Loss of traditional foam sources akin to removing lumber from housing industry, says surf sage
When the main manufacturer of blanks used for surfboard construction, Clark Foam, closed shop last year, the nation’s $200 million surfboard manufacturing market appeared headed for a wipeout.

Hearing the news, LeRoy Whinnery (8778), who describes himself as “a warm-water surfer” (as opposed to his wife, whom he says “will surf anywhere”), believed he just might have a solution — a foam initially developed to protect sensitive equipment from harsh mechanical environments, TufFoam™.
Now two licensees are evaluating the Sandia-developed foam for this use and scores of inquiries are being explored about this field and other uses, including insulation and structural core applications.
The material is a water-blown close-cell rigid polyurethane foam that features formulations with densities as low as 2 pounds per cubic foot.
News of TufFoam being considered as a potential replacement for surfboard manufacturing spread rapidly through news agencies, television, magazines, newspapers, and trade journals since the licensing opportunity was announced in February.
“It can be used for thermal and electrical insulation, and potentially as a core material for the automobile and aerospace industries,” says Scott Vaupen, who began the commercialization effort in Business Development Support Dept. 8529, where Jim Wilhelm is now handling TufFoam agreements and inquiries. Jim points out the material is unique in its ability to withstand high-rate impact without fracture or loss of structural integrity. In addition, it’s also being considered for use as industrial thermal insulation for liquefied natural gas storage tanks.
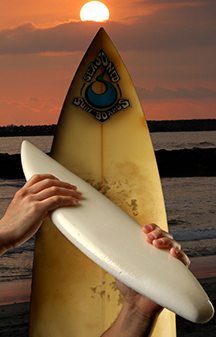
Clark Foam closed its doors suddenly late last year, citing the impact of ever-tightening environmental regulations on the manufacturing of their polyurethane surfboard blanks. The move led to near-panic, particularly in California, by manufacturers and sellers of surfboards who fear they will not be able to find the high strength-to-weight ratio surfboard blanks necessary to make the boards. Surf historian Matt Warshaw, in an article in the Santa Barbara News-Press, said “it’s the equivalent of removing lumber from the housing industry.”
Largely due to its low density, Sandia’s TufFoam might very well fit the bill as a drop-in replacement material. A key feature of TufFoam is that it does not contain toluene diisocyanate (TDI), the chemical used in the production of the polyurethane foam surfboard blanks that is most problematic with respect to environment regulations. Another attractive feature of the Sandia product is that all of the chemicals used to make TufFoam are commercially available in commodity quantities. The material is currently formulated to be processed in a batch mode, but the processing schedule can be modified for machine mixing or injection molding.
So, will a foam developed for America’s nuclear weapons program save the American surfboard industry? Maybe. Leroy hopes so.