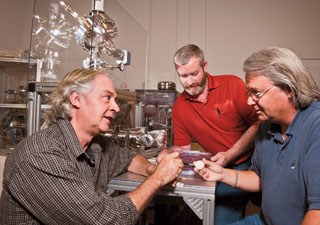
HELLO, MR. CHIPS — Juan Elizondo-Decanini (2735), left, Matt Senkow (2735), right, and Kevin Youngman (2625) discuss a new configuration for neutron generators. A three-year Laboratory Directed Research & Development project Juan led demonstrated the basic technology necessary for a tiny, mass-produced, chip-based neutron generator that he said can be adapted to medical and industrial applications. (Photo by Randy Montoya)
It was a figurative whack on the head that started Sandia distinguished technical staff member Juan Elizondo-Decanini (2625) thinking outside the box — which in his case was a cylinder.
He developed a new configuration for commercial neutron generators by turning from conventional cylindrical tubes to the flat geometry of computer chips. For size comparison, he says small neutron generators, which are like mini accelerators, are 1 to 2 inches in diameter.
“The idea of a computer chip-shaped neutron source — compact, simple, and inexpensive to mass-produce — opens the door for a host of applications,” Juan says.
The most practical, and the most likely to be near-term, would be a tiny medical neutron source, implanted close to a tumor, that would allow cancer patients to receive a low neutron dose over a long period at home instead of having to be treated at a hospital, he says.
The technology is ready to be licensed for some commercial applications, but other more complex commercial applications could take five to 10 years, Juan says.
“It’s really revolutionary technology,” said Stewart Griffiths, who retired in December as a senior scientist/engineer in Center 2100. “Juan’s knowledge, insights and creativity into this enabled this really big jump from today to how we might do neutron generators in the future.”
Stewart said the impact won’t be known for years, however. “The maturation of the technology is still needed, but if that process is successful, it will have a huge impact,” he said.
‘Deep in the proverbial box’
An independent committee of Sandia managers selected the technology as one of the Laboratories’ eight submissions to compete for the R&D 100 awards in 2012.
A three-year Laboratory Directed Research & Development (LDRD) project Juan led demonstrated the basic technology necessary for a tiny, mass-produced neutron generator that he said can be adapted to medical and industrial applications. He says his team is seeking funding to make sure it works reliably and can be scaled to meet needs.
Juan says it all started when now-retired Dept. 9610 senior manager Mike Sjulin told researchers he needed neutrons and he didn’t care how they were produced. Before that whack on the head, Juan says, “we were deep in the proverbial box, concentrating on making the cylinder more cylindrical.”
Traditionally, accelerator-based neutron generators with deuterium ion and tritium targets have operated on cylinders, which makes it easy to control the electric field and ion beam shape, he says. But that geometry also limits size, beam current, and neutron output.
Could they produce one neutron per transistor?
So members of Juan’s team turned to computer chip geometry. Noting chips have two transistors per bit, they wondered if they could produce one neutron per transistor — what one of Juan’s peers dubbed a “neutristor.”
“Once you see it, it’s kind of obvious … but before that nobody ever thought of it,” Juan says.
The fun began with the technology challenges that presented, he says.
The team’s first step was to discover whether it was possible to make a generator shaped like a flat computer chip with all surface-deposited components — everything from the ion source to the target, Juan says.
“We did not even know the proper scaling to go from cylindrical to flat, or from high operating voltages to lower operating voltages,” he recalls.
However, he says, a cross-section diagram of the simplest diode-based neutron tube translated into the ideal surface-mounted topology, and team members knew they had the tools to design it.
The LDRD project pulled together people from all over Sandia, including design, microelectronics, materials, ceramics, precision fabrication, ion gas loading, engineering, and detection calibration, Juan says. He also credits manager Mike Eatough (2735), saying, “It couldn’t have happened without his ability to open up space for me to be wild and crazy and talk nonsense.”
After seven months of working on an ion beam lens design and an additional six months doing the necessary modeling, the team scaled things down.
“The challenges switched to make the device micron size, and then nano size, until we could scale it down no more,” Juan says. To date, the project has demonstrated scaling to the millimeter and micron size, with neutron production demonstrated in the millimeter size and ion sources demonstrated in the micron size, Juan says.
The team moved from a millimeter package that looks a like a printed circuit board to a micron package to the concept of mounting the package on a computer chip. The chip configuration allows varying numbers of layers in a stack. That led to the idea of rotating those layers for radial discharge to ramp up output — a return, in a way, to the cylinder.
To illustrate that, Juan pins down one end of a sample rectangular millimeter design and rotates the free end in a circle, much like rotating a protractor.
Will present at TVC’s Deal Stream Summit
“All of a sudden you have a cylindrical cavity like a pill box,” he says. “It’s still flat but now it looks like a pill box, and I have increased the number of neutrons by one or two orders of magnitude.”
He says that if a neutron can be produced from each bit, “that’s a neutron source that you can use almost anywhere, in medical applications, in sensors for contraband, for nonproliferation.”
Juan presented a paper, “Surface Mounted Neutron Generators,” at the NNSA 2011 LDRD Symposium in Washington, D.C., in July as one of three featured technical speakers chosen by each of the NNSA labs to showcase their top LDRD research activity.
A patent has been filed for the millimeter-size hybrid — hybrid because everything is solid state except a vacuum gap — that would be used for neutron capture cancer therapy. In addition, the project sparked half a dozen technical advances, the team is testing micron-size neutron source arrays built using Sandia’s MicroElectricoMechanical Systems facilities, and it’s initiated commercial technology transfer work.
Technology Ventures Corporation (TVC) accepted Juan’s application to present his work at the April 3 Technology Ventures Deal Stream Summit’s Parade of Posters, which gives researchers an opportunity to talk with possible investors. The nonprofit TVC was founded and funded by Lockheed Martin to help commercialize technology from the national laboratories.
Juan’s vision for the neutron generator of the future is one that uses no tritium and no vacuum, is made in a solid state package and is fabricated at Sandia’s Microsystems and Engineering Sciences Applications (MESA) complex.
“That has very dramatic technology implications and challenges,” he says. “But that’s what I tell people, that’s what the national labs are all about.”