Skunk Works artiste: Sandia robot paints first F-117 Nighthawk at Lockheed Martin’s development facility
A robotic system developed at Sandia has successfully painted the first F-117 Nighthawk fighter inside a hangar at Lockheed Martin’s Advanced Development Projects group, better known as the “Skunk Works,” in Palmdale, Calif.
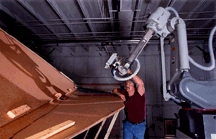
Download 150dpi JPEG image, ‘stealth_pix.jpg’, 1 Mb
Engineers in Intelligent Systems and Robotics Center 9600 designed and built the behemoth ‘bot — the largest Labs intelligent system ever delivered to an outside customer — as part of a three-year, $5.7 million development project for the United States’ F-117 System Program Office (SPO), which has responsibility for maintaining the F-117s.
The system’s two 10,000-lb. rail-mounted robotic arms and one floor-mounted arm will automatically spray a precisely thin radar-absorbent coating onto the skin of each of the nation’s active F-117 Nighthawks, also known as Stealth fighters. The system was delivered to Skunk Works in September 1998. Members of the Sandia team helped install and acceptance-test the system during the following five months. (See “Largest, most complex Labs robot ever delivered” on page 4.)
The robotic system will improve the final finish quality and reduce costs by minimizing the amount of time spent painting and reworking each aircraft, says project leader Larry Shipers (9672).
“With five painters and a masking crew, manually coating a Nighthawk took four and a half days,” he says. “We robotically coated the first aircraft in three days with a smaller crew. Once it’s in a production mode, the system will be faster and provide considerable cost and time savings to the Air Force.”
“Because of the superior performance of the robotic system, we now expect to yield a net cost savings measured in the millions of dollars over the next four years,” wrote Col. Samuel Ryals, Air Force F-117 SPO Director, in a recent memo of appreciation to the Sandia team. “I believe [the team’s] efforts will directly contribute to the F-117’s continued sustainability and combat effectiveness.”
Coatings are blip-resistant
During the Gulf War, US Nighthawks swooped largely undetected through Iraqi airspace at night. The fighter’s angular exterior minimizes reflected signals, increasing the odds that it will be missed by enemy radar.
Adding to the Nighthawk’s radar invisibility is its specially coated skin. The exterior surfaces of the F-117 feature coatings made of radar-absorbent materials. During manufacture these coatings are painstakingly applied to make sure no defects exist. Any slight deviation from the Nighthawk’s exacting coating specifications can result in a blip on an enemy radar screen.
Air Force plans to refurbish its F-117 fleet during the next few years include removing the existing coatings and replacing them with radar-absorbent paint that is easier and less expensive to apply and maintain. In addition, the Air Force wanted the F-117s to feature one exterior coating configuration rather than five different configurations. The F-117 SPO came to Sandia in April 1996 for an automated solution.
Nighthawks are large aircraft — 65 feet long with a 43-ft. wing span — so the first challenge in designing the automated painting system was to find a robot or robots big enough to reach all of the plane’s surfaces, says Larry.
The Sandia painting system features three commercial robotic arms used in US auto factories called the Motoman P8. Two of the arms are mounted on 30-ft.-long rails. A paint nozzle at the end of each of the robotic arms is connected via tubes and wiring to an oversized stainless steel paint can. Cameras and other sensors help a nearby computer plan and guide the robots’ every move.
To design the system, Sandia used a 3-D computer model of the F-117 provided by Lockheed Martin. The model allowed the team to perform a “reachability analysis” of the standard F-117, which helped determine that the system’s two robot-and-rail systems would have to be repositioned on the hangar floor several times to reach the entire aircraft.
Each 10,000-lb. robot-and-rail system is mounted on a specially designed air lift so two people can move its base to desired locations around the aircraft. One robot-rail combo paints the Nighthawk’s top surfaces; the second paints the bottom surfaces. The third floor-mounted, stationary robot paints the Nighthawks’ removable parts like weapon bay doors and rudders.
Unique robot path planning
Each real F-117 is slightly different, so the Sandia team designed a unique feedback system that adjusts for variabilities from aircraft to aircraft.
The Labs approach is based on an automated, on-the-fly path planning system developed at Sandia that uses geometric information about each real Nighthawk gleaned from a pair of stereovision cameras mounted on the end of each robotic arm.
Before painting begins and every time a robot-and-rail system is moved during painting, the computer automatically registers reference points corresponding to three jack stands the Nighthawk is placed on inside the hangar.
The cameras then locate “landmarks” on the F117 corresponding to vertices, or points where the Nighthawk’s angular facets meet. Based on that feedback about the unique geometry of each plane and information about the robot’s reach, joint limits, and other factors, the software generates a path for the robot to follow as it paints.
The feedback system also ensures that the robotic arms don’t violate a six-inch buffer zone around the fighter.
“You never unintentionally touch an aircraft,” says Larry.
The motion-planning software is what allows Sandia to rapidly and inexpensively develop robot systems for small-lot production operations like painting a limited number of aircraft, says Pat Eicker, Director of Intelligent Systems and Robotics Center 9600. “Path planning is the fruit of Sandia’s research in ‘geometric reasoning’,” he says. “Given a task, geometric reasoning gives robots the capability to automatically determine the movements needed to carry out the task, even if the workpieces vary.”
Geometric reasoning capabilities were originally developed with support from the Laboratory-Directed Research and Development (LDRD) program and DOE Defense Programs funding.
Humanlike agility
The Nighthawks’ angularity and the need to keep the paint spray nozzles at exactingly precise distances from the aircraft surface at all times also prompted the Labs team to give the robotic arms almost humanlike agility.
The rail-mounted robotic arms move with seven degrees of freedom, including the three spacial dimensions (x, y, and z) plus roll, pitch, and yaw.
That’s six, which is normal for many manufacturing-type robots, Larry says. The seventh degree of freedom gives the robot the ability to maintain a fixed x, y, z, roll, pitch, and yaw position from multiple poses, he says.
“This is like having an extra elbow to reach around things that are in the way,” he says. “In our case it also gives us the large range of motion along the 30-ft. rail required to coat a large aircraft.”
The system is expected to be certified for full-scale production by mid summer.
Plans are under way to transfer a variety of Sandia-developed robotic technologies to industry. See the March 12, 1999, issue of the Lab Newsfor more about DOE’s roadmap and program plan for advancing robotics and intelligent machines technologies.