Local assistance aims to help companies make national impact in energy sector and materials
Along a stretch of Route 66 that runs through rural eastern New Mexico stands a defunct ethanol plant in the town of Tucumcari. Still hanging inside the building, calendars from 2010 mark the year it closed, and six massive fermentation tanks — each one 35 feet tall and 55,000 gallons — sit empty.
Drought has depleted local corn harvests that were supposed to serve as feed stock, rendering the facility economically useless and spoiling two attempts to reopen it. A third try began in 2016, when Tucumcari Bio-Energy purchased the plant. This time, says the company, things are going to be different because it’s not going to use corn.
Through New Mexico Small Business Assistance (NMSBA), Sandia is solving technical challenges for Tucumcari Bio-Energy and, in a separate project, helping a cohort of companies led by PJ Woodlands to figure out how to market new composite materials made from forest slash.
Both companies are pursuing innovative ways to recycle waste, and both projects were among 10 recognized by NMSBA this year. In 2017, the state of New Mexico, along with Sandia and Los Alamos national laboratories, invested $4.6 million helping 346 small businesses in 28 counties through the NMSBA program. Since its inception in 2000, the program has helped 2,797 businesses in all 33 New Mexico counties.
Sandia assistance is advancing both companies’ plans. Tucumcari Bio-Energy has reduced its financial risk and can pursue financing to reconfigure the plant. It is pursuing private investors and Department of Agriculture-backed loans. And PJ Woodlands now can market its product and negotiate financing. It is also negotiating a site for its new production factory.
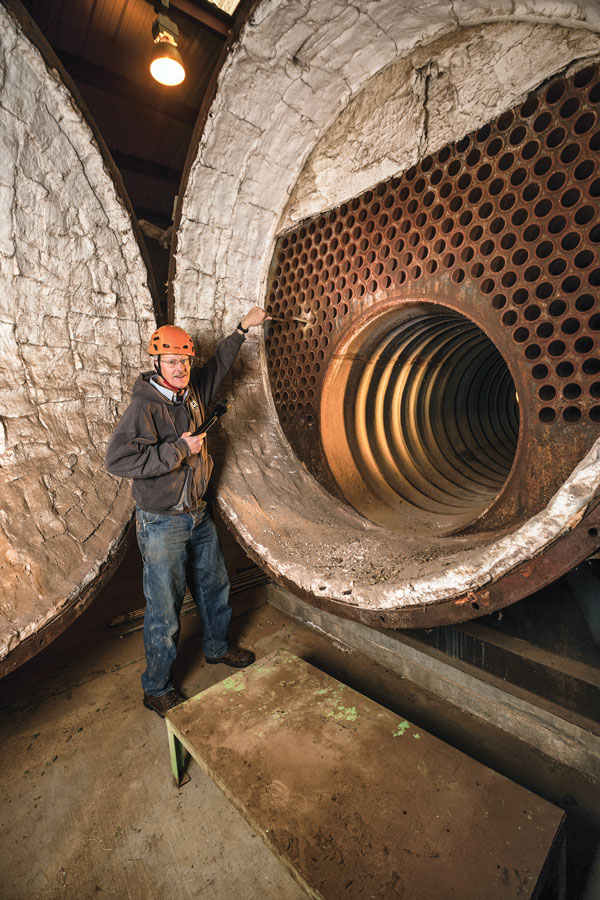
Thousands of gallons of (simulated) manure
Instead of corn, Bob Hockaday, president of Tucumcari Bio-Energy, has grand plans to fill his plant’s fermentation tanks with manure, which happens to be quite abundant around agricultural Tucumcari, to produce and sell methane-based natural gas. The product is designated a cellulosic biofuel under the Renewable Fuel Standard, which entitles producers to certain federal benefits for helping reduce greenhouse gas emissions. If the company turns a profit, dozens of closed and idle ethanol plants around the country could replicate the model and reopen their doors as well.
To turn manure into fuel, you must churn and carefully heat a slurry — “witch’s brew,” Hockaday affectionately calls it — of water, manure, digestive bacteria, waste whey from cheese and other ingredients. If the brew doesn’t mix evenly, it can overheat and boil over like a foul pot of spaghetti. Even if small areas inside the tanks get too hot or too cold, the bacteria, which ultimately produce the methane, can die or go dormant, respectively.
Perfecting the process through trial and error would have been too costly, so “we said, ‘Let’s go and use some science on this,’” and they applied to NMSBA, Hockaday explained.
“Some of the best fluid dynamics modeling is done at the national laboratories,” Hockaday said. Fluid dynamics is the study of how liquids and gases move.
Nuclear waste simulations
Sal Rodriguez, a nuclear engineer at Sandia, led the effort to identify potential trouble spots in the tanks before adding even a drop, or a plop, of slurry. Rodriguez used computer software similar to that used to simulate liquid nuclear waste at sites in the northwestern U.S. This mapped out how slurry will circulate inside the Tucumcari Bio-Energy tanks when the mixing propeller is spinning, hot fluid is rising, cold fluid is descending and methane gas is bubbling to the top. Rodriguez found areas that weren’t expected to mix well and showed Hockaday how to modify the tanks to minimize the risks of over- and underheating. Rodriguez also calculated the ideal temperature range to maximize methane production.
Rodriguez and Hockaday now are working together on the project’s second phase to perfect the computer simulation by adding more detailed physics.
“We’ve got the pieces. We’ve got the tools,” said Hockaday. “I think we can solve the problem.”
The project benefits Sandia, Rodriguez adds, because it’s improving the Labs’ software. Both Hockaday’s slurry and nuclear waste happen to share an unusual trait among liquids: both liquids thicken under pressure. This allows Sandia to use one to better understand the other. Improving the software, Rodriguez says, could in turn benefit any facility or institution that keeps or studies nuclear waste.
Taking brush to the bank
Sandia’s Structural Mechanics Lab is a rewarding workplace for people like test engineer Tom Bosiljevac who enjoy understanding why things break. The lab is a maze of equipment, from handheld tools to larger-than-life machines, that pull, press, stretch and squeeze with up to hundreds of thousands of pounds of force.
Tom acknowledges, though, that most of the time his job is making sure things don’t actually break. He tests materials that Sandia designs to endure intense stress. Through NMSBA, he got to apply his experience to the wood-plastic composite material Altree.
Bosiljevac worked with Albuquerque-based PJ Woodlands on the project, which represented its partners: GL Environmental Inc.; Highway Supply LLC; Mt. Taylor Machine LLC; P & M Lumber Inc.; and P & M Signs Inc.
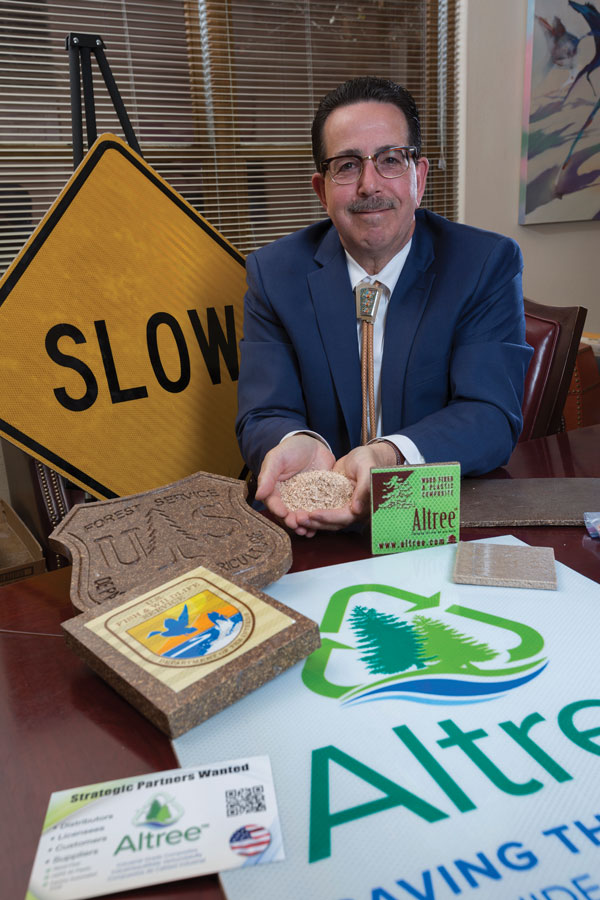
PJ Woodlands is making plans for a new factory that reuses forest waste: small trees, branches, stumps, leaves and berries that loggers leave behind and that foresters lop, pile and burn to thin wooded areas at high risk of fire. The company turns this forest slash into a fiber which, when blended with No. 2 plastic (like milk jugs), forms a stiff composite material designed to replace aluminum road signs. The company is further developing it as a green structural panel for building projects.
“We deal more with alloys and metals,” Tom said. “We were interested in this wood-plastic composite because it’s a new material for us, so it helps develop our knowledge base. It also helps us develop our testing abilities and familiarize ourselves with new types of testing equipment.” As a small plus, he got to break it, intentionally.
PJ Woodlands can produce Altree at a fraction of the cost of aluminum, one reason managing director Tony Burger believes it’s a promising low-cost, alternative material for signage. He says those savings could add up fast for municipalities that spend a bundle each year replacing stolen and damaged signs.
But prospective customers need detailed specs about the new material — how much weight it can hold, how fast it burns, how tightly it holds onto nails and screws and more. So PJ Woodlands asked Sandia for help measuring the material’s limits.
“We knew it was good, but we didn’t know to what degree,” Burger said.
This kind of testing is common but expensive because industry-standard methods can be very proscriptive and require specialized equipment.
Not only did the testing provide PJ Woodlands the specifications it needed for new customers and financing, but it also revealed a potential new market for Altree as a ballistic material.
Tom and his team discovered that while it’s not strong enough to stop a bullet, Altree absorbs a lot of energy before breaking, and it doesn’t shatter, so it doesn’t create hazardous shrapnel. Engineers see potential in such materials because their ability to absorb energy makes buildings more seismic- and blast-resistant.
In addition to Tucumcari Bio-Energy and PJ Woodlands-led Altree development, NMSBA recognized two other Sandia-led projects in 2018:
- The Labs helped Albuquerque company Voss Scientific improve the performance of a dime-sized sensor that measures short bursts of electrical current.
- Sandia was also recognized for ongoing service to the small business community through its geometric dimensioning and tolerancing courses, which teach business owners how to add value to products with precision manufacturing.