Efforts awarded with DOE Weapons Recognition of Excellence Award
Today members of the Power Sources Technology Group in Center 2500 are going about their business doing research and development work that over the years has produced significant improvements to thermal batteries used in nuclear weapons systems. But the memory is still with them of a little more than a year ago when they pushed them-selves to their limits to redesign and produce a lot of MC3323A batteries in record time to support DOE flight tests.“We accomplished something we’d never done before in an extremely short time,” says Larry Moya (2522), thermal battery team leader. For their efforts they were recently awarded the DOE Weapons Recognition of Excellence Award and were commended in a December 2000DOE Quality Assurance Survey Report.
Redesigning a battery and producing a new lot usually takes at least a year and a half — and that’s when Sandia works with commercial companies using the latest automated production equipment But Sandia’s thermal battery team — a research and development group that builds batteries with-out automation — did it in nine months while also working on several ambitious advanced development projects. In 1992, shortly after a major battery DOE procurement/production complex in Pinellas, Fla.,was phased out, DOE requested that Sandia’s battery group become a backup facility with the capability to do in-house thermal battery production for the nuclear weapons program. They were to be called upon only if the major suppliers, Eagle-Picher Technologies of Joplin,Mo., and The Enser Corp. of Pinellas Park,Fla., were unable to manufacture thermal battery lots.
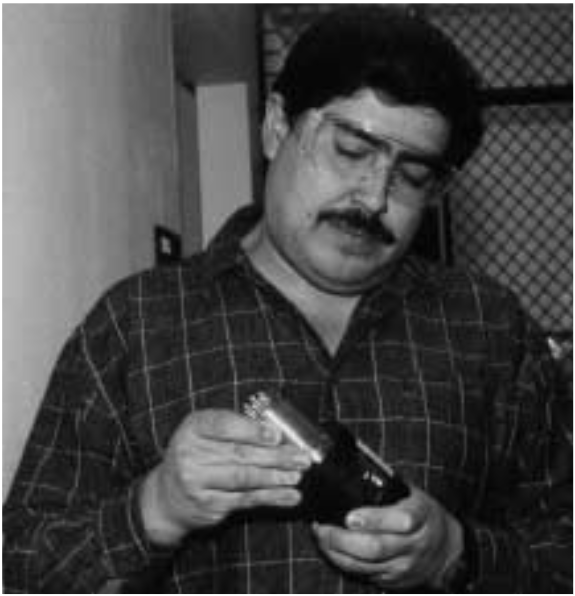
Construction of Sandia’s production lab was completed in1997. The thermal battery team success-fully produced its first lot of 40 MC4152thermal batteries for DOE the following year.“We built those batteries under extreme pressure as well. Budgets were cut towards the end of the program and the schedule was moved up by one month,”Larry says (Lab News, April 24, 1998). “This was to prove our capability as well as produce required WR product.” Sandia was supposed to produce one lot of batteries a year to maintain the production capability,but due to financial considerations, that plan was dropped. In March 1999 the group got a call that was to dramatically change their lives for the next nine months. Because of lot failure problems in batteries for a flight test, Sandia was requested by W80 System Engineering to redesign the MC3323A battery and produce 32 units by October 1999.The primary supplier, Eagle-Picher, could not fit the lot into its schedule. The other company,Enser, could not produce the replacement batteries because it was in the process of moving its facilities.
The task fell to the Sandia backup production lab and the handful of people on the thermal battery production team. Core team members with key responsibilities were Arthur Andazola, Patrick Benavidez, Amelia Sanchez, Joe Garcia, and Frank Soto (all 2522) and Jim Gilbert, Larry Demo, John Guillen, and Frank Lasky (all 2523) .Production staff from Enser who came to Sandia to help build batteries were Rhonda Toy, Patricia Wehinger, Wanda Lawson, and John Brettner. Other groups contributing were Organic Materials Dept. 14172, W80 System Engineering Dept. 2111, Metal Forming, Welding & Explosives Dept.14181, Reliability Assessment & Human Factors Dept. 12335, Quality Engineering/Business Practices Dept. 14408, Shipping, Receiving, and Mail Dept. 10263, Materials Characterization Dept.1822 and DOE/AL.“Because of the short time frame, we had to do the redesign and production in parallel, which is something highly unusual,” Larry says.
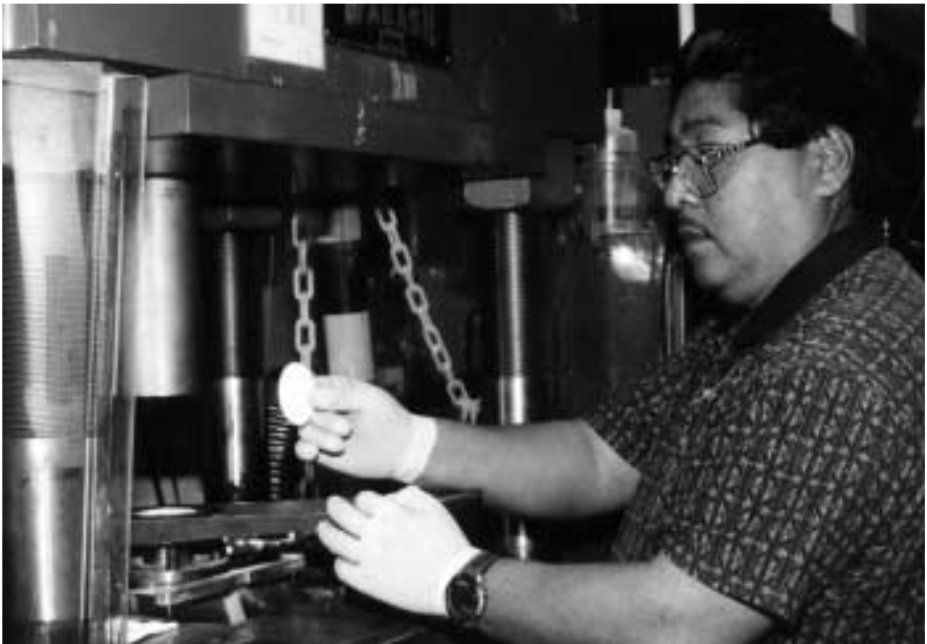
Team members began manufacturing those portions of the batteries that were unchanged. At the same time, others were redesigning parts of the batteries that needed to be reconfigured. The first redesigned prototype was done in a month — by April 1999. By June 1999 sample batteries were sent to the Kansas City Plant and National Testing Systems of Florida for testing.The team completed the redesign and built 72 batteries in nine months. Extras were made to ensure reliability, and the required units as well as additional units to allow the next lot to be moved out by several months were delivered on time in October 1999.“It was an amazing feat,” Larry says. “It took a lot of teaming to make it happen.”