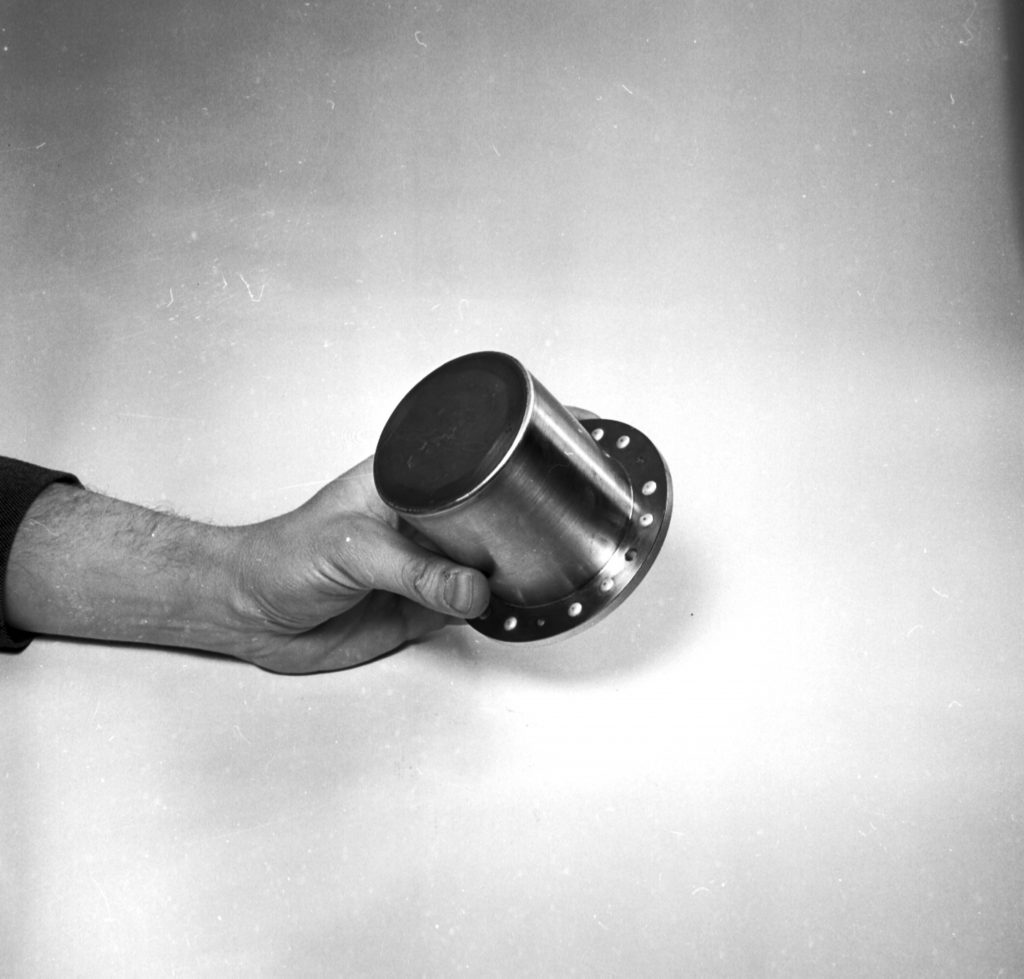
Sandia Laboratories is completing a six-month crash program of analysis and safety testing of a cup-sized radioactive heater scheduled for use in Project Apollo.
Sandia’s job is to ensure that the heaters, which contain plutonium, would survive atmospheric reentry and earth impact if the mission were aborted.
“This accelerated program is a prime example of how we are able to respond quickly to the needs of a new project,” says Gene Blake, former manager of the Aerospace Nuclear Safety Department.
“It shows how, in a short period of time, Sandia can make significant contributions to the safety of a design through analysis and environmental testing.”
The heaters are designed and built by AEC’s Mound Laboratory in Miamisburg, Ohio, and will control the temperature of an instrument package to be left on the moon by the Apollo astronauts. Since the intense cold of the lunar night – as low as 250 degrees below zero – would cause the electronic instruments to stop operating, this additional heat source is required. NASA selected the radioisotopic‑fueled heater, which gives off heat as the radioactive material decays.
The two heaters used in the package will keep the electronic instrumentation at temperatures between -65° to +160° – a range within which the instruments will function properly.
Sandia’s safety evaluation produced aerothermodynamic information which helped engineers at Mound Laboratory arrive at the final design. Safety questions were answered by mathematical computations backed up by testing of models and components in Sandia’s environmental testing facilities.
The shape of the heater, and its path and velocity through space were used to determine the heat, pressure, vibration and shock which it might experience. In turn, the design of the package itself – particularly its ability to withstand shock and heat – was analyzed to ensure that it could also survive these conditions.
Dynamic shock machines, rocket sleds, reentry arc tunnels and other facilities in Sandia’s environmental test area were used to obtain this data. Heater packages were “re-entered” in a supersonic stream of gas which subjected them to temperatures approaching 3500°F. The packages were also accelerated by rocket sleds into a variety of targets to determine their survivability.
Small size of the heat source posed some problems. In an air drop test over Sandia’s Tonopah Test Range, for instance, radar tracking of the falling module was not possible because – at a height of two miles – the target was too small to detect.
To overcome this problem, the aircraft’s position was precisely fixed by radar, a radio signal was transmitted at the time of the drop, and the impact of the module was recorded by a geophone – a microphone-like instrument which picks up vibration transmitted through the earth. With this data, Sandia mathematicians were able to compute the speed of impact – about 120 miles an hour.