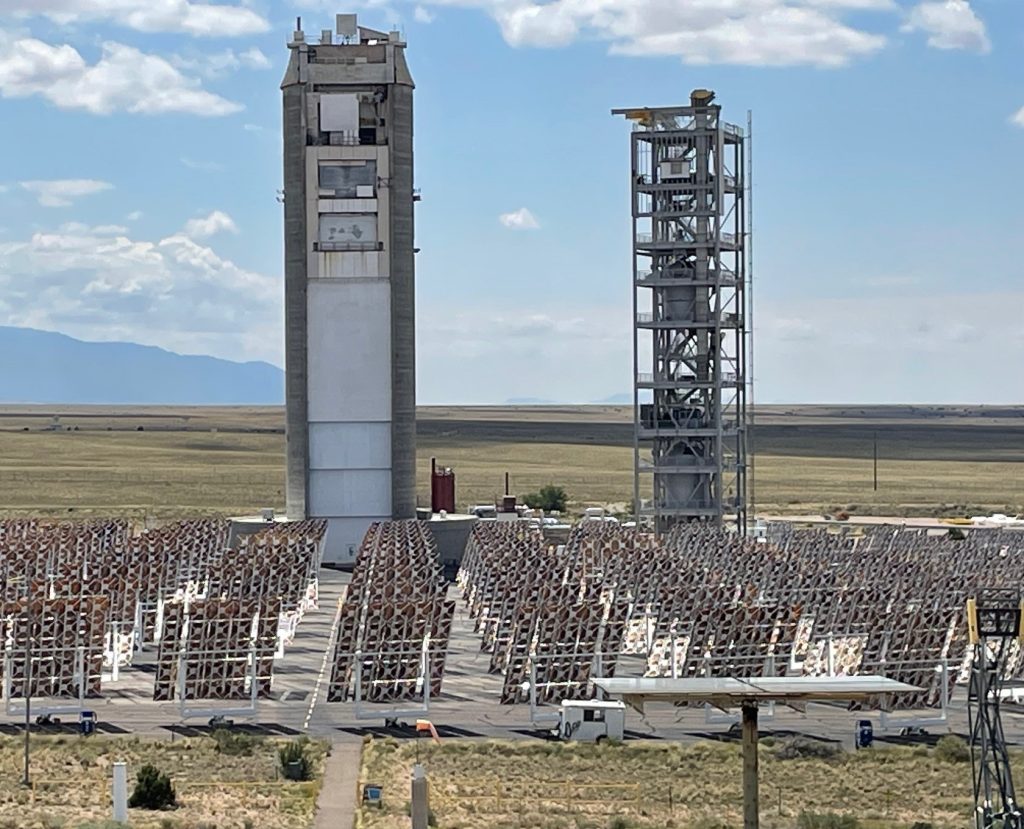
Generation 3 Particle Pilot Program (G3P3)
As part of a $70 million multi-year DOE Generation 3 CSP Systems program that began in 2018, the U.S. Department of Energy announced a Phase III, $25 million award to Sandia National Laboratories to build, test and demonstrate a next-generation Concentrating Solar Thermal Power (CSP) plant at the National Solar Thermal Test Facility (NSTTF) in Albuquerque, New Mexico. The award was announced on March 25, 2022, during a webinar hosted by DOE Secretary Jennifer Granholm.
The objectives of the Gen 3 Particle Pilot Plant project are to design, construct and operate an integrated system that de-risks a next-generation, particle-based concentrating solar power (CSP) technology to produce clean, utility-scale electricity with long-duration energy storage. The multi-MWt G3P3 system will use the existing field of heliostats, or mirrors, at the NSTTF to concentrate sunlight on to a particle receiver that: 1) heats particles to over 700 °C, 2) enables at least six hours of particle-based energy storage, and 3) heats an supercritical phase CO2 working fluid to ≥ 700°C while demonstrating the ability to meet cost and performance goals.
In Phases 1 and 2, Sandia successfully de-risked key elements of the proposed G3P3 by improving the design, operation and performance of key particle component technologies including the receiver, storage bins, particle-to-sCO2 heat exchanger, particle lift and data acquisition and controls. Modeling and testing of critical components led to optimized designs that meet desired performance metrics. Detailed drawings, piping and instrumentation diagrams and process flow diagrams were generated for the integrated system, and structural analyses of the assembled tower structure were performed to demonstrate compliance with relevant codes and standards. Instrumentation and control systems of key subsystems were also demonstrated. Together with Bridgers & Paxton, Bohannan Huston Inc., and Sandia Facilities, a 100% G3P3 tower design package with stamped engineering drawings suitable for construction bid was developed.
The contract for G3P3 was awarded to Summit Construction in August of 2022. The tower was erected between January 2023 and April 2024. As of December 2024, the particle-based solar components have been lifted into the tower and are being assembled and energized. The 2 MWt Falling Particle Receiver has been ground tested with particles at ambient temperature. The storage bins have been installed. The storage bin insulation is nearing completion using a combination of microporous insulation, Calcium Silicate, and High-Alumina Silica firebrick with thermocouples embedded between each layer. The heat exchanger is being fabricated and will be received in early 2025. The sCO2 circulating loop has been successfully ground tested, and is being assembled in the tower by NSTTF technologists. All particle duct work and control valves are being installed and initialized.
Contact: Jeremy Sment
G3P3 Field Testing
Stay Tuned! G3P3 field testing is planned to begin in Summer of 2025.
Other Related Projects:
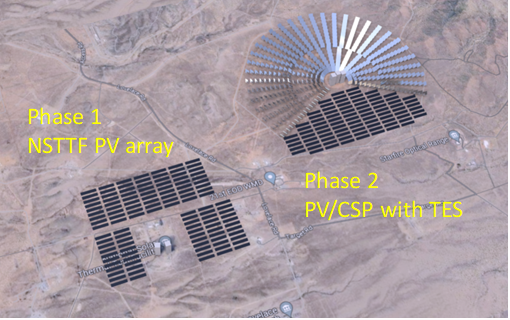
Advanced Solar Generation and Resiliency Deployment (ASGARD) Front End Engineering and Design (FEED) Study
Sandia is investigating a major solar energy deployment capable of providing 100% of the combined energy needs of Kirtland Air Force Base, including the Sandia National Laboratories and National Nuclear Security Agency tenants. In 2024, a computational model was developed on Sandia’s High-Performance Computing infrastructure to run advanced energy balance calculations to determine how much solar energy could be harvested on available KAFB land. The outcome of this analysis determined that the lowest cost and highest yield system would be hybrid, with daytime photovoltaic energy generation that delivers AC power directly to the Sandia grid and converts all excess DC power above the current load to Lithium-ion batteries. Once the batteries are fully charged, any remaining PV energy is converted to heat that is stored in a particle-based thermal energy storage system. Additionally, a concentrating solar power plant will be used to provide low-cost heat to the TES system during the day.
A FEED study was commissioned by the Solar Energy Technology Office at the U.S. Department of Energy to reduce cost and deployment uncertainty associated with the first-of-kind particle-based CSP system at this scale. The scope of the study will involve down selection of the key technology options for the CSP portion of the project such as the type of turbine and heat exchanger, and work with an Engineering, Procurement, and Construction firm to better estimate the cost of tower construction, field deployment, storage bin construction and system integration. The study will also establish a supply chain by submitting drawings and specifications to vendors, and where no vendor currently exists for first-of-kind components, such as falling particle receivers, we will provide fabrication drawings to custom vendors.
Compact Counter Flow Fluidized Bed Heat Exchanger (CCFB-HX)
HelioCon
- Developing strategic core capabilities and infrastructure to support high-performance heliostat manufacturing, validation, and optimization and facilitate industry’s ability to design, manufacture, install, and operate central receiver heliostat fields with higher technical and economic performance
- Ensuring that these capabilities are readily available to industry, and meeting their needs
- Funding research on new technologies with significant potential to improve heliostat field economic performance
- Forming U.S. centers of excellence focused on heliostat technology to restore U.S. leadership in heliostat research, development, and validation
- Promoting workforce development by encouraging student internships and postdoctoral positions, the formation of a HelioCon early career scientist group to promote networking, and highlighting existing training and educational programs in heliostat design, production, and operation.
Contact: Margaret Gordon
HoTPROP
Long Term Particle Wear
The Long Term Particle Wear project investigates surface wear in packed bed and fluidized bed particle systems at high temperatures for concentrating solar power relevant materials, and use that data to validate numerical models that can predict material lifetimes for given temperature and particle flow regimes. Using solid particles as energy storage and transfer media is seen as one of the most practical ways to achieve the temperature targets needed to drive advanced high efficiency power cycles and generate alternative fuels via solar thermochemistry, while simultaneously driving down the cost of thermal energy storage. However, one of the biggest engineering challenges of next generation concentrated solar power plants is the handling of bulk materials at elevated temperatures. The current particle of choice for Sandia National Lab’s Generation 3 Particle Pilot Plant is primarily made of sintered bauxite. These particles have excellent optical and thermophysical properties for CSP applications. These particles also have the potential to cause severe wear in chutes, valves, heat exchangers, and other high temperature CSP components. These models can be used for CSP plant design where expected material lifetimes are measured in 105-106 hours. Furthermore, this project will develop two lab-scale particle wear test rigs which will be capable of simulating accelerated particle wear and will add to the capability of Sandia’s National Solar Thermal Test Facility as a particle-based CSP research and development facility.
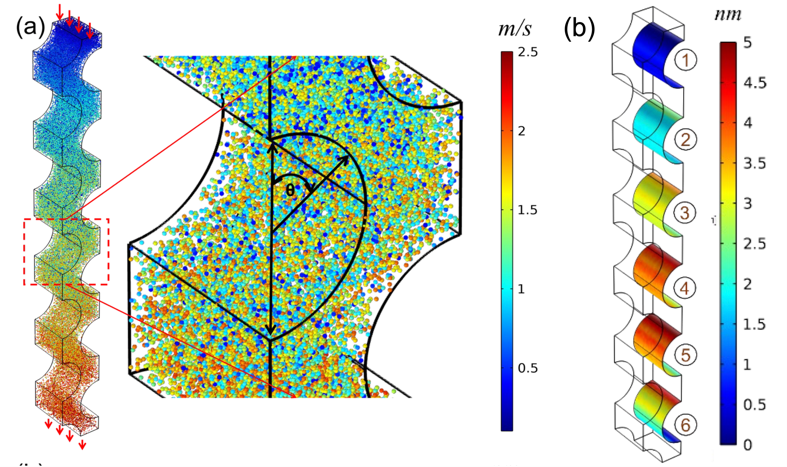
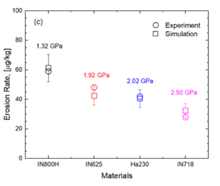
Contact: Matthew Sandlin
Particle Curtain Generating Valve (PCGV)
When falling particle receivers are used to directly heat particles using concentrated solar power, they generate a particle curtain that cascades through an open cavity. This curtain can be approximately 10 meters wide and 6 cm thick. The goal of the Particle Curtain Generating Valve (PCGV) project is to develop a modular valve that can be strung together to create a continuous particle curtain that can span over 10 meters and operate at 900 °C.
Ultra High Operating Temperature SiC-matrix Solar Thermal Air Receiver (HOTSSTAR)
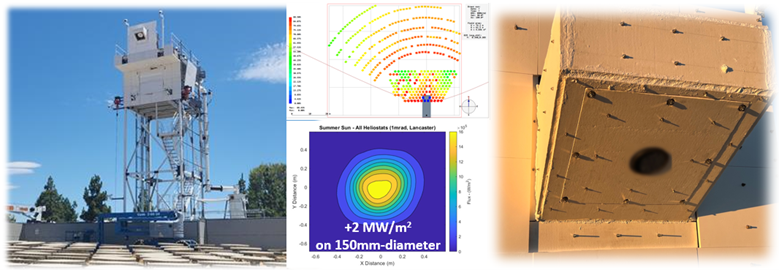
Contact: Ken Armijo