Summer institute introduces Sandia interns to NW work
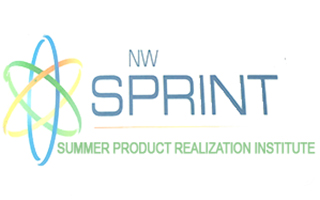
The “sprint” part of Sandia’s summer NW SPRINT competition for interns was more of an all-out run.
Three intern teams, augmented by Sandia staff, designed a nuclear weapon component, built it with additive manufacturing techniques, and tested it on a centrifuge — spending eight weeks on work that Advanced Mechanical Design Senior Manager Carl Vanecek (2610) says traditionally might take a year.
Along the way, interns were “exposed to the whole product realization process as they are developing concepts, creating prototypes, simulating their design, and actually testing their product to see how it performs,” says Mechanical Design Manager Fran Current (2996).
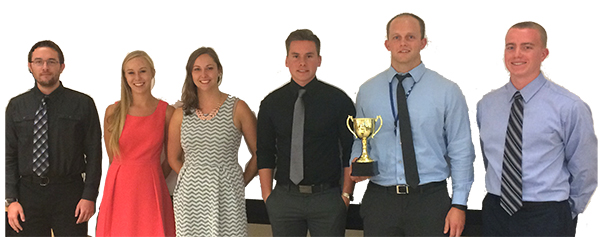
CHALLENGE WINNERS — Student members of the NW SPRINT winning team pose with their trophy after challenge pose after judging Aug. 4. Three intern teams, augmented by Sandia staff, spent eight weeks this summer designing a nuclear weapon component, building it with additive manufacturing techniques, and testing it on a centrifuge. (Photo by Tommy Woodall)
NW SPRINT, for Nuclear Weapons Summer Product Realization Institute, formalizes a contest that began in 2015 when interns from three Sandia centers spent the summer developing designs for a nuclear weapon discriminator mechanism, using emerging additive manufacturing techniques and collaborating with Sandia’s partners at the Kansas City National Security Campus (KCNSC).
The contest generated innovative designs, and Sandia put in a provisional patent application for one of them, Carl and Fran say. “You wouldn’t put that component into the stockpile out of the box, but it’s intriguing because they’re designs you wouldn’t necessarily think about,” Carl says.
2015 contest led to summer institute competition
Staff members participating enjoyed the contest so much, and felt that interns got so much out of it, that they wanted to do it again.
So the Additive Manufacturing Discriminator Design Competition morphed into NW SPRINT. Championed by Weapons Engineering & Product Realization Div. 2000 VP Gary Sanders and Div. 1000 VP and Chief Technology Officer Rob Leland, it will carry forward with a new contest each summer. Its goals: have non-traditional teams develop innovative concepts using new technologies, identify gaps in those technologies and how to address them, and create a pipeline for recruitment.
Interns Ryen Ormesher and Karl Johannes, who competed both years, say more Sandians were aware of this year’s contest, which involed designing a small component that senses acceleration. The device had to actuate and close its contacts under sustained acceleration — a requirement that simulated environments in a typical rocket launch.
Requiring teams to demonstrate functionality “increases the challenge pretty significantly,” Ryen says.
It also compressed the contest timeline. At the mid-point in 2015, Ryen’s team was still deciding among designs. By this year’s halfway mark, the team was prototyping a design “to make sure that we have time to go back and redesign and retest,” says Ryen, a junior biomedical engineering student at North Carolina State University. “Allowing enough time to do multiple iterations and multiple prints has been the hard part.”
Karl’s team had narrowed its choice to two designs and was printing and testing parts to see how they’d function in a system, preparatory to printing full systems to test. “It’s helpful that we had more people working on it this year,” says Karl, now in graduate school at the University of Colorado Boulder after receiving a mechanical engineering degree this year from New Mexico State University (NMSU).
Teams included interns from several universities
Karl’s team — which won the competition — was sponsored by Carl and included members from the University of New Mexico, Cornell, New Mexico Tech, NMSU, and the University of Florida. Ryen was on a team sponsored by Surety Analysis Senior M anager Tommy Woodall (0430) that also had members from the University of Texas, Missouri University of Science and Technology, NMSU, and Texas A&M. The team sponsored by Advanced Weapons Systems & Surety senior manager Manuel Contreras (2223) included members from New Mexico Tech, UNM, Oklahoma State University, and Community College of Denver.
Teams were judged Aug. 4 by a panel made up of Sandia distinguished mechanical engineers Daniel Petersen (2613) and Allen Roach (2735), Labs’ additive manufacturing Deputy Director Mark Smith (1801), University of Texas mechanical engineering professor Carolyn Seepersad, and KCNSC senior technical manager David Spieker.
The competition drew about 20 interns, either full or part time. Each team included interns and newly hired and more experienced staff members, helped by experts in safety from Org. 400, 3-D modeling from Org. 2900, manufacturing from KCNSC, materials from Org. 1800, and additive manufacturing from around Sandia.
Deputy Chief Engineer Scott Holswade (2200) says the contest promoted “accelerated cycles of learning.”
Completing design cycle in short period
“We took people more or less off the street and gave them an assignment they were able to complete in a very short time, eight weeks. It’s amazing that we were able to do a complete design cycle in that amount of time,” he says.
Technology is changing quickly and the pace of change is accelerating, he told the interns at a June kickoff. “We need that ability to rapidly think about things, to solve problems, and to get our models and simulations to agree with what we’re seeing in the lab.”
It’s also more inclusive. The challenge brought in people who had little exposure to the weapons program and took them through an entire design cycle in a short period, in contrast to a more traditional approach of years of apprenticeship-type training, Scott says. “It lowers barriers,” he says. “If we can do it with interns and early-career staff, we can certainly do it with the wider Sandia population.”
Fran, who works in the B61-12 program, says that until the summer contests, it was hard to find significant assignments for interns because of the classified nature of weapons work. Now, he says, “I feel very comfortable bringing in interns knowing that I’m going to have something for them to work on that’s meaningful throughout the summer.”
Ryen says seeing a project through from start to finish was a unique intern experience. “We get to learn a lot about the design process and what goes into making sure that whatever your design is, it meets the requirements you’re given.”
Karl enjoyed using additive manufacturing in 2015 at Sandia and wanted to return. “I really like everyone that I worked with, so coming back for another summer seemed like a good idea. Certainly NW SPRINT has been fun.”