Try this.
Get a pair of scissors – a pair of those little snub-nosed kids’ scissors would be perfect.
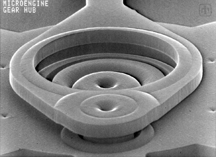
Highly magnified image of a small section of complex micromachine designed by Sandian Steve Rodgers.
Cut out a couple of gear shapes with cogs that will mesh with each other.
Pin the gears down on a flat surface so that the gear teeth line up.
Turn one gear.
Does it turn the other one? Does it ride up over the other one?
When you’ve mastered control of your two paper gears, you’re ready to advance to Phase 2.
Cut out hundreds of interlocking components – gears, actuators, planes – from the construction paper and arrange them so that they’re all linked.
Turn the biggest gear. Do all of the components do what they’re supposed to do? Slide, turn, churn, or whatever?
Pretty complicated, right? Now reduce the scale a little bit, down to, say, the microscopic level, and do it all over again.
Most complex MEMS design ever
If you’ve followed all of the above, you have some idea of the almost maddening complexity of designing a functional microelectromechanical system (MEMS).
Steve Rodgers of Intelligent Micromachine Dept. 1325 says working at the micromachine scale is “practically two dimensional, like cutting gears from sheets of paper and trying to keep them from riding up over each other.”
Steve knows whereof he speaks. He’s just won the 1998 “Excellence in Design” award from Design News magazine for his design of a complex miniature lock for nuclear weapons.
His device, the microelectromechanical Stronglink, was characterized by Design News as “the most complex MEMS system ever designed.” Rodgers’ Stronglink consists of hundreds of components, five electrostatic actuators, and a nine-step, 1,728:1 transmission assembly. The gear teeth on the assembly are about the diameter of a human red blood cell.
The MEMS Stronglink is at this time an advanced conceptual design. It hasn’t actually been incorporated into a nuclear weapon yet.
“Steve is presently working with designers from Electromechanical Engineering Dept. 2643 to realize these advanced concepts in future weapons systems,” says Jim Smith, Steve’s manager in Dept. 1325.
Here’s how Stronglink works: The gear train, driven by a pair of matched electrostatic microengines, slides a pair of mirrors into a certain position that allows an optical-link path to be completed. That process is a critical step in arming a weapon, and the arming can’t proceed unless the Stronglink is correctly activated.
To protect against unauthorized tampering or activation, Stronglink relies on an ingenious system. The gear train proper is missing a couple of gears. These gears, called coupling gears, are slid into place by a second pair of microengines, but only after an irreversible, one-time-only 24-step unlock code is entered into the system. The code moves a tiny pin through a maze. One wrong turn during the 24-step process foils the attempt.
Five-level fabrication
Steve’s Stronglink design was the first ever to use Sandia’s patented five-level polysilicon fabrication process called SUMMiT, or Sandia Ultraplanar Multilevel MEMS Technology.
“The new five-level polysilicon capability,” Steve says, “increases robustness and makes much greater complexity possible. And that means much more functionality – devices that combine all the individual components, such as gears and actuators, to perform a useful task – in this case, a weapon safety device.”
Steve credits the work of Dept. 1325 colleague Jeff Sniegowski with making his design a practical reality.
“Jeff developed the five-level fabrication technology,” Steve says. “Without that, we could develop a lot of individual gizmos, but we need five-level capabilities to tie them all together. Over the years Jeff and I have developed a strong working relationship. Since the drawing set actually defines the fabrication and not the part geometry, close cooperation is essential.”
Steve says work on the MEMS Stronglink started about three years ago, with design of various individual components – transmissions, mirrors, actuators. Back in early 1997, though, Steve said he got the go-ahead to drop everything else and focus totally on the device.
“For about three months I just totally concentrated on this,” he says.
Steve’s Stronglink AutoCAD drawing set contains 1.6 million entities on 17 drawing layers; these are combined to create 14 photolithographic mask levels used in a 240-step fabrication sequence. Because the process is based on semiconductor fabrication technology, hundreds of MEMS devices can be built on a single wafer.
As a Design News winner, Steve will be honored in Chicago next week at a formal black tie awards dinner. He will receive the Design News Excellence in Design medallion and a $5,000 technology award. An article about his design was published in the March 2 issue of Design News, which is read twice monthly by 335,000 engineers who design products ranging from autos to spacecraft.